기술과 솔루션
탄소나노튜브 섬유의 제조 및 응용
작성자 : 편집부
2021-06-23 |
조회 : 7981
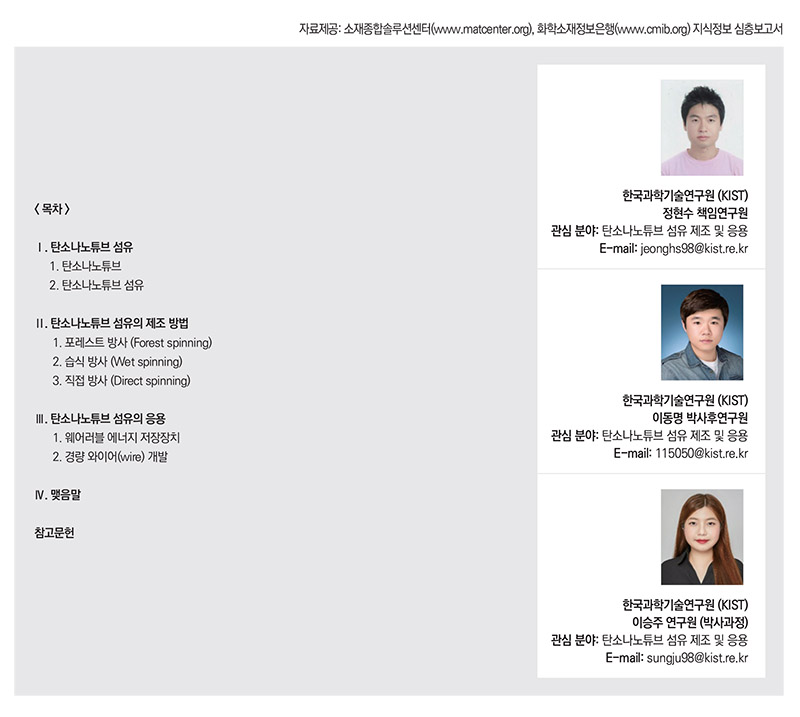
Ⅰ. 탄소나노튜브 섬유
1. 탄소나노튜브
탄소나노튜브는 탄소 원자 사이의 sp2 공유 결합으로 형성된 긴 원통형의 나노 구조체로, 벽에 수에 따라 단일 벽(single-walled), 이중벽(double-walled), 그리고 다중벽(multi-walled) 탄소나노튜브로 분류할 수 있으며, 육각 고리 배열 상태에 따라서 암체어(armchair), 지그재그(zigzag), 그리고 키랄(chiral) 구조로 나눌 수 있다. (그림 1)1-3 탄소나노튜브는 탄소섬유, 구리, 다이아몬드와 같은 상용화된 재료들보다 기계적 강도, 전기전도도, 그리고 열전도도가 높으며 유연하고 가벼운 특성을 갖는다. 4-7
이러한 탄소나노튜브의 우수한 특성으로 인해 전계 효과 트랜지스터, 센서, 리튬 이온 배터리, 슈퍼 커패시터, 연료 전지 및 나노 복합체와 같은 다양한 응용 분야에 적용할 수 있다. 하지만 탄소나노튜브는 개개의 튜브들 사이에 강한 반데르발스 인력으로 인해 물이나 유기용매에 쉽게 분산되지 않으며, 길이가 짧아 산업에서 탄소나노튜브를 광범위하게 사용하기에는 제한이 있다.
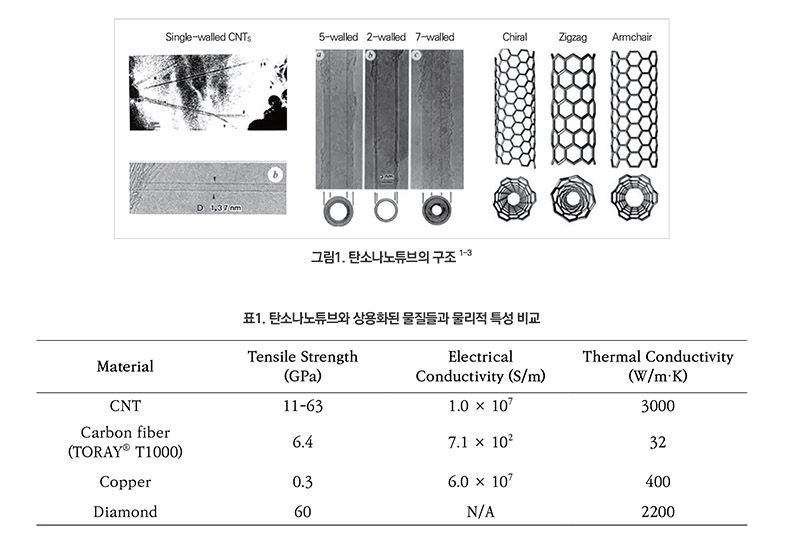
2. 탄소나노튜브 섬유
탄소나노튜브 섬유는 미시적 탄소나노튜브들이 축 방향에 따라 정렬하여 밀집된 거시적인 1D 형태의 조립체이며, 탄소나노튜브가 모여 번들을 형성하고 번들이 모여 탄소나노튜브 섬유를 형성하는 계층 구조를 갖고 있다.
