기술과 솔루션
사출 금형 파팅(Parting)과 게이트(Gate)에 대하여
작성자 : 편집부
2021-11-11 |
조회 : 10889
자료제공: 우진플라임 기술교육원 / 교수 한선근
1. 파팅(Parting)과 파팅 라인(Parting Line)
< 파팅(Parting) >
파팅 라인(Parting Line)이란 금형의 고정 형판과 가동 형판의 맞춤 면으로서, 또한 파팅면(분활면)이라고도 하는데, 이 파팅면의 위치가 금형 설계나 제작은 물론, 성형 제품의 취출에도 영향을 주게 되므로 매우 신중하게 결정되어야 한다.
< 파팅 라인을 결정할 때는 다음 사항에 대하여 주의하여야 한다. >
① 성형품의 외관 기능을 손상 시키지 않는 위치에 결정한다.
② 성형품의 정밀도가 잘 나올 수 있는 곳에 선정한다.
③ 성형재료가 흐르기 쉬운 위치에 게이트를 붙일 수 있게 한다.
④ 금형가공이 용이한 곳에 선정한다.
⑤ 이형이 용이한 위치에 선정한다.
⑥ 금형이 열릴 때 언더컷이 되지 않는 곳에 선정한다.
< 파팅 라인의 결정 >
(a)와 같은 곳에 게이트를 붙이는 것도 허용되지만 눈에 띄기 쉽다. 하지만 (b)와 같은 곳에 설치하면 제품의 외관이기는 하나 눈에 잘 띄지 않고, 게이트 절단 후 상대물과의 조립 시 보이지 않을 수 있다.
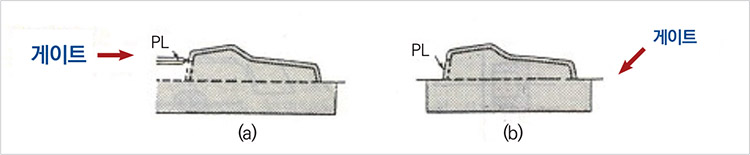
[ 생각해보기 ] 파팅 라인 어느 곳이 가장 적합할까?
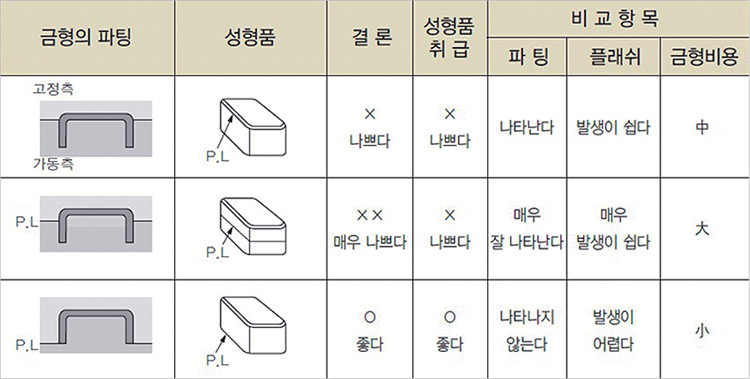
2. 게이트의 종류
Sprue, Runner, Gate System
1) 게이트의 분류
- 비제한 게이트 : 다이렉트 게이트(Sprue Gate)
- 제한 게이트:사이드 게이트 (Side Gate), 필름 게이트 (Film Gate), 탭 게이트(Tap Gate)
오버랩 게이트(Overlap Gate), 핀포인트 게이트(Pin Point Gate)
서브마린 게이트(Submarine Gate), 커브드 게이트(Curved Gate, 코끼리 게이트)
① 다이렉트 게이트(스프루 게이트)
▶ 스프루의 싱글 캐비티 금형으로 성형이 쉽다.
▶ 성형기 사출 압력이 직접 캐비티에 전해져 압력 손실이 적다.
▶ 성형성이 좋고 모든 사출성형 재료에 적용할 수 있다.
▶ 스프루의 고화 시간이 길기 때문에 사이클 타임이 길어진다.
▶ 잔류응력 또는 크랙이 일어나기 쉬우므로 게이트 주변에 링 모양의 리브를 보강하는 것이 좋다.
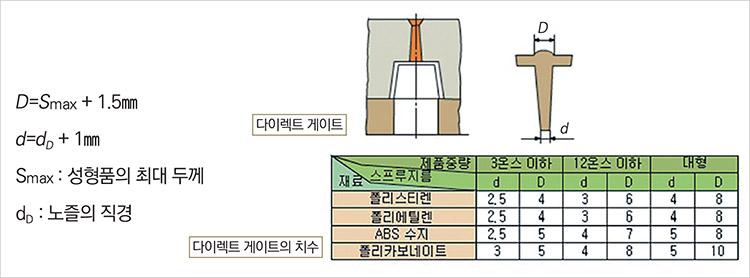
② 표준 게이트(사이드 게이트)
▶ 단면 형상이 간단하므로 가공이 용이하다.
