정책과 동향
독일, 자동차 업계 소재 혁신은 벌써 이만큼
작성자 : 편집부
2022-06-08 |
조회 : 3369
- 다양한 산업 연계 속 친환경, 경량화 및 혁신 신소재 개발 줄이어
- 높은 강성 및 경량화 신소재로 차후 금속 부품 대체 전망, 지속 가능한 경량화 신소재에 대한 관심도 부상
- 국내 기업, 대체 소재 개발을 위시한 자동차 소재 혁신으로 신규 밸류체인 진입이 중요한 시점
독일 자동차 업계, 전기차 대량 생산을 위한 확고한 행보
숄츠 총리는 지난해 12월 초 신정부 출범 첫 성명에서 2030년까지 총 1,500만 대 전기자동차 보급을 목표로 한다고 밝혔다. 독일 정부의 전기자동차 정책 기조와 더불어 산업계도 일찌감치 확신에 찬 행보를 보이고 있다. 많은 완성차기업이 이미 오래전부터 E-모빌리티를 지향하고 있고 내연기관차에 대한 단계적 퇴출은 이미 정해진 시나리오로 알려져 있다.
지난 2월 8일 독일 자동차 전문 매거진 Automobilwoche가 개최한 웨비나에 연사로 초대된 전 아우디(Audi) 기술부 이사 메르텐스(Peter Mertens)에 따르면, “자동차 기업이 E-모빌리티에 대해 초점을 두는 것은 절대적으로 올바른 길”이라고 생각하며, “특히 유럽에서는 내연기관의 퇴출이 예상보다 훨씬 빠르게 다가오고 있다”고 전하고, 또 “연료 전지가 장기적으로 여전히 큰 미래가 있다고 확신한다”고 밝혔다.
메르텐스는 “이는 특히 원래 큰 배터리가 장착되어야 하는 대형 럭셔리 SUV에서 레인지 익스텐더(Range-Extender: 순수 전기자동차에, 주로 내연기관과 발전기가 기계적으로 결합된 발전설비를 추가로 장착한 형식)와 결합해 추천할 만하며, 이는 매우 현실적인 안이라고 생각한다”고 말했다.
메르텐스와 더불어 연사로 참석한 포르쉐(Porsche) 개발부 이사, 자동차 부품 제조기업 엘링클링어(ElringKlinger) CEO 등도 향후 모빌리티 시장의 판도는 시장 내 ‘고객의 선택’이라는 데 공감하면서도 승용차 부문에서 전기차가 갖는 지배적인 역할을 강조하고, 이 외에도 수소(특히 상용차용), E-Fuel(합성연료) 등도 각 적용 분야에서 대안이 될 수 있을 것으로 내다보고 다른 나라 역시 유럽의 행보를 따를 것으로 예견했다.
뉴모빌리티(New Mobility), 혁신 소재 개발이 뒷받침해야!
이처럼 업계 내 전기차 및 배터리 기술 개발에 대한 역량이 집중되고 있는 것에 못지않게 차량용 소재 경량화 및 혁신 소재 기술 개발도 눈에 띄게 진전하고 있다. 신소재에 대한 기대감도 있지만, 무엇보다 무게 감소가 E-모빌리티에서 아주 중요한 역할을 하기 때문이다.
이미 지난 2019년 12월 포드(Ford)가 맥도날드(McDonald’s)와 협업 하에 원두를 로스팅하고 남은 커피 폐기물로 헤드라이트 하우징을 제조한다고 밝히며, 획기적인 신소재*로 주목을 끈 데 이어, 랑세스(Lanxess), 바스프(BASF) 및 크라이부르크(Kraiburg) TPE 등과 같은 독일의 선도 화학기업도 다양한 솔루션 찾기에 열심이다.
* 포드는 이 소재를 사용해 이전보다 최대 무게가 20% 덜 나가는 자동차부품 생산과 함께 부품 제조에 사용되는 에너지도 1/4 감축하고자 한다.
재활용 소재를 활용한 신소재를 비롯해 알루미늄 폼과 미세한 유리구슬로 최적화된 플라스틱 등의 혁신 소재로 경량 구조를 구현하는 움직임도 눈에 띈다. 더 나아가 훨씬 기술적으로 진보한 카본도 2024년 상용화될 것으로 기대되고 있다.
이 기업들은 소재 개발로 차체의 무게 감소에 기여할 수 있는 기회로 볼 뿐만 아니라, 신소재 기술 개발을 통해 지속가능성을 제고하고자 하며, 이를 위해 고객과의 협업에도 적극적인 행보를 보이고 있다.