(그림 2)8-9 탄소나노튜브는 기계적, 전기적, 열적 특성이 매우 우수하기 때문에 섬유로 제조하게 되면 유리 섬유, 아라미드 섬유, 탄소섬유와 같은 기존의 섬유 재료의 물성을 뛰어 넘는 고성능 섬유 재료로 사용될 수 있다.
또한, 탄소나노튜브 섬유는 가볍고 유연하기 때문에 우주, 자동차, 선박과 같은 운송 분야에서 획기적인 연비 절감이 가능하며, 웨어러블 디바이스, 웨어러블 에너지 소재 등 많은 분야에서 고기능성 섬유로 응용이 가능하다. 최근 연구에 따르면, 탄소나노튜브의 비 인장강도는 5.5 N/tex로 탄소섬유(Toray T1100G, 3.9 N/tex)보다 높으며, 비 전기전도도는 5640 S m2/kg로 구리(6150 S m2/kg)와 비슷한 수준에 이르렀다. 10-11
그러나 아직까지도 탄소나노튜브 섬유의 물성은 개별 탄소나노튜브의 물성을 구현하고 있지 못하며, 고품질의 소량 생산으로 합성된 탄소나노튜브들로 달성한 물성이므로 아직까지 상업성이나 경제성이 부족하다.
특히 탄소나노튜브 섬유의 물성은 탄소나노튜브 내에서 sp2 C-C 결합의 특성보다는 탄소나노튜브 사이의 상호작용에 의해 결정되기 때문에 개별의 탄소나노튜브의 물성이 발현되지는 못한다.
예를 들어, 탄소나노튜브 섬유의 파손은 탄소나노튜브 사이의 미끄러짐에 의해 발생하며, 전도는 탄소나노튜브 내의 전자 이동과 탄소나노튜브 사이의 호핑 메커니즘에 의해서 일어난다.
12-15 따라서 탄소나노튜브 섬유의 고강도 및 고 전기전도성은 개별 탄소나노튜브를 높은 밀도로 정렬시켜 마찰력을 최대화하고 접촉 및 접합 저항을 최소화하여야 한다.
순수하게 탄소나노튜브로만 이루어진 섬유를 생산하는 방식은 크게 3가지로 대표되며, 각 방법에 대해 아래에 기술하겠다.
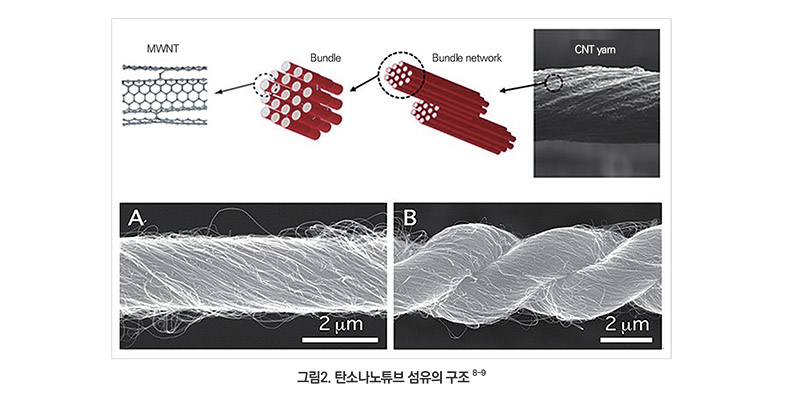
Ⅱ. 탄소나노튜브 섬유의 제조 방법
1. 포레스트 방사 (Forest spinning)
포레스트 방사는 기판에서 높은 공간 밀도로 수직으로 성장된 탄소나노튜브 번들에서 섬유를 생산하는 방식이다. 수직 성장된 탄소나노튜브 번들의 한쪽 끝을 끌어당기면 탄소나노튜브들 사이의 반데르발스 인력에 의해 인근의 탄소나노튜브 번들이 함께 따라 나오면서 섬유 형태로 뭉쳐지는 방식이다. (그림 3)16-17
이 방법은 기판 및 촉매들의 제어가 용이해 합성되는 탄소나노튜브의 직경이나 길이 조절이 가능하다. 이를 통해 집합 구조체인 섬유 물성과 개별 탄소나노튜브의 연관성을 조사하고 연구하기에 적합한 방법이다. 그러나 모든 탄소나노튜브 집합체가 섬유로 방사할 수 있는 것은 아니며, 집합체 형태가 방사와 밀접한 관련이 있기 때문에 탄소나노튜브 섬유로 방사할 수 있는 조건을 충족시키는 탄소나노튜브 집합체를 합성하기 어렵다. 18-20
일반적으로 50μm에서 2㎜ 길이의 탄소나노튜브로 구성된 매우 밀집도로 수직 정렬된 탄소나노튜브 집합체만 탄소나노튜브 섬유로 방사할 수 있다. 21 또한, 합성되는 탄소나노튜브 자체의 결정성이 좋지 않고 방사(spinning) 시 탄소나노튜브의 정렬도와 밀집도가 낮아 좋은 물성을 기대하기 어렵다. 무엇보다도 기판 크기에 의존하므로 원천적으로 생산성에 제약을 받으므로 산업적으로 응용하기에는 한계가 있다.