▶ 게이트 치수를 정밀하게 가공할 수 있고, 치수의 수정이 쉽다.
▶ 캐비티의 충전 속도는 게이트 고화와 관계없이 조절할 수 있다.
▶ 거의 모든 수지에 적용할 수 있다.
▶ 성형품의 외관에 게이트 흔적이 남는다.
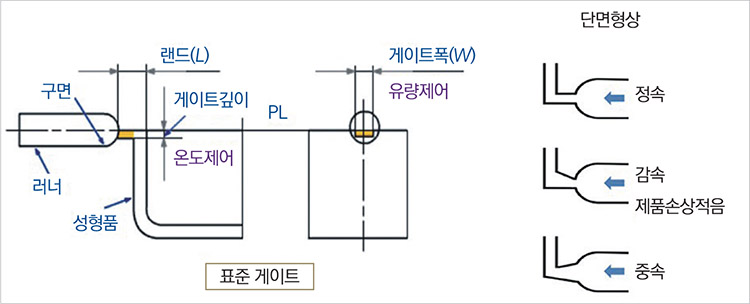
③ 팬 게이트(Fan Gate)
< 단면 형상이 부채꼴로 된 게이트 >
▶ 넓고 얇은 평판 형상의 제품을 균일하게 충전하여 기포나 플로우 마크(Flow Mark)를 없게 하는 데 적합
▶ 게이트 부근의 결함을 최소로 하는 데 가장 효과가 있고, PVC 이외의 범용 수지에 사용된다.
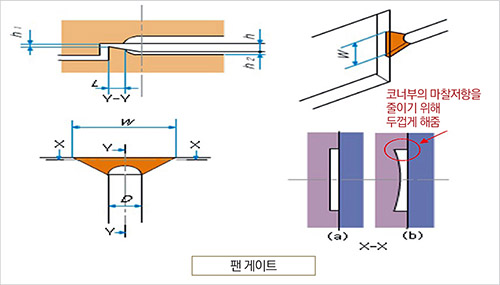
④ 필름 게이트(Film Gate)
▶ 성형품에 형평으로 런너를 설치하고 성형품과의 사이에 두께를 얇게 한 게이트를 설치
▶ 평판 상 성형품의 수축변형을 최소한으로 억제하려고 할 때 사용
▶ 점도가 높은 경질 PVC뿐만 아니라 범용 수지에도 사용된다.
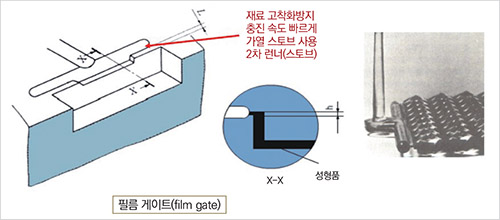
⑤ 오버랩 게이트(Overlap Gate)
▶ 성형품에 수지 흐름 자국(Flow mark)이 생기는 것을 방지하기 위하여 성형품의 측면이 아니고 성형품의 끝 면에 겹쳐지도록 코어 쪽에 설치한 게이트
▶ 성형품의 측면에 게이트 자국이 남게 되므로 제거 및 다듬질하는데 주의하여야 한다.
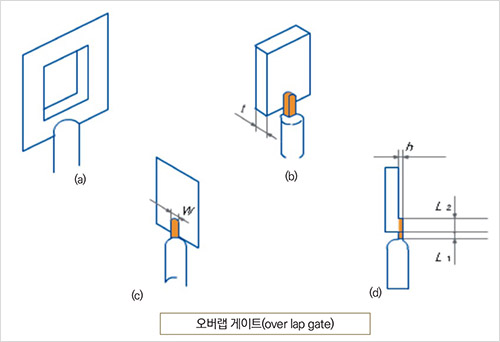
⑥ 탭 게이트(Tab gate)
▶ 오버랩 게이트의 변형
▶ 잔류응력이나 변형이 없는 성형품을 얻을 수 있다.
▶ 사출 압력에 의한 과충전이나 게이트 부근의 싱크 마크 방지
▶ 열 안정성과 유동성이 좋지 않은 수지 성형에 적합(PVC, PC)
▶ 성형품의 폭이 넓을 경우 멀티탭 게이트를 사용
▶ PMMA, SAN 등 대부분의 수지에 적용된다.
▶ 런너에 대하여 직각으로 붙이는 것이 보통이다.
