기술과 솔루션
전기자동차용 리튬이온 전지 시스템과 안정성 확보 기술 동향
작성자 : 편집
2022-06-12 |
조회 : 5300
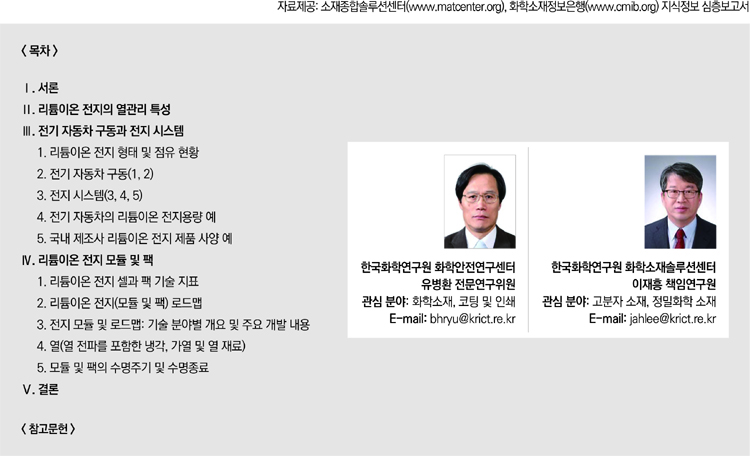
Ⅰ. 서론
2021년 말 대한민국의 전기차와 수소차 등 친환경 차량 등록 대수가 100만 대를 돌파한 가운데 대중교통 수단인 버스도 빠른 속도로 전기차로 진화하고 있다. 2025년까지 전기자동차는 113만 대(승용, 버스, 화물 등 누적)를 보급하고, 충전 기반시설(인프라)은 4.5 만기(급속충전기 1.5만기, 완속 충전기 3만기, 누적)를 확충할 예정이다. 다음 그림 1은 서울, 부산, 대전 전기버스의 운행 예를 뉴스 기사로부터 인용한 것이다.
• “서울·부산은 전기버스 도시”이다.
2021년 서울을 달리는 전기버스는 총 392대이고, 부산시는 연말까지 전기버스 운행 대수를 263대로 늘릴 예정이다. 전기버스는 주행 시 질소산화물(NOx) 등 오염물질과 이산화탄소 등 온실가스가 발생하지 않는다. 기존 압축천연가스(CNG) 버스가 연간 1대당 이산화탄소 약 80.9t, 질소산화물 66㎏을 배출하는 점을 고려하면, 한 단계 업그레이드된 ‘그린 모빌리티’ 수단이다. 1대당 연간 약 1,260만 원의 연료비를 절감하는 효과도 있다고 한다.
• 서울~인천을 오가는 2층 전기버스
2021년 4월부터 2층 전기버스를 인천시 연수구와 서울 삼성역을 연결하는 광역버스 노선을 운행 중이다. 최대 70명이 탈 수 있는 2층 전지버스는 384kWh의 대용량 배터리를 적용해 환경부 인증 기준으로 1회 충전 시 최대 447km를 운행할 수 있다.
• ‘무선 충전 버스 대전 시내 누벼’
2021년 10월부터 대전에서는 무선 충전 방식의 전기버스(올레브)가 운행을 시작했다. 올레브는 온라인 전기자동차(On-Line Electronic Vehicle)의 약칭이다. 올레브는 1시간에 150㎾를 충전해 150㎞를 주행할 수 있다. 대덕 특구 순환노선에서는 버스 기사가 쉬는 시간인 20분 동안 50㎾를 충전해 23.5㎞를 달린다고 한다. 마을버스 성격인 올레브는 KAIST~대덕 특구 출연연~도시철도역 등을 순환 운행한다.
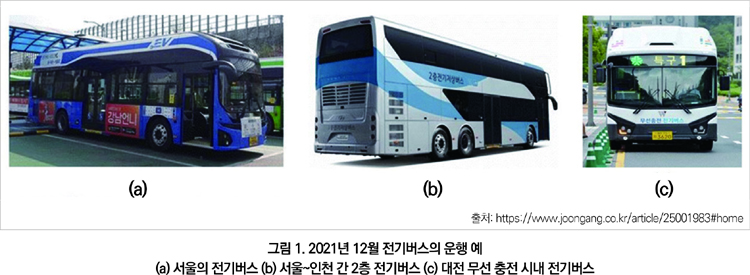
전기자동차가 승용차 상용화를 시작으로 전기버스도 본격적인 상용화 시대가 도래한 것으로 보인다. 이에 따라 리튬이온 전지 시장도 본격적으로 상승세를 맞이할 것으로 보인다.
본 리튬이온 전지의 심층 보고서에서는 리튬이온 전지 및 관련 소재산업의 전반적 현황 및 미래기술 동향으로부터 리튬이온 전지 관련 종사자의 시장 선점 노력을 소개하고자 한다.