랑세스(Lanxess), 폐유리를 활용한 엔지니어링 플라스틱 신소재로 주목
특수 화학물질 제조기업인 랑세스는 배터리 시스템, 전기 구동 트레인 및 충전 인프라와 관련된 구성 요소가 신소재인 듀레탄(Durethan®) 및 포칸(Pocan®)*으로 만들어지고 있다고 전한다.
* 랑세스에 따르면, 듀레탄(Durethan)은 폐유리를 재활용한 유리섬유 강화 폴리아미드6 소재로 특히 뛰어난 강도와 강성이 특징으로 자동차 산업에서 활용도가 높으며, 친환경 공정으로 탄소발자국 감축 효과가 있다고 한다. 포칸(Pocan)은 우수한 난연성과 내화학성을 지녀 배터리 매니지먼트 콘트롤러 제조에 사용된다고 한다.
랑세스는 바이오 또는 재생 원료를 기반으로 최소 50%의 재활용 플라스틱(Rezyklat) 또는 플라스틱으로 구성되거나 기존의 ‘스콥블루(Scopeblue)’ 브랜드 제품보다 CO2 배출량이 적어도 50% 이상 낮은 제품을 결합하였다. 이를 통해 탄생한 제품이 듀레탄 브랜드 폴리아미드(PA) 6 화합물로 중량 기준 유리섬유 함량이 60%이며, 유동성이 뛰어나다고 한다.
이 재료는 무엇보다도 자동차 프론트 모듈, 브레이크 페달 및 오일 팬은 물론 전기차용 경량 배터리 트레이 등에도 사용되고 있다. 이 제품의 제조 과정에서는 원재료의 92%가 지속 가능한 대안으로 대체되나 기존에 제조된 제품과 동일한 물성과 품질을 갖는다고 한다. 이는 특히 글로벌 지속가능성 및 탄소 인증제도인 ISCC+(International Sustainability and Carbon Certification)**을 획득했다. 여기서 지속 가능하게 생산되는 시클로헥산(Cyclohexane)은 폴리아미드 생산에 사용되는데, 이를 위해 랑세스는 석유 회사인 BP와 공급 계약을 체결했다.
** 이는 EU의 재생에너지 지침에 부합하는 글로벌 지속 가능 친환경 소재 인증제도로, 원료에서부터 생산과정, 최종제품까지 친환경성을 점검해 부여된다. 재생 유리섬유를 보강재로 적용한 PA6 플라스틱 듀레탄 에코(Durethan Eco) 제품 출시에 이어 재활용 유리섬유로 강화된 폴리부틸렌테레프탈레이트(PBT) 엔지니어링 플라스틱 ‘포칸 에코(Pocan Eco)’를 선보이는 등 친환경 소재에 수요에 발맞춰 친환경 플라스틱 제품군을 확장해 나가고 있다.
하벨 메탈폼(Havel metal foam), 혁신 소재 개발로 경량화 선도
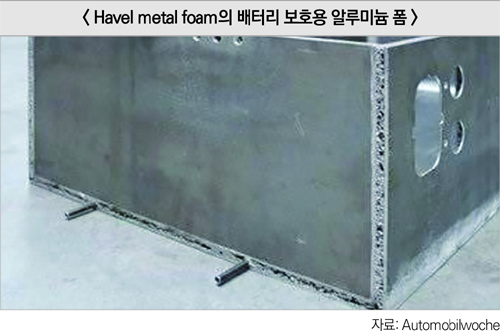
알루미늄 소재로 만든 부품은 기존 철강 소재 대비 50%나 무게를 경감할 수 있고 일례로 알루미늄 폼은 이미 20여 년 전 카르만(Karmann)이 개발해 선보인 바 있다.
재료 전문가들은 훨씬 더 가벼운 부품 소재 개발에 대한 많은 아이디어를 갖고 있으나 시리즈 생산으로 가는 길은 멀다는 게 업계 내 지론이었다. 몇 년 전까지만 해도 알루미늄 폼은 아우디 Q7 트렁크 그물망과 페라리 스파이더 430의 충돌 흡수 장치와 같이 아주 예외적인 경우에만 사용되었으며, 여기에는 금속 폼 보강 요소가 사이드 스커트에 설치되기도 했다.