▶ 얇은 부분에 설치하면 흐름 자국(Flow mark)이나 웰드라인(Weld Line)을 일으키기 쉬우므로 두꺼운 부분에 설치한다.
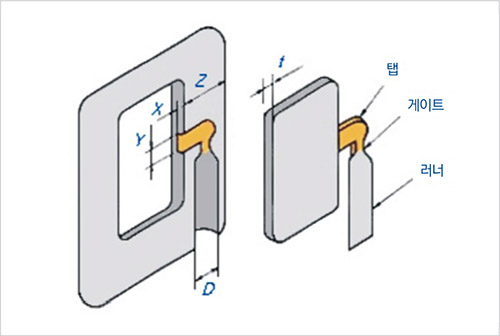
⑦ 디스크 게이트(Disk gate)
▶ 다이아프램 게이트(Diaphragm gate)
▶ 성형품의 중앙부에 스프루를 지름보다 크게 뚫린 구멍이 있을 경우, 여기에 게이트를 배치하거나 원통 모양의 성형품에 웰드 마크를 방지하기 위하여 사용되는 원판상의 게이트
▶ 게이트 제거와 마무리 작업을 필요로 함, 수지는 경질 PVC 이외의 모든 수지에 적용
▶ 2매 용 금형의 1개 치로 원통형에 일반적으로 사용
▶ 3매 용 금형 및 런너 리스 금형의 다수 개 빼기에도 사용된다.
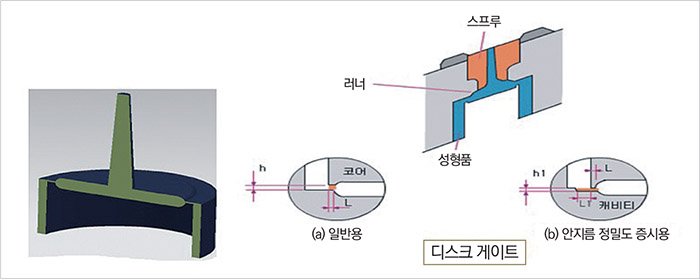
⑧ 링 게이트(Ring gate)
▶ 소형 물이며, 캐비티가 많은 금형으로, 파이프 형상의 가늘고 긴 성형품 제작에 사용
▶ 볼펜 뚜껑 등의 원통형 성형품을 성형하기 위해 사용
▶ 웰드라인 방지, 사출 압력에 의한 금형의 코어 핀의 쓰러짐으로 인한 편심 방지
▶ 두께가 균일한 성형품의 생산이 가능
▶ 주입구의 반대쪽에 콜드 슬러그 웰을 원통형의 외주에 설치한다.
▶ 일반적으로 스트리퍼 밀판 또는 슬리브 밀판에 의해 내어지므로 사다리꼴 런너를 많이 채택한다.
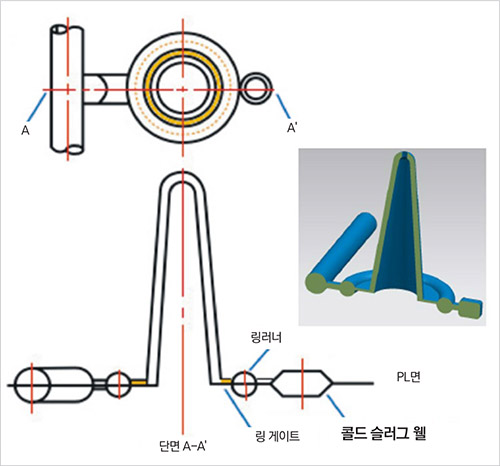
⑨ 핀 포인트 게이트(Pin Point gate)
▶ 게이트의 위치 결정이 비교적 제한받지 않고 자유롭게 결정할 수 있다.
▶ 게이트 부근의 잔류응력이 적다.
▶ 투영면적이 큰 성형품, 변형되기 쉬운 성형품의 경우 다점 게이트로 수축, 변형을 적게 할 수 있다.
▶ 게이트의 후가공이 용이하다. 게이트는 자동적으로 절단된다. 다 캐비티의 경우 게이트 밸런스가 쉽다.
▶ 금형 구조는 3매 용 구조로 된다. 그러나 런너 리스 금형일 경우 2 플레이튼 구조로도 된다.
▶ 3단 금형의 경우 성형 사이클 시간이 길게 된다.