리튬이온 전지의 시장과 소재(1편~2편), 리튬이온 전지의 제조와 성능향상(3편~4편)으로 나누어 전체 4편의 리뷰로 리튬이온 전지의 시장동향과 요구사양, 셀 제조기술과 성능향상, 소재 로드맵, 전지의 에너지형과 파워형 설계 디자인(핸들러 2022년 2월호 테크&솔루션 p129~142 참조), 그리고 전지 시스템의 안정화를 위한 전지팩 기술 로드맵에 관한 전반적 내용을 소개하고자 한다.
4편은 전기자동차용 리튬이온 전지 시스템과 안정성 확보를 위한 전지팩 로드맵을 주제로 전기 자동차용 전지 시스템과 구동 연계, 리튬이온 전지 모듈 및 팩의 주요 개발내용을 조사하였다. 자세하게는 전기 자동차용 전지 시스템과 구동 연계, EV용 전지팩의 적용 사례와 실제 리튬이온 전지 성능 스펙을 예시하여 현재 전지 성능과 특성을 알아보았다.
또한, 전지의 지속 가능한 성능 발전을 위하여 전지 모듈과 팩 제조를 위한 기술 로드맵을 중심으로 리튬이온 전지 시장의 지속 성장과 전지 시스템의 안정화 관점에서 조사하였다.
Ⅱ. 리튬이온 전지의 열관리 특성
표 1에 18650 원통 셀을 이용한 리튬이온 전지의 열관리 특성을 나타내었다. 리튬이온 전지는 (1) 저온에서 전극 활물질 활성도와 리튬이온 확산계수가 낮아짐으로써 전지 성능이 급격하게 저하하며, 극한 상황에서는 전해질의 동결로 인하여 가동이 불가능해질 수 있다.
또한, 리튬의 석출(플레이팅, plating)로 인해 충전용량이 상당히 저하될 수 있고, 덴드라이트(dendrite) 성장으로 분리막이 관통되면 내부 회로의 단락(short circuit)이 발생하여 큰 발열로 전이될 수 있다. 실제 저온에서 영향 평가한 실험에서는 외부온도가 상온에서 -20℃로 변화할 때, 동일한 방전 조건에서 에너지가 27% 정도 감소함을 보였다.
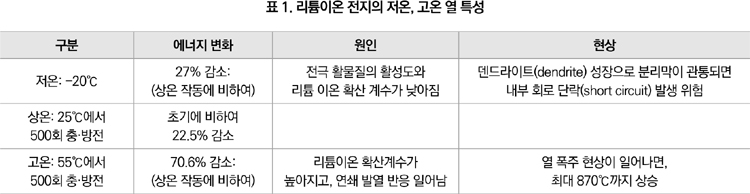
리튬이온 전지가 (2) 고온에 노출될 때 저온에서와 유사하게 용량 감소(capacity fade)와 전력 손실이 발생한다. Sony 18650 셀을 이용하여 상온에서부터 55℃까지 온도를 변화하며 충·방전 사이클에 따른 용량 변화를 분석한 실험에서는 500회 충·방전 시 상온에서 22.5%, 55℃에서는 70.56% 용량 감소를 보고하였다.
최근 다른 보고에 의하면, 전기 자동차용 리튬이온 전지는 영하의 온도에서 성능이 급격히 떨어진다. 전지의 최적 성능을 유지할 수 있는 25℃를 기준으로 전지 온도가 -20℃와 45℃일 때, 전기 자동차의 주행거리는 각각 33%와 1.8% 감소하였다.
고온 환경에서 전지 사용 시 연쇄 발열 반응으로 인해 발생하는 열 폭주(thermal runaway) 현상은 발화 및 폭발과 같은 심각한 사고를 유발할 수 있다. 각형 리튬이온 전지를 이용한 열 폭주 거동 실험에서는 최대 온도가 870℃에 도달하는 것으로 보고되었다.
리튬이온 전지 사용 가능 온도는 0~60℃이지만, 최적의 성능을 위해서는 15~40℃ 사이에서의 가동이 권장된다. 따라서 온도에 따른 성능 감소와 심각한 사고를 예방하기 위해서는 리튬이온 전지가 적절한 온도 범위 내에서 반드시 가동 및 보관되어야 하고, 이를 위해 리튬이온 전지팩 시스템의 적절한 열관리 시스템이 추가되어야 한다.
Ⅲ. 전기 자동차 구동과 전지 시스템
1. 리튬이온 전지 형태 및 점유 현황
리튬이온 전지의 가장 작은 단위는 셀이다. 전기를 충·방전하며 에너지를 효율적으로 관리할 수 있는 리튬 이차 전지는 형상별로 원통형, 각형, 파우치형의 각 용기에 양극과 음극, 전해액과 분리막이 겹겹이 쌓여있는 구조로 그림 2와 같이 되어있다.
