기술과 솔루션
사출성형조건의 기본원칙과 체계적인 금형 시험 Injection Molding Basic & Systematic Mold Proving
작성자 : 취재부
2021-08-31 |
조회 : 4540
자료제공 : LS엠트론 김영기 고문
010-6603-8210 / ykkim2025@gmail.com
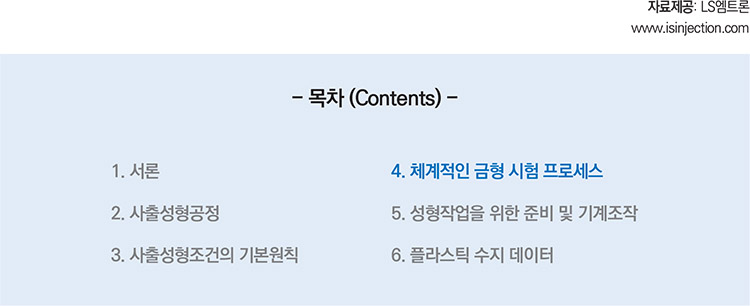
4. 체계적인 금형 시험
1) 정보
모든 금형 시험 공정의 초기 단계에서 금형과 플라스틱 재료 및 성형품에 대한 필요한 정보와 시험목적이 있어야 한다.
2) 절차
이 금형 시험은 위에 표기된 플로 차트에 맞게 수행되어야 한다.
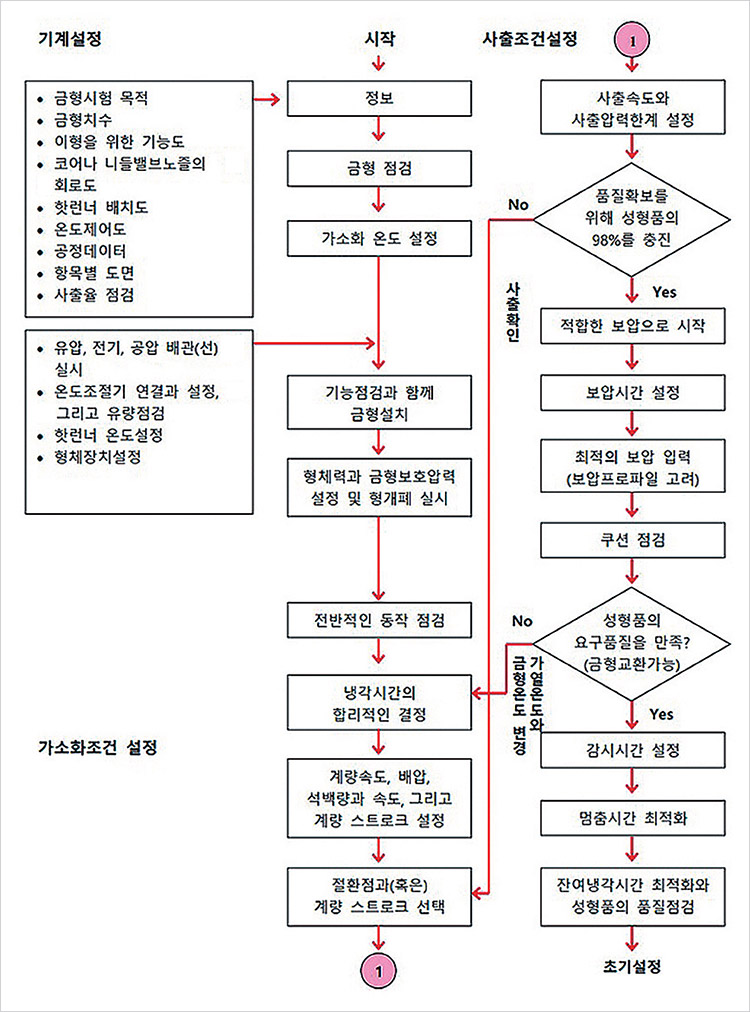
3) 부분 충진
각 시험과 불량원인의 분석을 위해서 부분 충진을 진행하는 것이 아주 중요하다. 여기에서 보압단계 중에 용융수지가 금형의 캐비티로 들어가지 않는 것을 확인하는 것이 중요하다.