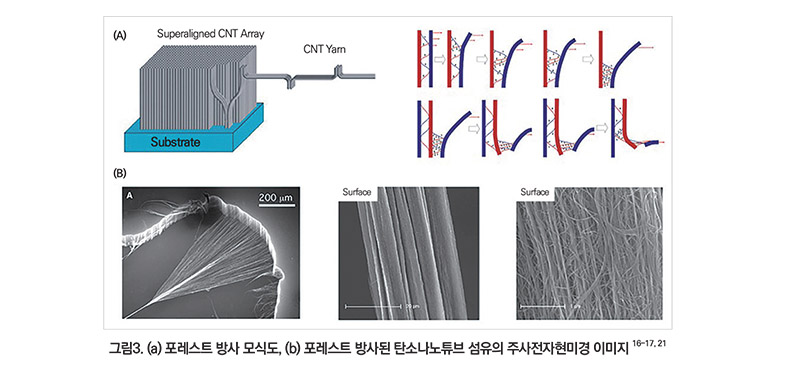
2. 습식 방사 (Wet-spinning)
습식 방사는 이미 산업화되어 있는 방사법으로서 매우 높은 농도의 용액 도프(dope)를 제조하고 노즐을 통해 응고액에 투입하여 상 분리를 기반으로 고체화된 섬유를 연속생산하는 방식이다.
아라미드(aramid) 섬유가 대표적인 습식 방사 기반 산업화된 섬유이다. 습식 방사는 이미 산업화된 공정이지만 원재료라고 할 수 있는 매우 높은 농도를 가지는 고분산된 도프를 만드는 것이 가장 기초이자 핵심기술이다.
탄소나노튜브는 강한 반데르발스 인력으로 인해 용매 분산이 일반적으로 어려우며 이를 해결하기 위해 탄소나노튜브의 표면을 기능화 또는 계면활성제를 이용하여 분산성을 높이는 연구가 많이 진행 되어왔다. 22 그러나 이 방법들은 어느 정도 수준의 분산이 가능하지만 방사 가능한 농도 증가에 한계가 뚜렷하며, 개질을 통한 탄소나노튜브 품질 저하 또는 계면활성제로 인한 정렬도와 밀집도 하락 등 탄소나노튜브 섬유의 물성을 저하시키는 단점이 있다.
순수하게 탄소나노튜브만을 이용하여 고분산/고농도의 도프를 제조하기 위해서는 일반 분산 상태가 아닌 액체와 고체의 중간 상인 액정(liquid crystal) 상을 경유하여야 한다.
탄소나노튜브 액정 상은 농도 구배에 따라 발현이 가능한 유방성(lyotropic) 액정으로 분류가 되며, 액정 상이 발현되면 물질 간의 반발력과 인력이 조화를 이루어 집합적 거동(collective behavior)이 나타나는 상태가 된다.
이러한 집합적 거동은 하나의 도메인(domain)을 형성하게 되며 도메인 내에서 정렬을 통한 밀집도가 향상이 되어 농도 증가가 가능하게 된다. 23-25 탄소나노튜브 액정 상을 발현시키기 위한 기본 조건은 어떠한 첨가제 없이 이들의 반데르발스 힘을 이겨낼 수 있는 반발력을 부여하는 것이다.
현재까지 연구된 용매 중에 유일한 열역학적 자발적 분산 용매로는 클로로황산(chlorosulfonic acid)이 가장 효과적으로 알려져 있다. 24
산에서 탄소나노튜브의 분산은 양성자화(protonation)에 의한 튜브 사이의 정전기적 반발력에 의해서 일어나게 되며 이런 양성자화를 가장 효과적으로 전달하는 용매가 바로 클로로황산인 것이다. 하지만 모든 탄소나노튜브가 클로로황산에서 양성자를 받아 자발적 분산이 되는 것이 아니고 결정성, 즉 결합이 없는 탄소나노튜브가 효과적이다. 25
양성자화 조건은 결정성이지만 액정 상 발현에 있어 다른 큰 요인은 바로 탄소나노튜브의 높은 종횡비(aspect ratio)이다. 콜리이달 이론에 (Onsager 이론 (φiso⇀bi = 3.34 (aspect ratio)-1)에 의하면 종횡비가 높을수록 상전이 즉 액정 상이 발현되는 농도가 낮아지게 된다. 그러므로, 높은 종횡비를 갖는 탄소나노튜브는 클로로황산에 분산되면 분자 수준의 공간 제약이 생겨 튜브의 퍼콜레이션(percolation)이 일어나 튜브들이 이방성 네마틱 액정을 형성한다.
이 액정 용액은 탄소나노튜브가 규칙적으로 배열하고 있고, 동시에 액체와 같은 유동성을 갖게 되어 고분산/고농도 액정 도프가 된다. 제조된 도프를 노즐을 통해 응고제(e.g. 아세톤)에 방사하면 노즐에서의 전단력과 아세톤에서의 빠른 응고에 의해서 정렬도와 밀집도가 높은 탄소나노튜브 섬유를 제조할 수 있다. (그림 4)11, 26-29
또한, 분산 전 탄소나노튜브의 정제 과정을 통해 합성 중에 생성된 비정질 탄소와 철 불순물을 제거할 수 있기 때문에 탄소나노튜브 섬유의 순도를 높일 수 있다. 산을 이용한 습식 방사 방법은 이미 Kevlar와 같은 고강도 섬유를 제조하기 위해 산업에서 이용되고 있으므로 탄소나노튜브 섬유의 대량 생산으로의 적용 역시 쉬울 것으로 예상된다.