독일 브란덴부르크(Brandenburg)주에 자리 잡은 하벨 메탈폼(Havel metal foam)의 대표이사 슐러(Friedrich Schuller)는 “금속 폼은 매우 가벼울 뿐만 아니라 매우 안정적이기 때문에 사고 시 배터리를 보호하고 온도 조절을 개선해 배터리 수명을 연장한다”라고 말한다. 이 회사는 프라운호퍼 공작기계 및 성형기술 연구소(IWU)와 제조 공정을 함께 개발하였다.
연구소 경량구조개발 담당자인 Mr. T는 “폼은 국소 보강재로서 잠재력이 있다”고 말하고, “현재 자동차에서 알루미늄 폼의 적용이 가격 문제로 둔화되고 있으나 대규모 생산을 통해 낮출 수 있다”고 내다보고 있다. 예를 들면, 알루미늄 폼은 추가 금속 시트 또는 플라스틱 인서트가 설치되는 곳뿐만 아니라 충돌에 대비해 보강이 필요한 모든 곳에서 가능성을 제공한다는 것이다. 다른 밀도와 강도가 다른 지점에서 생성되는 방식으로 구성 요소를 제조할 수 있기 때문이라고 한다.
이 소재를 배터리 하우징으로 사용하는 경우 열저장 재료를 생산 중에 직접 투입하거나 열 관리 라인을 알루미늄 폼에 통합할 수 있다는 이점도 갖고 있다고 한다.
미세하게 작은 유리구슬로 플라스틱 최적화
독일 바이에른(Bayern)주 소재 크라이부르크(Kraiburg) TPE는 새로운 경량 폴리머로 이미 첫 시리즈 응용기술 개발에 성공했다. 경량 TPE(Thermo Plastic Elastomer: 열가소성 엘라스토머)는 3M이 이러한 응용 분야를 위해 특별히 제조하는 일반 열가소성 엘라스토머(외력의 영향을 많이 받는 고분자 화합물)에 현미경으로 작은 유리구슬을 내장해 만든다.
크라이부르크에 따르면, “이를 통해 깃털처럼 가볍고 얇은 벽이나 우수한 표면과 밀도가 0.7~0.9g/㎤인 기계적으로 탄력적인 성형 부품을 생산하는 데 사용할 수 있다”고 한다. 경량 TPE는 이미 루프 레일, 바닥 매트 및 내부의 소음 차단 요소에 사용되고 있다.
또한 해당 업체의 관계자에 따르면 이 소재는 우수한 밀봉 특성을 가지는 데 관련 응용 분야에서 중량을 50% 줄일 수 있으며, 이미 다수의 자동차 제조기업에서 활용되고 있다고 한다.
바스프(BASF), E-모빌리티용 플라스틱 개발
독일 화학분야 대기업 BASF는 E-모빌리티에 역량을 집중하고 있다. 바스프의 플라스틱은 무엇보다도 난연성, 전기 절연성, 열 전도성 및 냉각수 호환 재료가 필요한 배터리 부문에서 주로 사용되고 있다.
또한 충전 인프라와 관련해 바스프는 까다로운 조건을 견디는 동시에 색상, 표면 마감 및 자외선에 대한 안정성과 내구성을 제공하기 위해 고온에서 우수한 기계적 성능과 높은 치수 안정성(dimensional stability; 온도·습도 변화에 대하여 재료의 치수, 형상이 안정하며 변화하지 않는 성질)을 가져야 한다고 했다.
동사의 플라스틱은 전기 모터 및 플러그 연결용 드라이브 트레인 및 케이블 관리 분야에서 사용되며, 차량의 열 관리 및 소음 진동 성능을 개선하기 위해 사용되고 있다.
특히 동사의 마케팅·물류·기능성 소재 분야 프린츠(Michael Prinz) 이사에 따르면, 이 회사는 고객과 긴밀한 공동 제작 파트너십을 체결하고 있으며, 디자인과 시공 지원, 재료 선택에 대한 컨설팅, 시뮬레이션 및 테스트 지원, 시리즈 개발에 있어 고객과의 협력을 통해 추진하고 있으며, 자동차 가치사슬에 대한 깊은 이해를 갖고 임하고 있다고 한다.