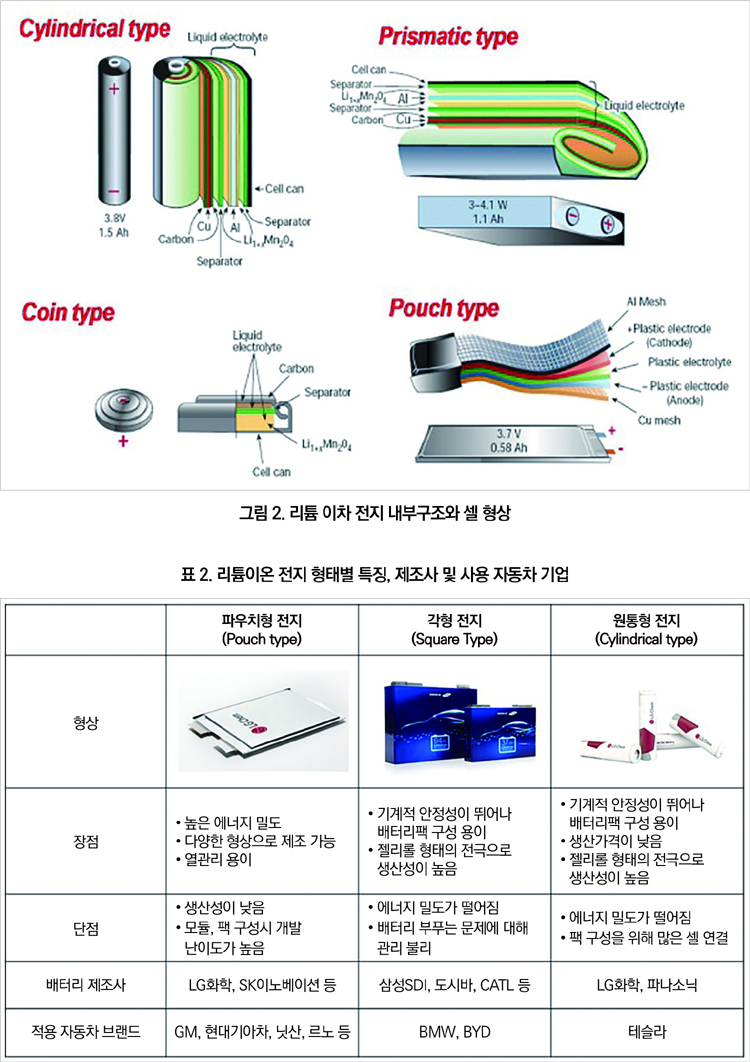
셀의 형태에 따른 장단점, 그리고 전지 제조(사)와 전기 자동차 브랜드는 표 2와 같다. 파우치형은 생산성이 다소 낮지만 에너지 밀도가 높고 열관리가 쉬운 장점을 가지고 있으며, LG화학, SK이노베이션이 생산하고 GM, 현대기아차, 닛산, 르노 등이 사용하고 있다.
전체 리튬이온 전지에서 파우치형 전지의 점유율은 2012년에 23.6%에서 2020년에 51.8%를 차지하여 증가 추세이다. 원통형은 LG화학, 파나소닉이 생산하며 자동차에서는 테슬라만이 채용하고 있다. 에너지 밀도가 떨어지는 단점 때문에 2012년에 약 40%에서 2020년에 약 20%로 감소하였다.
2. 전기 자동차 구동
전기 자동차에는 기존 자동차의 가장 중요한 부품인 엔진과 변속기가 없다. 대신, 전기 자동차 구동은 구동 모터와 감속기에 의해 동력을 발생시킨다. 전기는 전지 시스템에 의해 제공되고 전지 온 보드 차저, 통합전력제어 장치로 구성된다. 이들은 모두 전지의 전력으로 모터를 구동한다. (그림 3 참고)
• 구동 모터
구동 모터는 전기 에너지를 운동 에너지로 전환하여 바퀴를 굴린다. 모터를 구동 장치로 사용하며 얻는 장점은 다양하다. 일단, 주행 중에 발생하는 소음과 진동이 매우 적다. 전기 자동차의 파워트레인은 연소 엔진보다 크기가 작아 공간 활용성을 높이는 데 매우 유리하다.
구동 모터는 발전기로도 활약한다. 내리막길 등 탄력 주행 시 발생하는 운동 에너지를 전기 에너지로 전환해 전지에 저장할 수 있다. 주행 중 속도를 줄일 때도 마찬가지로 감속하는 운동 에너지를 이용하여 전기 에너지를 만들어 낸다. 이는 회생제동 시스템이라고 한다. 현재 일부 전기 자동차에는 회생제동을 단계별로 조절할 수 있는 장치가 마련되어 있다.