탄소나노튜브 액정섬유의 가장 큰 장점은 액정 상을 이용하므로 높은 밀집도와 배향도를 가지는 섬유 구조체 제작이 가능하고 결정성이 높은 탄소나노튜브들로 이루어져 있어 전도성이 매우 뛰어나다. 탄소섬유에 비해 전기전도성이 최소 10배에서 100배 뛰어나며, 최근에는 습식 방사로 만든 탄소나노튜브 섬유의 비 인장강도는 2.94 N/tex로 탄소섬유(Toray T1100G, 3.9 N/tex)보다 낮지만, 비 전기전도도는 5640 S m2/kg로 구리(6150 S m2/kg)와 비슷한 것으로 보고되고 있다. 11, 29
하지만 탄소나노튜브의 정제부터 분산, 방사까지 멀티스텝으로 이루어진 공정으로 인해 에너지와 시간이 소모되며, 무엇보다 액정 방사 가능한 탄소나노튜브가 결정성이 충분히 높아야 하는 점은 제약으로 작용한다.
결정성 이외에 섬유 물성의 결정적 역할을 하는 높은 종횡비까지 동시에 갖춘 고결정/높은 종횡비 탄소나노튜브의 합성은 아직까지 보고된 사례가 지극히 없고 있더라도 극소량의 실험실 레벨 수준이라 파괴적인 물성을 보유하고 있는 탄소나노튜브 액정섬유의 산업화는 시간이 걸릴 전망이다. 27
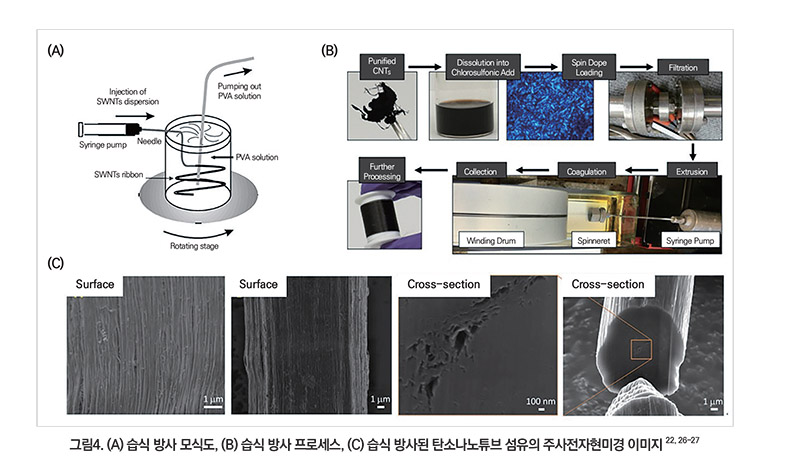
3. 직접 방사 (Direct spinning)
직접 방사는 명명에서도 알 수 있듯이, 탄소나노튜브가 합성되는 동시에 섬유화가 바로 가능한 one-step 섬유 제조 방식이다. 탄소나노튜브 합성을 위한 전구체, 촉매들을 기상으로 동시에 고온의 수직 반응기로 주입하여 탄소나노튜브를 합성하게 되는데 반응이 수초 이내로 매우 짧으며 일반적인 파우더와 달리 직접 방사법에 의해 만들어진 탄소나노튜브는 에어로겔 형태를 띄게 된다.
이런 에어로겔 형태의 탄소나노튜브들을 반응기 하단에 물과 같은 비친화적인 용매들로 통과시키면 소수성을 띄는 탄소나노튜브들의 자발적 응축이 일어나게 된다.
응축이 일어난 탄소나노튜브들을 winder 부분에서 끌어주게 되면 섬유 형태로 연속적으로 감기게 된다. (그림 5)30 그러므로 이 방법은 탄소나노튜브를 합성과 동시에 섬유화시키기 때문에 빠르고 간단하여 경제성이 뛰어나며 긴 종횡비를 가지는 탄소나노튜브들로 이루어진 섬유의 연속 생산이 가능하다.
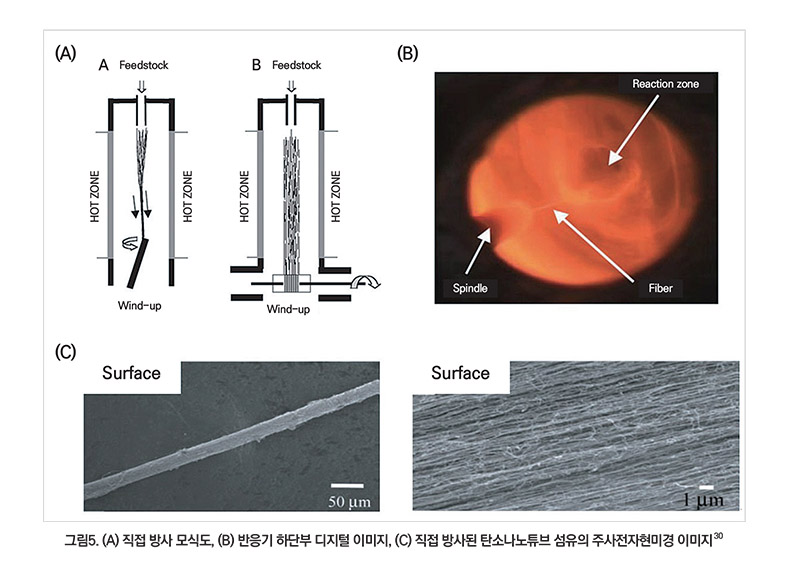
그러나 섬유로 응축되는 힘이 부족하여 섬유의 내부 밀집도와 정렬도가 습식 방사 섬유에 비해 많이 떨어져 물성이 습식 방사 섬유에 비해 열위에 있다. 또한, 탄소나노튜브의 빠른 합성이 장점이 되지만, 이는 역설적으로 메커니즘 분석이 어려우며 기상상태에서 반응이 일어나므로 불안정하고 불균일한 유체 흐름에 의한 영향이 합성 제어에 많은 요인으로 작용한다.