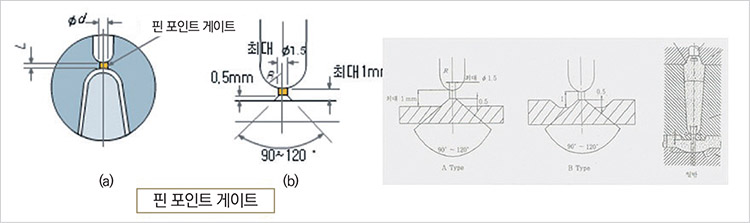
⑩ 서브마린 게이트(Submarine gate)
▶ 형판 앞에 터널식으로 파고 들어가 터널 게이트라고도 함
▶ 게이트는 성형품이 돌출함과 동시에 자동 절단
▶ 게이트 자국이 측면에 남아서 안 될 경우 2차 런너 사용
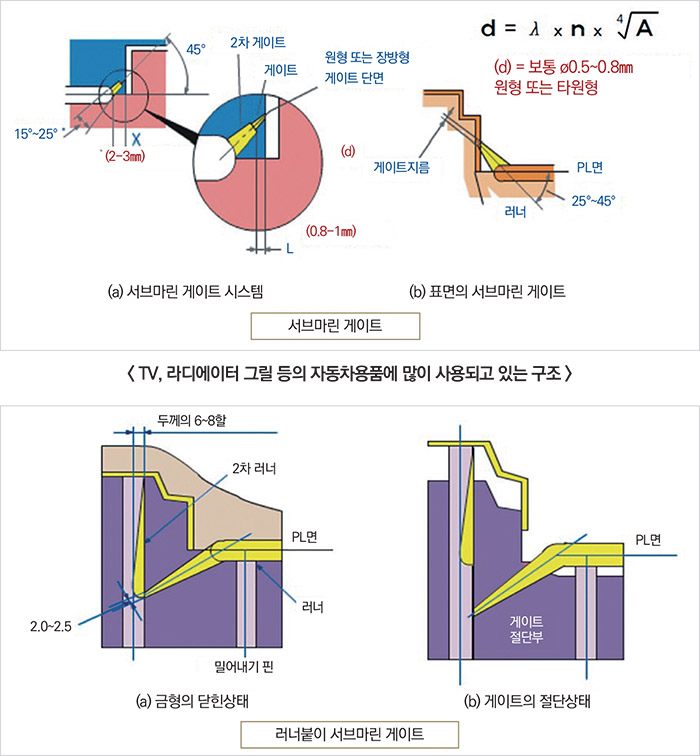
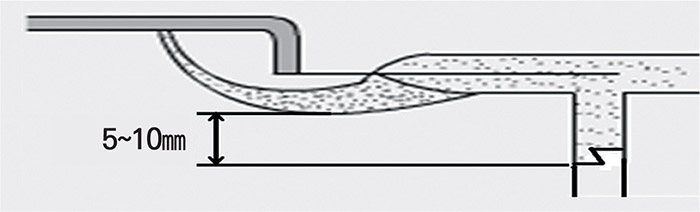
▶ PC 원재료를 사용하는 제품에서 젯팅 현상 방지
▶ 게이트 흔적을 남기지 않기 위해 사용
▶ 게이트 자동 제거가 필요한 얇은 제품에 적용된다.
▶ 런너 이형 시 게이트부가 잘 이형되지 않아 부러질 수 있음
▶ 콜드 슬러그 부위가 게이트의 만곡점보다 5~10㎜ 길게 제작(제품 손상 방지)
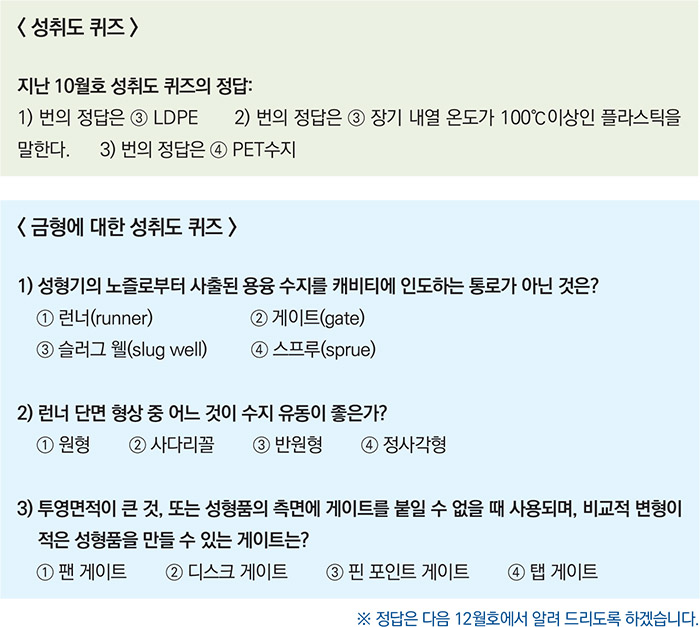