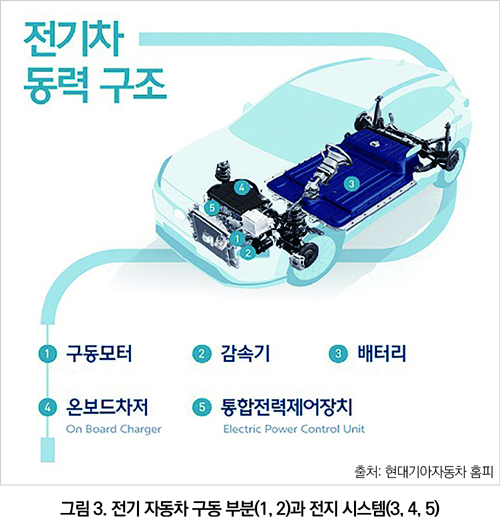
• 감속기
감속기는 모터의 특성에 맞춰 동력을 바퀴에 더 효율적으로 전달하기 위해 고안된 일종의 변속기이다. 모터는 분당 회전수(RPM)가 내연기관 엔진보다 훨씬 높다. 회전수를 상황에 맞게 바꾸는 변속이 아닌, 회전수를 하향 감속해야 한다. 감속기는 모터의 회전수를 필요한 수준으로 낮춰 전기 자동차가 더 높은 회전력(토크)을 얻을 수 있도록 한다. (내연기관의 변속기 역할)
3. 리튬이온 전지 시스템
전기 자동차용 전지 시스템은 (1) 에너지원인 전지 셀, (2) 전지 셀을 외부의 충격과 진동으로부터 보호하는 기계적 구조물, (3) 전지 셀의 작동 시에 발행하는 열을 배출하고 외부의 영향을 차단하여 전지 셀을 열적 위험으로부터 보호하는 열관리 시스템, (4) 전지의 충전과 방전을 제어하고 전지를 보호하는 전지 관리 시스템(battery management system, BMS) 등으로 이루어진다.
• 전지(팩)
전지는 전기 에너지를 저장하는 부품으로, 내연기관차의 연료탱크와 연료에 해당한다. 전기 자동차의 주행거리는 보통 전지용량이 클수록 주행거리도 늘어난다.
그러나 전지용량을 키우는 일은 그리 간단하지 않다. 전지가 차지하는 부피와 무게 때문이다. 큰 전지를 얹으면 실내 공간 및 짐 공간이 줄어들고, 에너지 효율이 떨어진다. 따라서 전기 자동차의 주행거리를 효율적으로 늘리기 위해서는 전지 에너지 밀도를 높여야 한다. 크기가 작고 가벼우면서 전기 에너지를 최대한 효율적으로 저장해야 한다. 주행가능 거리가 길수록 충전 횟수가 줄어들어서 전기 자동차 생활은 한층 더 편리해진다.
최근 출시된 전기 자동차는 전지 기술 발전에 따라 에너지 밀도가 크게 높아졌다. 덕분에 1회 충전 주행거리도 초기 전기 자동차보다 크게 늘었다. 기아자동차 쏘울 부스터 EV의 경우 64kWh 용량의 리튬이온 전지를 탑재해 최대 386km를 달릴 수 있다(국내 인증 기준).
전지 수명도 크게 개선되었다. 전기 자동차의 리튬이온 전지는 충전 패턴에 따라 수명이 달라지는데, 일상적인 사용 조건이라면 폐차할 때까지 전지 내구성에 대한 걱정은 필요 없다.
통상적으로 전지 전력을 100% 방전될 때까지 주행하고 다시 충전하는 경우라면 1,000회, 전지 전력 50%를 사용하고 다시 충전하는 경우라면 5,000회, 전력 20%를 사용하고 다시 충전하는 경우라면 8,000회까지 전지 사용이 가능하다. 따라서 쏘울 부스터 전기 자동차를 하루에 약 77km(전력 20% 사용 시)를 운행한다고 가정하면 8,000일(약 22년) 동안 전지 교체 걱정 없이 차량을 사용할 수 있다는 계산이다.
• 전지 관리 시스템(Battery Management System, BMS)
전지 관리 시스템(이하 BMS)은 이런 수많은 전지(셀)를 하나의 전지처럼 사용할 수 있도록 관리한다. 전기 자동차 전지는 수십에서 수천 개에 이르는 셀로 이뤄져 있는데, 각 셀 상태가 비슷해야 전지 내구성과 성능이 최적 컨디션을 유지할 수 있다.
BMS는 전지와 일체형으로 설계되는 경우가 많으며, 통합 전력 제어장치(EPCU)에 포함되기도 한다. 셀 충전 및 방전 상태를 감시하고, 전지에 이상이 감지될 경우 릴레이(특정 조건에서 다른 회로를 개폐하는 장치)를 통해 자동으로 전지 전원을 잇거나 끊기도 한다.
• 전지 히팅 시스템
전지는 낮은 온도에서 충전량이 감소하며 충전 속도가 느려진다. 전지 히팅 시스템은 전지를 최적 온도로 유지시켜 동절기 성능 저하를 예방하고 주행거리를 확보하는 장치이다. 또한 충전 시에도 적정 온도를 유지해 충전 효율성을 높인다.
• 온 보드 차저(On Board Charger, OBC)
전지에 충전을 하는 장치이다. 온 보드 차저는 완속 충전을 하거나, 휴대용 충전기로 가정용 플러그에 꽂아서 충전할 경우, 차량에 입력된 교류 전원(AC)을 직류 전원(DC)으로 변환하는 장치이다. 참고로 급속 충전은 직류를 이용한다.