마지막으로 전구체와 촉매의 잔류물인 비정질 탄소, 그리고 철 불순물이 기본적으로 포함되어 있어 섬유 물성을 저하시키고 있다. 언급한 많은 단점을 해결하기 위해 연신비 조절, 유체역학 모사, 반응기 설계, 정제 등 많은 연구가 진행되고 있지만, 제조 단계에서 섬유의 좋은 물성을 나타내기 쉽지 않아 제조 후 후처리를 하는 연구들이 주를 이루고 있다.
직접 방사로 만든 탄소나노튜브 섬유의 정렬도와 밀집도를 향상시키기 위해서 물리적, 화학적 후처리 방법이 연구되고 있다. 31-34 대표적으로 mechanical densification 방법은 탄소나노튜브 섬유를 물리적 압착을 통해서 짧은 시간 안에 공극을 제거하여 급격한 물성 향상을 나타냈으며, cross linking 방법은 탄소나노튜브 사이에 반데르발스 힘보다 더 강한 공유 결합을 형성시켜 강도를 향상시켰으며, liquid infiltration 방법은 탄소나노튜브 섬유 내에 유기용매 또는 산을 침투시켜 탄소나노튜브 번들의 정렬도를 향상시키고 침투 용액의 쌍극자 모멘트와 표면 장력을 이용해서 공극을 줄임으로써 물성을 향상시켰다.
대부분 후처리 방법들은 의미 있는 구조와 물성의 향상을 달성하기 위해서 상당한 처리 시간이 필요하기 때문에 빠르게 섬유 제조 가능한 직접 방사의 가장 큰 장점을 결국 상쇄시키게 된다. 무엇보다 개발된 방법들은 연속 후처리가 불가능하므로 연구적으로 의미가 있을지라도 산업적 관점에서는 한계가 있다.
최근에는 습식 방사 방법과 직접 방사 방법의 장점을 결합한 하이브리드 방식의 후처리 공정 방식이 개발되었는데, 이 방식은 제조된 직접 방사 탄소나노튜브 섬유를 매우 빠르고 효율적으로 섬유 내부 구조를 재정렬시킬 수 있다. 10, 35-36
직접 방사된 탄소나노튜브 섬유를 탄소나노튜브의 분산을 위한 열역학적 용매로 알려진 클로로황산에 투입하면 탄소나노튜브 섬유 내부로 클로로황산이 빠르게 침투하여 탄소나노튜브를 양성자화 함에 따라 탄소나노튜브가 팽창하게 된다.
이 상태에서 탄소나노튜브 섬유의 적절한 힘을 가해 연신을 하게 되면 얽힌 탄소나노튜브들이 연신 방향으로 재배열되어 축 방향으로의 정렬이 개선된다. 이때 제조 단계에서 포함된 매우 큰 공극들도 연신에 의해 없어지게 된다.
그다음 탄소나노튜브를 습식 방사와 같이 아세톤 응고제에 넣으면 용해도 차이에 의한 상 분리에 의해 클로로황산이 압출되면서 탄소나노튜브 섬유는 고체화가 빠른 시간 안에 일어난다. (그림 6) 최종적으로 정렬도와 밀도가 높은 탄소나노튜브 섬유가 만들어지게 된다.
이 방법을 생성된 탄소나노튜브 섬유의 비강도는 5.5 N/tex로 탄소섬유(T1100G, 3.9 N/tex)와 습식 방사로 제조된 탄소나노튜브 섬유(2.94 N/tex)보다 높으며, 비 전기전도도는 2270 S m2/kg로 스틸보다(1340 S m2/kg) 높은 것으로 나타났다. 10, 11, 35
개발된 후처리 공정의 또 다른 의의는 언급한 공정들이 수 분 내로 이루어지며 연속 처리가 가능하여 공정성이 뛰어나다는 장점이 있다는 것이다. 후처리 된 직접 방사 섬유는 습식 방사 섬유에 비해 강도 면에서는 우위에 있고 전기전도성에서는 열위에 있다.
전기전도성이 열위인 이유는 직접 방사로 만든 섬유의 정렬도, 밀집도, 그리고 무엇보다 섬유를 구성하는 탄소나노튜브의 결정성이 떨어지기 때문이다. 합성 기술의 발달로 정렬도, 밀집도, 그리고 결정성이 높은 탄소나노튜브 섬유 제조가 가능하게 된다면 후처리 기술을 이용해 많은 물성의 향상을 기대할 수 있을 것으로 보인다.