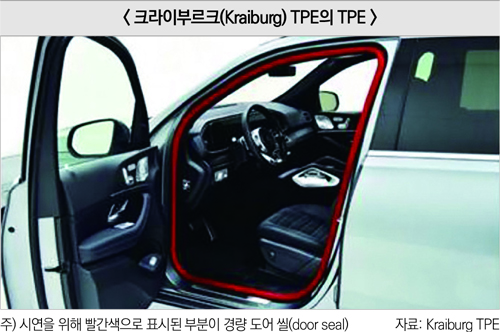
알루미늄 경량화 소재에 이어 탄소 소재 2024년 상용화 예상
여전히 탄소 및 알루미늄에 대한 응용 분야에서는 추가 개발이 이뤄지고 있고, 이는 경량화와 관련해 이 소재가 여전히 잠재력이 있다는 것을 시사한다. 특히 자동차 산업계는 모빌리티의 미래를 구축해 나가기 위해 지속적으로 경량, 고강도 및 지속 가능하게 생산되는 알루미늄에 의존하고 있는데, 알루미늄의 추가 적용 가능성이 부각되고 있다.
2021년 프랑스에 본사를 두고 있고, 독일 내 자회사이자 생산 공장을 운영 중인 알루미늄 전문기업 콘스텔리움(Constellium)과 세계 최대의 알루미늄 재활용 기업인 美 노벨리스(Novelis)가 발족한 비영리기관 알루모빌리티(Alumobility)의 연구 결과, 알루미늄을 사용하면 차체 생산 시 무게를 줄일 수 있다고 한다.
Alumobility는 차세대 알루미늄 도어와 전체가 알루미늄으로 만들어진 구조적 B-필러(pillar) 관련 기술을 이미 개발했으며, 연구에서 나온 설계 솔루션을 통해 알루미늄은 제조업체에 비교적 저렴한 비용으로 대량 차량용 다른 재료와 효과적으로 경쟁할 수 있다고 확신한다고 밝히고 있다.
이 기관의 부회장이자 콘스텔리움 소속 부이사인 클라크(Jack Clark)는 “Alumobility의 기술 작업은 특히 전기 자동차에서 가볍고 지속 가능한 알루미늄의 역할을 강화할 것이며, 동시에 알루미늄의 재활용을 늘리고 제품 총 수명 주기의 탄소 배출량을 줄일 것”이라고 강조했다.
경량화 분야 선도기업인 Audi는 e-Tron에 알루미늄을 투입해 이미 차체 제조에서 높은 무게 경감 효과를 보고 있다. 다른 여러 종류의 강철로 만들어진 기존의 차체 무게가 193.8kg인 반면, 전체 구성 요소가 알루미늄인 경우 113.2kg으로 42%의 무게 경감 효과가 있다고 한다.
도어와 강철 플랫폼을 포함한 전체 차체 구조로 계산하면, 무게가 481kg에서 399kg으로 감소한다. 이로 인해 알루미늄 소재로 구성된 차체는 역 80%에 이르는 일반 강철로 제조된 e-Tron 본체보다 약 1/6 가볍다고 한다.
이외에도 독일 자동차 매거진 Automobilwoche은 최근 美 사우스 앨라배마 대학교가 고성능 나노 탄소섬유 복합 소재 ZT-CFRP 개발사례를 들며, 학계에서 충격 손상에 취약하고 전기 및 열 전도성이 좋지 않은 탄소 소재의 약점을 개선해 나가고자 하는 노력이 진행되고 있다고 전한다.
Automobilwoche의 전문가 플뤠렉케(Klaus-Dieter Flörecke)는 자동차의 경량화 구조는 여전히 높은 잠재력을 갖고 있으며, 이는 현재 탄소 소재와 알루미늄 분야의 다양한 혁신으로 드러나고 있다고 밝히고 있다.
플뤠렉케는 매니지먼트 및 IT 컨설팅 기업 MHP*의 R&D 혁신 부서의 수석 컨설턴트 키름제(Sebastian Kirmse)와의 인터뷰를 통해 “나노 입자가 풍부하고 탄소섬유강화 플라스틱 복합재는 2024년 시장에 출시될 것”이라고 한다.
* MHP는 산학 협업 하에 재료 제조 공정을 개발하고 상용화 파트너 역할을 하고 있다.
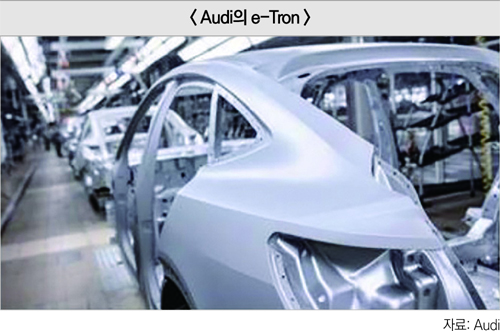
탄소 나노섬유와 탄소섬유의 결합은 기계적, 전기적, 열적 에너지를 전도하는 복합재의 기능을 향상시키며 무게 이점도 있는 것으로 알려져 있다.