• 통합 전력 제어장치(Electric Power Control Unit, EPCU)
통합 전력 제어장치는 차량 내 전력을 제어하는 장치를 통합하여 효율성을 높여주는 역할을 하며 인버터, LDC, VCU로 구성되어 있고 각각의 역할은 다음과 같다.
- 인버터(Inverter): 인버터는 전지의 직류 전원(DC)을 교류 전원(AC)으로 변환하여 모터의 속도를 제어하는 장치이다. 내연기관 변속기와 같은 역할로 가속과 감속 명령을 담당하므로 전기 자동차의 운전성을 높이는 데 있어서 매우 중요한 역할을 한다.
- LDC(Low voltage DC-DC Converter): LDC는 전기 자동차의 고전압 전지 전압을 저전압(12V)으로 변환해 전장 시스템에 전력을 공급하는 장치이다. 고전압 전지는 높은 전압을 사용하지만, 자동차의 전장 시스템은 낮은 전압을 사용하기 때문에 이를 변환하는 장치가 반드시 필요하다.
- VCU(Vehicle Control Unit): VCU는 EPCU에서 가장 중요한 부품 중 하나이다. 차량 내 전력 제어기를 총괄하는 컨트롤 타워에 해당한다. 모터 제어, 회생제동 제어, 공조 부하 제어, 전장 부하 전원공급 제어 등 차량의 전력 제어와 관련된 대부분을 관장하고 제어한다.
4. 전기 자동차의 리튬이온 전지용량 예
최근 주목받고 있는 전기 자동차의 전지용량, 모터 출력, 주행거리를 그림 4에 정리하였다. 쉐보레 볼트는 전지용량은 60kWh이고, 주행거리는 383km이다. BMW i3의 전지용량은 33.2kWh이고, 주행거리는 300km이다.
국내에서는 현대차 아이오닉, 기아차 SOUL 등이 양산되고 있고, 하이브리드를 고수하던 일본도 전기 자동차 개발에 박차를 가하고 있다. 고성능 전기 자동차로 주목받고 있는 테슬라 모델-S 제원은 다른 제조사에 비해 가격보다는 성능에 초점을 맞춘 것을 알 수 있다.
현대기아차와 테슬라는 아이오닉5와 모델Y 등 73~75 ㎾h 용량의 전지를 장착해 한번 충전으로 450~511㎞ 이상 주행이 가능한 전기 자동차를 2021년 초에 선보였다. (핸들러 2022년 2월호 테크&솔루션 p130 표 1 참조)
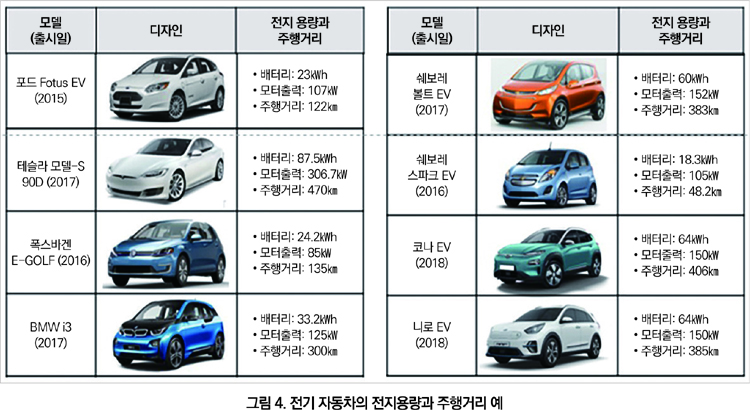
5. 국내 제조사 리튬이온 전지 제품 사양 예
소형, 중형, 대형 용량(26~200Ah)의 리튬이온 전지 제품 사양을 표 3~표 6에 나타내었다. 제품 사양으로 공칭전압, 에너지 밀도(비용량), 내부저항, 규격, 중량 등을 확인할 수 있다. 제품 사양을 통하여 충·방전 시간, 온도 환경을 확인할 수 있으며, 셀 크기, 사이클 수명 등도 확인할 수 있다.