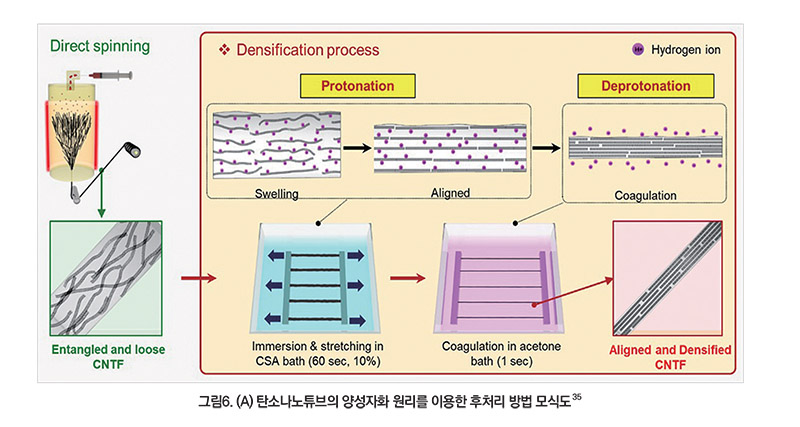
Ⅲ. 탄소나노튜브 섬유의 응용
탄소나노튜브 섬유는 기계적 강도, 전기전도성, 열전도성, 경량, 유연성 등 거의 모든 부분에서 우수한 물성을 나타내는 차세대 슈퍼섬유이다. 37-40 특히 다른 고기능성 섬유(e.g. 탄소섬유 및 그래핀 산화물 섬유) 들과 비교했을 때, 유연성과 전기전도성이 뛰어나 웨어러블 센서 39-42, 엑츄에이터 43-44, 웨어러블 에너지저장 및 생산 소재 45-48 등 다양한 분야에 활발히 응용되고 있다.
여러 응용 분야 중 가장 파괴적인 응용 분야는 구리 도선 대체 초경량 전력 수송용 케이블 개발이며, 영국 및 미국을 중심으로 활발히 연구가 진행 중이다. 이번 보고서에서는 에너지 저장장치 및 경량 도선 개발 응용 분야에 대해 소개하고자 한다.
1. 웨어러블 에너지 저장장치
미래사회의 핵심 디바이스 중 하나인 웨어러블 디바이스는 신체에 부착하여 컴퓨팅 행위를 할 수 있는 모든 전자기기를 지칭하며, 다양한 스마트 기기들과 연결을 통해 데이터 정보 수집이 가능하고 휴대성과 사용 편리성이 높아져 확산속도가 높아지고 있다.
웨어러블 디바이스를 구동하기 위한 에너지원으로서 섬유 형태가 가장 이상적이며 의류의 관점에서 위화감 없이 직조 및 매듭을 통해 실제 착용이 가능한 안정성 있는 유연하고 강하며 전도성이 매우 좋은 전극 소재가 필요하다.
탄소나노튜브 섬유는 GPa 대의 높은 기계적 강도 및 MS/m 대의 우수한 전기전도도, 그리고 50% 대의 매듭 강도 즉, 유연성을 보유하고 있어 웨어러블 에너지저장 소재로 가장 적합한 후보 물질이다. 하지만 탄소나노튜브 섬유는 활성비표면적이 작기 때문에 자체적으로 저장 소재로 쓰이지 않고 나노소재 및 활성 물질들과의 복합 구조화를 통해 저장용량을 증가시키고 있다.
호주 Woollongong 대학의 Wallace 교수 연구팀은 탄소나노튜브 섬유 표면에 이산화망간 (MnO2) 나노 플레이크를 전기증착 방식으로 복합화한 섬유를 개발하였다. 49 탄소나노튜브/MnO2 복합섬유는 152F/g의 비정전용량 값을 나타냈으며, 202W/kg의 파워 밀도에서 14.1Wh/kg의 에너지 밀도 값을 보여주었다.
또한, 10,000번의 반복 작동에도 심각한 용량 저하 없이 안정적으로 구동되었다. 최근, KIST 연구팀은 탄소나노튜브 섬유/폴리아닐린 고분자 복합구조체를 Hot spot을 이용한 초음파 처리 방식으로 개발하였다. (그림 7)
개발된 복합섬유는 738F/g(1A/g 충·방전 속도) 높은 정전용량값을 보였으며 매우 빠른 충·방전속도(100A/g)에서도 604F/g의 높은 용량을 유지했다. 50 또한 15,000번의 구부림에도 정전용량이 85% 이상 유지되었으며, 매듭을 지어도 정전용량의 변화가 없음을 보여주어 웨어러블 디바이스의 에너지저장 소재로 적합함을 보여주었다.
상기 경우들처럼 탄소나노튜브 섬유를 충실히 전극으로 이용한 사례가 있는 반면, 섬유 자체의 비표면적을 증가시켜 활성을 높이는 연구도 진행되었다.
대표적으로는 다른 기능성 나노소재들과 복합 방사를 통해 탄소나노튜브 섬유의 비표면적을 조절하였다. Wallace 교수 연구팀은 그래핀 산화물과 복합 방사를 통해 비표면적을 늘려 순수 탄소나노튜브 섬유 대비 약 40%에 더 증가된 비정전용량을 달성하였다. 51 더 나아가, 탄성 고분자를 복합섬유에 코팅하여 8배까지 늘어나는 동시에 138F/g 비정전용량 값을 달성하여 신축성이 확보된 웨어러블 에너지저장 소재를 개발하였다.