설정한 보압절환점을 육안으로 점검되어야 한다. 보압절환 위치가 초과되는 것을 피하기 위해서 보압의 양을 아주 적은 값을 선택하는 것이 중요하다.
계량 중 용융 수지가 금형 캐비티 내로 들어가지 않게 확보하기 위해 충분히 긴 계량 지연 시간이 요구된다.
부분 충진 단계는 흐름 공정의 명확한 형상을 갖기 위해서 직경의 변화나 표면 결점이 있는 곳에 단계적으로 나누어서 수행되어야 한다.
부분 충진은 흐름 전단이 추적될 수 있도록 해당 절환점이나 계량량을 기록해야 한다. 상응한 이젝터 위치를 확보하기 위해서 부분 충진의 생산에서 충분한 사전 충진이 요구된다.
4) 사출 구간
일정한 표면 품질을 얻기 위해서 사출 초기 속도가 상대적으로 일정해야 한다. 사출 초기 속도는 사출 구간에서 사출 초기에 커버되는 거리이다.
일정하게 설정된 사출 속도에서 용융 수지가 일정한 양으로 사출된다. 그림 2.1과 같이 게이트에서 가깝고 먼 곳의 적은 수지 전단의 직경으로 수지 전단 속도는 중간에서 보다 이들 구역에서 높다.
좀 더 일정한 수지 전단 속도를 얻기 위해 저속-고속-저속의 사출 프로파일이 설정되어야 한다. 성형품의 상당한 흐름 전단 직경의 크기와 위치를 설정한 후에 스크류 전진 속도는 대략적으로 동등한 사출 전단 속도를 얻기 위해서 채택되어야 한다.
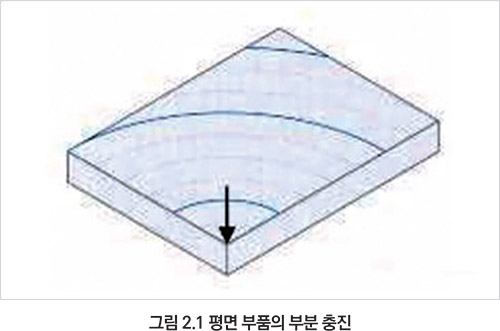
5) 보압절환점
보압절환점은 사출에서 보압단계로의 변환을 결정한다. 성형품의 과충진을 방지하고, 가능한 금형 손상을 방지하기 위해 성형품 전체용량의 대략 98%에 달할 때 보압절환이 되어야 한다.
계량되는 용융량이 변수 변화에 의해서 영향을 받을 때마다 보압절환점이 점검되어야 한다.
• 압력: 용융 수지의 압축
• 석백: 스크류 전단 구역의 수지량 변화
• 초기 사출 단계: 스크류 체크링의 닫힘 동작
6) 효과적인 보압시간
효과적인 보압시간은 점차 증가되는 보압시간에 따라 생산되는 성형품의 무게를 측정하여 결정할 수 있다.
보압의 양을 일정하게 유지해야 한다. 무게가 상당하게 증가하는 것이 멈추자마자 효과적인 보압시간에 도달한 것이다.
성형품에서 게이트 시스템으로 혹은 스크류 전단의 공간으로 불명확한 방법에 의해서 용융 수지가 뒤로 새지 않도록 하는 것이다. 이것은 성형품의 무게나 치수에서의 변화의 결과일 수 있다.