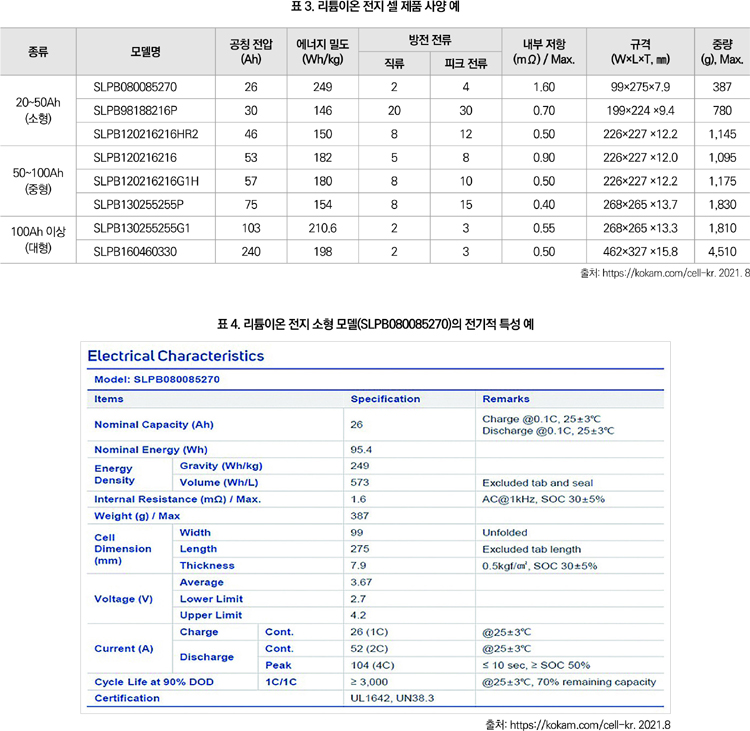

Ⅳ. 리튬이온 전지 모듈 및 팩
영국자동차협회는 2021년 1월 리튬이온 전지 보고서를 발간하였다. 리튬이온 전지 소재개발과 전지팩 제조 관련하여 기술적 지표와 함께 중장기적으로 달성할 기술 로드맵(2020년~2035년)을 발표하였다. 주로 전지의 셀, 모듈과 팩 제조기술 지표와 로드맵을 소개하였다.
1. 리튬이온 전지 셀과 팩 기술지표 (에너지 중심 및 원가 민감형)
셀은 전지의 가장 작은 단위이고, 모듈(Module)은 셀을 외부 충격, 진동, 열 등으로부터 보호하기 위해 하우징에 넣은 전지 집합체이다. 팩(Pack)은 전기자동차에 장착되는 전지 시스템의 최종 형태이고, 제어기, 냉각시스템 등 각종 제어 및 보호 시스템을 전지 모듈과 통합하여 완성된다.
블룸버그 통계에 따르면, 그림 5와 같이 2013년부터 2020년까지 리튬이온 전지(셀) 가격은 668$/kWh에서 137$/kWh로 급격하게 감소하였으나, 자동차용 전지로 사용하기에는 여전히 고가이다.
한편 영국자동차협회가 발표한 성능지표 및 원가를 살펴보면, 시장의 경쟁 환경에서 전지 산업이 달성할 기술지표는 표 7과 같다. 리튬이온 전지 팩의 비용량을 보면 2020년, 185Wh/kg에서 2035년에 275Wh/kg으로 비약적으로 증가할 것으로 예상하고 있다. 충전 시간을 보면 2020년 약 45분에서 2035년 15분으로 단축되고 있다.
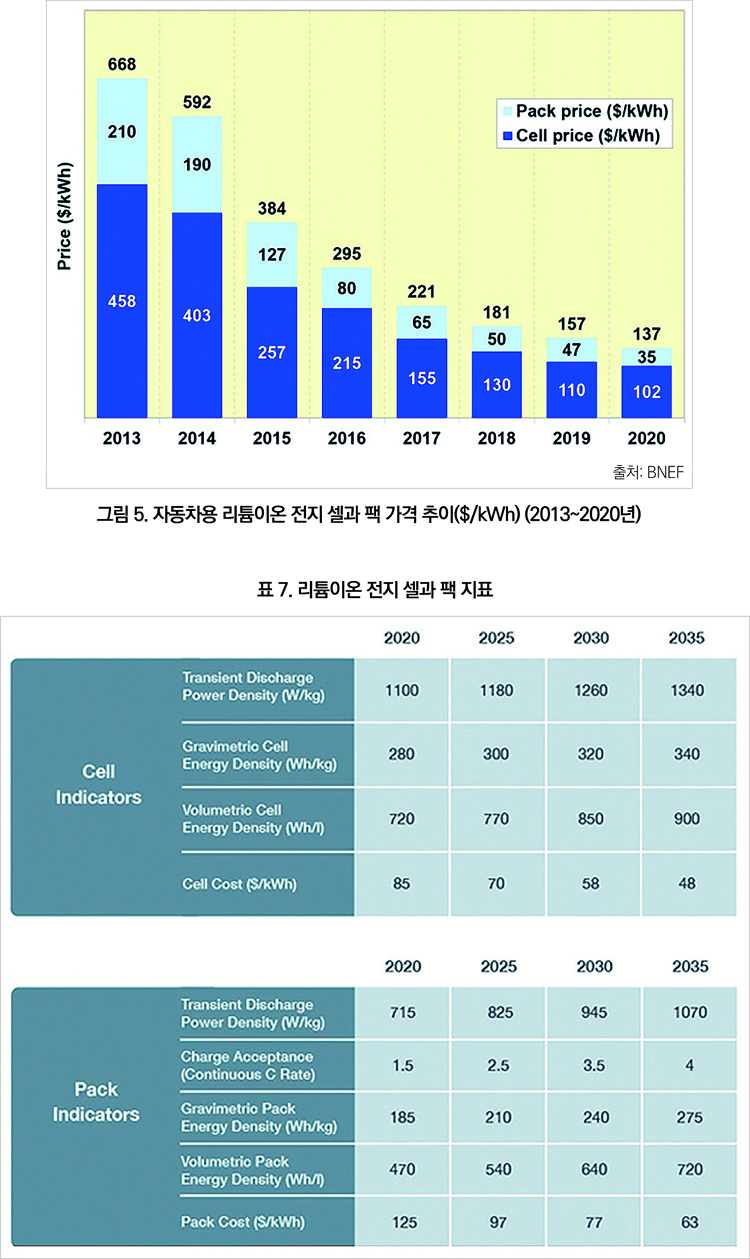
영국자동차협회는 2020년 팩의 OEM 가격은 셀 가격 85$/kWh에 패킹가격 40$/kWh을 더하여 125$/kWh로 제시하였다. 블룸버그 통계치는 셀 가격 102$/kWh에 패킹 단가 35$/kWh을 더하여 137$/kWh로 12$/kWh 정도 단가가 더 높다.