이처럼, 저장용량의 증가뿐만 아니라 탄소나노튜브 섬유의 유연성과 기계적 강도를 바탕으로 신축성 고분자와의 복합화 혹은 섬유의 공간적 배치, 설계 등 다양한 방식으로 신축성, 구부림 등 웨어러블 에너지 소자에 필요한 기계적 특성을 확보하는 연구가 활발히 진행 중이다. 35
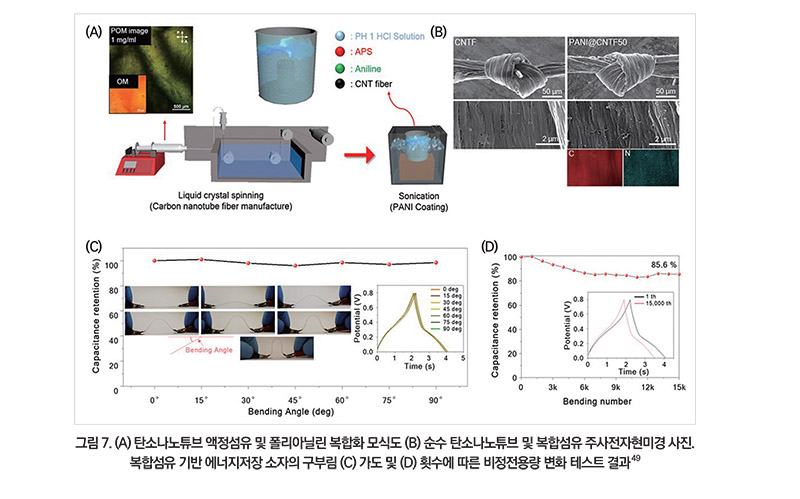
2. 경량 와이어(wire) 개발
탄소나노튜브 섬유의 우수한 전기전도성을 바탕으로 구리 도선을 대체하는 연구가 미국, 유럽, 일본 등 주요 선진국을 중심으로 주도적으로 개발이 이루어지고 있다.
구리는 비중이 9g/cc 정도로 매우 높고 표피효과, joule 열에 의한 저항 상승 및 주변 환경에 의한 부식, 한정된 자원 등 많은 단점이 존재하여, 전 세계적으로 이슈화되고 있는 4차 산업혁명의 스마트 팩토리 및 친환경 대체에너지의 안정적인 공급망 구축, 그리고 항공, 선박, 전기자동차, 우주산업에서의 연비향상 등 다양한 미래산업에서 요구하는 케이블의 경량화, 컴팩트화, 대용량화 트렌드에 대응하기 어렵다.
탄소나노튜브 섬유는 초경량 고전도성 케이블 개발에 있어 가장 유력한 후보 물질로 주목받고 있다. 하지만 결정적으로 전기전도성이 구리(58 MS/m) 대비 현재 약 1/10~1/6 수준에 있어, 아직까지는 순수한 탄소나노튜브 섬유를 이용하여 구리 도선을 대체하기 이른 수준이다.
이에 많은 연구자들이 탄소나노튜브 섬유와 금속의 혼합을 통해 부족한 전기전도성과 허용전류(ampacity)를 증가시키는 연구전략을 취하고 있다. 금속과의 복합화는 크게 2가지 형태로 나눌 수 있는데, 코어(CNT 섬유)/쉘(금속) 타입과 금속이 섬유 내부까지 복합화된 하이브리드 타입이다.
Li 교수 연구팀은 탄소나노튜브 섬유 표면에 2μm의 정도의 구리를 코팅하여 일반 대기 분위기에서 9.1×104A/㎠의 허용전류 값을 얻어냈으며, 이는 순수 구리와 유사한 수준이다. 52 코어/쉘 타입이 아닌 내부에 구리를 침투시킨 탄소나노튜브 복합섬유의 경우, 코어/쉘 타입보다 좀 더 낮은 6.3×104A/㎠ 허용전류 값을 나타냈으며, 그 원인으로는 내부의 구리들이 연결되지 않아 전도성 채널이 제대로 형성이 되지 않았기 때문이다. 53
구리의 내부 채널 형성 및 복합섬유의 전하 및 열전달에 관한 구체적인 연구로서, KIST에서는 직접 방사된 탄소나노튜브를 모태로 구리를 단계적으로 섬유 내부에 전기 도금하여 각 단계를 정밀 분석하였다.
연구에 따르면, 탄소나노튜브 섬유는 전력 수송 시 발생하는 구리의 joule heating을 효과적으로 방열시키는 역할을 하며 구리는 전도체 역할을 한다. 구리가 전도성 채널을 섬유 내부 전체에 걸쳐 형성하였을 경우 일반 구리 대비 약 50배에 가까운 107A/㎠의 최대 허용전류 값을 얻을 수 있었다. 54
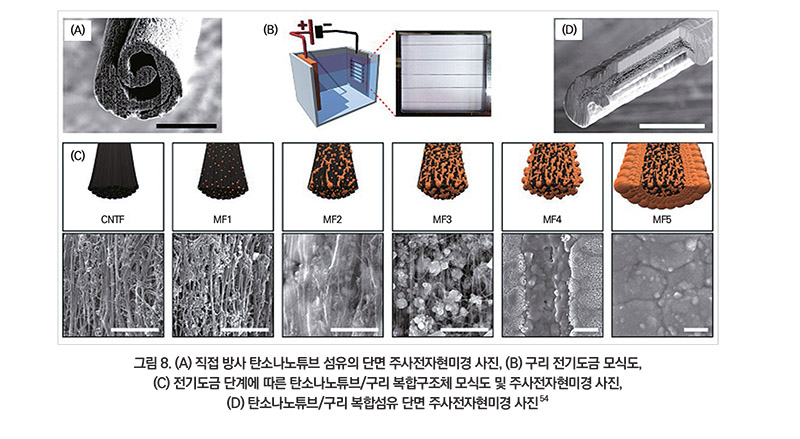
Ⅳ. 맺음말
탄소나노튜브 섬유는 경량, 고 전도성, 고 열전도성, 고강도 물성을 모두 보유하고 있는 차세대 슈퍼섬유로서 탄소섬유를 뛰어넘을 수 있는 유일한 소재로 알려져 있으며, 실험실 레벨에서는 뛰어난 물성들이 검증되었다.