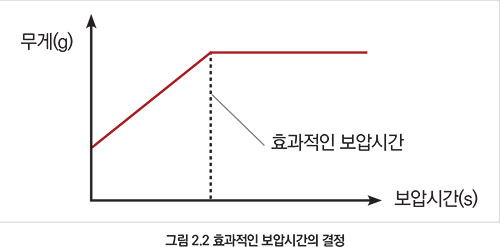
7) 냉각시간
경제적인 이유로 냉각시간은 가능한 한 짧아야 한다. 계산식에 의한 값이나 경험치는 해당 수지에 대한 고정된 값으로 사용될 수 있다. 결정적인 것은 제품두께, 금형 온도와 이형 온도이다.
냉각시간에서 금형 온도의 영향, 즉 생산 과정에서 추정컨대 금형 온도가 매우 높다는 것을 명심해야 한다. 온도 10℃의 변화는 냉각시간을 대략 20%까지 변화시킨다. 더군다나, 이형 온도나 금형 온도도 수축에 영향을 준다.
따라서 금형 치수 수정은 일정한 사이클에서 생산된 성형품을 갖고 이루어져야 한다.
8) 공정영역
사출성형품의 품질이 품질 관련 설정값의 확실한 범위 안에서만 보증될 수 있다. 이러한 범위를 가끔 공정영역이라고 부른다.
공정영역의 중간에서 기계 설정값만이 재료, 기계, 주변장치 등의 오차에 의해서 원인이 되는 불량률을 낮게 확보할 수 있다. 기계 설정에 대한 변화의 허용된 오차를 정의하는 것이 가능하다.
만약 생산 중에 품질 문제가 발생한다면 완벽한 기능을 위한 모든 구성 품목을 사전에 점검하는 것이 의무사항이다. 일반적으로 공정온도가 측정되어야 하고 수지 건조가 점검되고, 변수의 설정값과 실제값이 비교되어야 한다.
기계의 설정값이 체계적으로 최적화되었을 때만이 정확한 원인을 파악할 수 있다.
9) 변수변경 절차
만약 최적화가 아래의 조치대로 수행된다면 한 번에 변수 하나만 바꾸어야 하고 기록되어야 한다. 특히 용융온도와 금형 온도에 변화가 있다면 열 균형이 도달했을 때 성형품을 평가해야만 한다.
10) 상관관계
여러 변수의 상관관계와 그들이 성형품 품질에 끼치는 영향이 평가될 수 없다면, 체계적인 금형 시험이 수행되어야 한다. 이러한 목적으로 사출률, 보압 등 각각의 품질 관련 변수가 체계적으로 변경되도록 시험계획에 포함되어야 한다. 금형 시험 횟수는 2n이다.
< 예 > 변경될 변수
사출 시간 te
보압 tn
금형 온도 Tw
금형 시험 횟수 = 2n = 23 = 8
te+ 사출 높임
te- 사출 낮춤
tn+ 보압 높임
tn- 보압 낮춤
Tw+ 금형 온도 높임
Tw- 금형 온도 낮춤
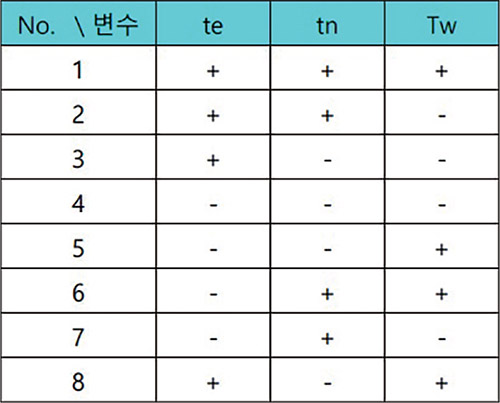
시험에 필요한 시간은 가능하면 적게 들어야 한다.
따라서 시험은 설정온도의 변화에 따라서 실시되어야 한다.
상기 도표와 같은 경우에는 2, 3, 4, 7, 1, 5, 6, 8번 순으로 시험을 진행되어야 한다.
… 10월호에 ‘5. 성형작업을 위한 준비 및 기계조작’가 이어집니다