키름제는 “우리는 실험실 테스트에서 기존 탄소재료에 비해 최대 30%의 무게 절감을 달성했다”고 전하고, 엔진룸의 높은 내열성 때문에 이와 같이 기능이 향상된 탄소의 적용 분야로 적합할 것으로 보고 있다고 한다. 아울러 전기자동차에서도 높은 활용도를 예상하며, 이는 “상대적으로 무거운 배터리 때문에 무게를 다른 영역에서 줄여야 한다는 것을 의미한다”고 전하고, “새로운 경량화 소재가 필요할 것”으로 내다보고 있다. 다만, 비용 문제가 여전히 난제로 지적되고 있다.
독일항공우주센터(DLR), 경량 구조로 차량 효율성 제고 기술 개발
독일항공우주센터(DLR)의 차량 콘셉트 연구소(DLR Institute for Vehicle Concepts)는 2022년 2월 16일과 17일 개최된 학술회의 ‘MaterialPlus Auto 2022’에서 미래의 여행용 리무진을 선보였다. IUV(Interurban Vehicle)로 불리는 이 차량은 무게가 250kg에 불과한 탄소섬유 강화 플라스틱으로 만들어진 차체를 갖고 있으며, 미래 장거리용 차량으로 개발 중이다.
이 차량은 적층제조방법을 사용해 공간과 무게를 절약하는 방식으로 구성 요소를 차량 구조에 직접 통합한 것으로, 기능적으로 통합된 경량 구조는 차량의 무게를 줄여 효율성을 높였다. 충돌 안전성을 높이고, 지속 가능성과 경량 구조와 편안함을 결합한 디자인으로 고도의 경량 구조를 갖춘 연료 전지 플러그인 하이브리드인 IUV는 최대 충전거리가 1,000km로 장거리 달성이 가능하다.
DLR 연구원들은 고성능 열저장 시스템으로 이 전기차를 위한 고효율 난방 기술을 제시하였는데, 기능 원리는 포켓 손난로(pocket warmer)의 원리와 유사하다. 금속 합금이 저장 매체 역할을 하고 이 시스템은 차량 배터리와 독립적으로 작동하기 때문에 높은 난방 출력으로 인해 더 이상 겨울철 주행 거리가 줄어들지 않는다고 한다.
이 기술은 또한 매우 작고 가벼운 난방 시스템을 가능하게 하기 때문에 이러한 저장 시스템은 지역 대중교통에서 사용하기에 특히 적합하다고 한다.
독일항공우주센터(DLR)의 차량 콘셉트 연구소 소장인 지프케스(Tjark Siefkes) 교수는 “경량 구조는 차량의 효율성을 더욱 높일 수 있다고 강조하고 핵심 질문 중 하나는 미래의 자동차를 무엇으로 만들까? 또는 새로운 재료를 어떻게 처리할 수 있나?”라고 전하며, 미래 차량 소재의 다양성을 언급하였다.
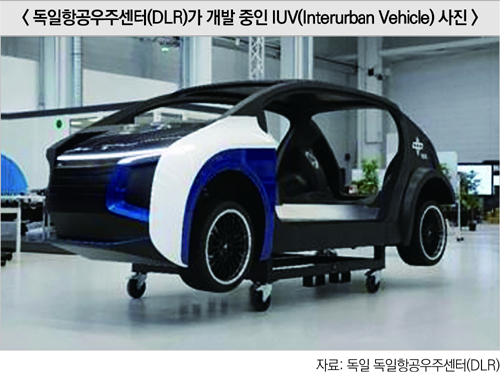
지속 가능 경량화 신소재 연구개발도 활발
지난 2021년 12월 독일 뷔르츠부르크(Würzburg)에서는 경량화 회의가 열렸다. 미래 자동차에서 철강 생산의 지속가능성 개선 및 철강의 역할에 대한 논의 외에도 섬유 복합재의 재활용 문제도 다뤄졌다.
프라운호퍼 IGCV(주조, 복합재료 및 가공 기술) 연구소의 마니스(Frank Manis)는 자동차 산업에서 재활용 탄소섬유의 사용에 대한 다양한 프로젝트의 연구 결과를 발표하면서 재료가 환경에 미치는 영향을 최대한 낮추는 또 다른 방법은 이미 사용한 재료를 재사용하는 것이라고 강조하며, 섬유 복합재의 재활용을 하나의 대안으로 제시했다.