탄소나노튜브 섬유를 제조하는 방식은 크게 3가지이나 생산성 및 산업적 관점에서 바라봤을 때, 연속 생산이 가능한 습식 방사와 직접 방사법이 높은 TRL(Technology Readiness Level)을 달성할 수 있는 방법들이다.
2가지 방식들 기반으로 현재 영국, 이스라엘, 미국에서 spin-off된 벤처들이 산업화를 시도하고 있다. 한국은 서울대학교 포항공과대학교, 숭실대학교 한국과학기술연구원 등 학연을 중심으로 연구개발이 이루어지고 있으며, 최근에는 다양한 산업계에서 개발 및 응용 가능성을 검토 중이다.
이처럼 탄소나노튜브 섬유는 이제 실험실 수준에서 산업화를 가기 위한 개발(Development) 단계에 진입하였다. 하지만, 탄소섬유에서도 알 수 있듯이 가격경쟁력 확보와 확실한 응용처를 찾는 것이 관건이다. 이에 국방 및 우주 등 가격경쟁력 압박을 덜 받는 하이테크 분야와 구리 도선 대체와 같은 파급력이 매우 큰 분야에서의 개발이 집중될 것으로 예상된다.
그동안 많은 나노 소재들의 산업화 실패를 반면교사 삼아, 탄소나노튜브 섬유는 개별 탄소나노튜브에 가까운 우수한 물성과 공정성, 그리고 가격경쟁력을 동시에 확보해야 우리 실생활에서 쓰이는 모습을 볼 수 있을 것이다.
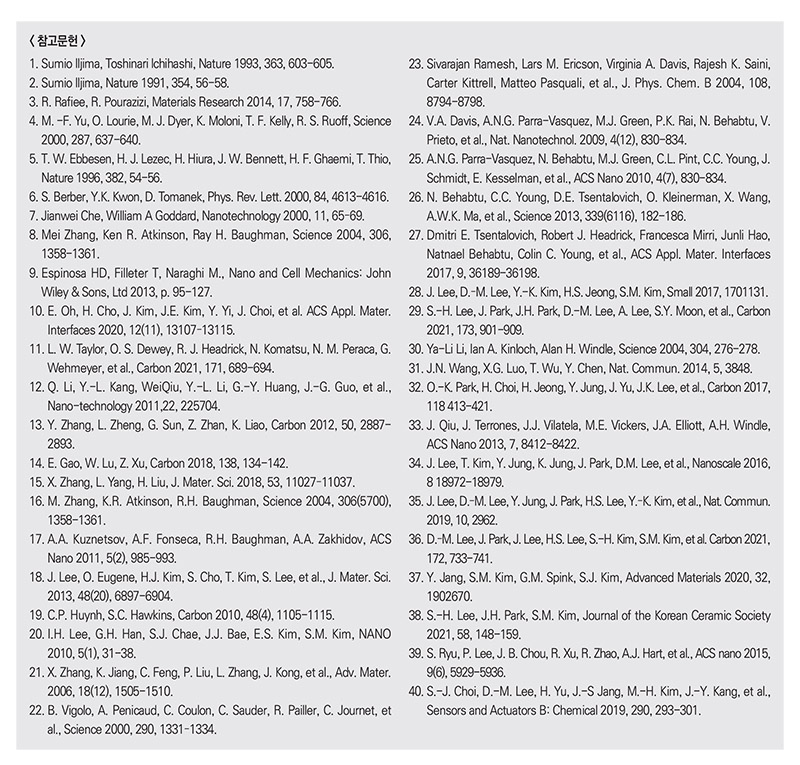
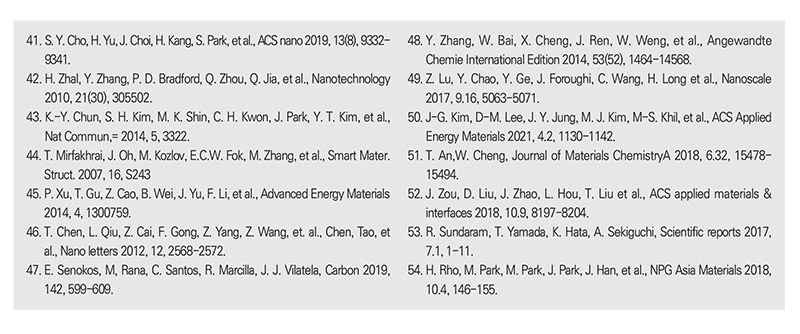