패킹 단가는 비슷하지만 셀 가격이 17$/kWh 더 높게 나타나, 셀 단가는 더 낮아질 수 있는 여지를 보인다. 또한, 팩 단가를 2020년 125$/kWh에서 2035년에는 65$/kWh로 낮추는 지표를 제시하고 있다.
이는 리튬이온 전지용 셀 소재 및 제조공정의 단가를 혁신적으로 더 낮추어야 한다는 결론이다. 대안으로는 혁신적으로 비용량이 높은 양극재를 개발하고, 소재와 공정에 대한 글로벌 표준을 제안하고 규모의 경제와 함께 소재와 셀의 재활용 등을 준비할 때이다.
표 7에서 과도방전전력밀도(Transient Discharge Power Density(W/kg))는 셀이 끌어낼 수 있는 최대 전력을 나타낸다. 전이방전은 <10초 25℃ 및 50% SoC로 정의된다. 충전율(C-rate)은 전지 팩 충전과 방전 속도의 척도이다. 2035년의 4C rating은 전지팩이 15분 안에 완전히 충전되는 것을 기대한다. 에너지 밀도는 셀과 팩 모두 적용되며 체적 및 중량으로 측정된다.
원가는 셀 및 팩의 OEM 구입 가격을 나타낸다. 참고로 에너지 및 전력 밀도의 셀 대 팩의 추정 비율은 다음과 같다. 2020년에 65%(예: 1100W/kg(셀) × 65% = 715W/kg(팩)), 2025년 70%, 2030년 75%, 2035년에 80%이다.
2. 리튬이온 전지(모듈 및 팩) 로드맵 (출처: 영국자동차협회)
영국자동차협회에서 발간한 리튬이온 전지 보고서에는 셀과 팩에 대한 로드맵에 대하여 리튬이온 전지의 셀 디자인, 전기분배 시스템, 열, 기계적, 팩 통합, 수명 사이클 및 모듈 및 팩의 수명 주기 등에 대한 로드맵으로 그림 6과 같이 세분하였다.
리튬이온 전지팩을 안전하게 사용하기 위해서는 셀 제조 이후에도 전지 시스템 운영을 위한 배전 및 열관리, 보호 관리 등이 부가되고 있음을 알 수 있다.
전기 화학반응에 의한 전지 발열의 요인에는 분극 현상에 의한 반응열, 저항에 의한 Joule 열, 그리고 엔트로피 열 등이 있다. 여기에서는 발생 열의 처리 혹은 극한 환경에서 전지 시스템 내부의 열 물성(비열, 전도도, 밀도 등)과 작동조건(충·방전 속도, 외부온도 등)의 영향을 효과적으로 대처하는 기술들이 필요한 것으로 보인다.
3. 모듈 및 팩 로드맵(그림 6): 기술 분야별 개요 및 주요 개발내용
• 셀 형식 및 설계
규모의 경제를 지원하기 위해 점점 더 표준화되면서 다양한 차량 요구사항을 충족하도록 특화될 것이다.
- 대량 제조를 위한 통합 셀 형식 모듈
- 새로운 셀 형식 및 특성(예: 탭리스, 현장 계측, 열 유량 및 접합 개선 등)
• 전지 관리 시스템(Battery Management System: BMS, 하드웨어 및 소프트웨어 포함)
전지 셀 및 모듈의 전력 손실을 최소화하면서 지능적으로 분배되도록 한다. 이는 향상된 전지 관리 시스템, 버스 바(예, 공통 전극) 및 커넥터를 통해 달성할 수 있다.