그중 하나로 재활용 탄소섬유로 만든 부직포가 언급됐는데, 프라운호퍼는 이를 위해 프로젝트 그룹은 U-프로파일과 도어 모듈을 사용하여 시뮬레이션을 시연했다.
마니스에 따르면, 무엇보다도 이러한 작업을 통해 재료 리스트가 축적되었는데, 재활용 탄소섬유로 만든 220개의 부직포 및 접착테이프가 현재 문서화돼 있으며, 2022년부터 라이선스 모델에 대해 데이터베이스에 접근이 가능하다고 한다.
개발자는 이 데이터를 사용하여 보다 빨리 재료를 선택하고 첫 번째 프로토타입을 설계할 수 있다고 한다. 이를 통해 볼 때, 현재 경량화 기술 연구개발에서는 지속 가능성을 고려한 연구도 활발히 진행되고 있으며, 또 다른 새로운 혁신 섬유의 노하우가 축적되고 있다고 볼 수 있다.
시사점
경량화 구조가 신규 차량 설계의 일부로 자리 잡아 나가고 있다. 엔지니어링 플라스틱은 E-모빌리티, 뉴모빌리티의 경량화에 효과적으로 대개 내연기관차보다 훨씬 많은 무게가 나가는 전기차나 수소연료전지차 보급과 함께 개발에 탄력을 받고 있으며, 대용량 배터리 무게를 감축하게 되면 주행 거리가 확장되는 효과가 있어 간과할 수 없는 부품 기술이다.
이는 높은 강성과 가벼운 무게를 동시에 만족시키는 신소재로 급부상하고 있으며, 차후 기존의 금속 부품을 대체할 것으로 예상되고 있다. 특히 재활용 소재 비율을 높인 지속가능성 소재 개발은 지속적으로 확대될 것으로 전망되며, 폐자재를 활용해 에너지를 절감하면서 CO2 배출량 감축에 유리한 일거양득의 공법 활용 역시 지속적으로 주목을 받게 될 것으로 기대된다.
즉 새로운 소재의 경량화 효과 외에도 재활용 등을 통한 탄소 배출량 감축 및 지속 가능한 신소재 개발을 위한 소재의 경제성도 함께 고려해야 할 부분으로 지적되고 있다.
특히 현재 장기화되고 있는 러-우크라이나 사태로 인한 부품공급의 지연이 생산의 하방 요인으로 작용하고 있는 시점에서, 대체 부품 개발을 위해 아직 극복해야 할 장애물은 존재하나 업계 전문가들은 지속 가능한 경량 구조가 매우 중요해질 것이라고 확신하고 있고, 기후 보호와 자원 효율성 개선을 위한 노력은 이러한 발전을 더욱 촉진할 것으로 예상된다.
더불어 이러한 신소재는 시장 내 지속가능성 트렌드에 부응하며, 자동차 제조기업에서도 새로운 판매 기회로 작용하고 있다. 업계와 소비자의 지속 가능한 제품에 대한 수요 역시 꾸준히 증가하고 있기 때문이다.
국내 기업 역시 소재 개발 및 상용화를 통해 새로이 구축되는 밸류체인에 진입 기회를 노려볼 수 있는 중요한 시점으로 이는 향후 전기차 수요 증가에 따른 편승효과가 가장 기대되는 분야 중 하나라 할 수 있다. 이는 더 나아가 소재의 지속가능성 확대와 함께 현재 중요한 화두가 되고 있는 ESG* 경영 기조에 발맞춰 나가는 선도 기업의 행보이기도 할 것이다.
* 기업의 비재무적 요소인 환경(Environment)·사회(Social)·지배구조(Governance)를 뜻하는 말로 장기적 관점에서 이러한 기업 가치와 지속가능성을 중시하는 기업의 경영 원칙을 의미하며, 글로벌 자금시장 내 신 투자기준으로 자리 잡고 있다. 현재 경량화 기술 개발이 기후 친화적 혁신이라 할 수 있는 ‘혁신 소재와 지속 능성’의 두 마리의 토끼를 잡을 수 있기를 기대해 본다.
자료: Automobilwoche, Automobilwoche 개최 웨비나 참석, Handelsblatt,
각 기업 홈페이지, electrive.net, industrie.de, leichtbauwelt.de, 관계자 인터뷰,
automobil-industrie.vogel.de및 KOTRA 프랑크푸르트무역관 자료 종합