- 400V 및 800V 아키텍처의 광범위한 채택, 새로운 1200V 아키텍처
- 과거 데이터를 이용한 BMS 업그레이드, 물리학 기반 SoH 및 SoC 셀 추적이 가능한 BMS, 자가 업데이트 알고리즘, 현장 데이터를 사용하는 AI 지원 BMS
- 원격측정 지원 BMS 아키텍처, 차량 오프라인 업데이트 및 실시간 모니터링
- 차세대 컨택터/커넥터(예: 솔리드 스테이트)
- 원가 및 중량 감소 버스 바, 전도도가 향상된 정형 다중 재료 버스 바
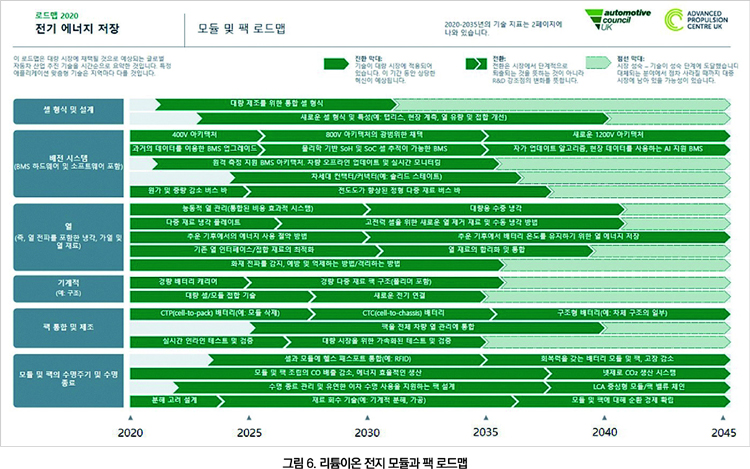
• 열(열 전파를 포함한 냉각, 가열 및 열 재료) 관리 시스템
전지 팩의 상태를 유지하는 데 매우 중요하다. 열을 관리하고 저온 및 고온의 영향을 완화할 수 있도록 향상된 능동 냉각 또는 가열 시스템으로 전지 셀을 가열 및 냉각할 수 있다.
- 능동적 열관리(통합된 비용 효과적 시스템), 대량용 수중 냉각
- 다중 재료 냉각 플레이트, 고전력 셀을 위한 새로운 열 제거 재료 및 수동 냉각 방법
- 추운 기후에서 에너지 사용 절약 방법, 추운 기후에서 전지 온도를 유지하기 위한 열에너지 저장
- 기존 열 인터페이스/접합 재료 최적화, 열 재료의 합리화 및 통합
- 화재 전파 감지, 예방 및 억제하는 방법/격리하는 방법
• 기계적(예 구조) 요소
모듈 및 팩의 무결점에 기여하는 하우징 및 접합 기술이 포함된다. 전지 케이스와 구조체는 무게를 줄일 수 있는 중요한 요소이다. 반면 새로운 접합 공정은 셀 간의 견고한 접촉을 보장해야 한다.
- 경량 전지 캐리어, 경량 다중 재료 팩 구조(폴리머 포함)
- 대량 셀/모듈 접합 기술, 새로운 전기 연결
• 팩 통합 및 제조
에너지 저장 및 관리를 차량에 통합하는 새로운 방법을 모색한다. 더 넓은 차량에 에너지 저장장치를 내장하고 열관리 시스템을 통합하는 것이 중요한 핵심이다.
- CTP(cell-to-pack) 전지(예: 모듈 삭제), CTC(cell-to-chassis) 전지, 구조형 전지(예: 차체 구조의 일부)
- 팩을 전체 차량 열관리에 통합
- 실시간 인라인 테스트 및 검증, 대량 시장을 위한 가속 테스트 및 검증
• 모듈 및 팩 수명 주기
전지 모듈 및 팩의 탄소 집약도(에너지 소모 정도), 환경 영향, 자원 소비 및 재활용 가능성이 포함된다. 이러한 요소를 개선해야 만 전기 자동차가 진정으로 지속 가능한 솔루션이 될 수 있다.
- 셀과 모듈에 헬스 패스포트 통합(예: RFID), 회복력을 갖는 전지 모듈 및 팩, 고장 감소
- 모듈 및 팩 조립의 CO2 배출 감소, 에너지 효율적인 생산, net-zero CO2 생산 시스템
- 수명 종료 관리 및 유연한 이차 수명 사용을 지원하는 팩 설계, LCA 중심형 모듈/팩 밸류 체인
- 분해를 고려한 설계, 재료 회수 기술(예: 기계적 분해, 가공), 모듈 및 팩에 대해 순환 경제 확립
4. 열(열 전파를 포함한 냉각, 가열 및 열 재료)
온도에 따른 성능 감소와 심각한 사고를 예방하기 위해서는 리튬이온 전지가 적절한 온도 범위 내에서 반드시 가동 및 보관되어야 하고, 이를 위해 적절한 열관리 기기 또는 시스템이 필요하다.
4.1. 능동 냉각 전략
강제 공기 또는 수동 냉각은 저 방전율 전지 팩에 적합하지만, 고전력 응용이나 고속 충전에는 충분하지 않다.
고에너지 및 고전력 전지 팩의 경우 냉각 플레이트를 사용하는 물/글리콜 냉각수 시스템으로 전환하는 추세이다. 가장 두드러진 열 문제는 (열 방출을 통해 상당량의 에너지를 낭비하는) 150kW 이상의 급속 충전 시 발생할 것으로 예상된다. 잠재적인 전략은 전지 사전 냉각, 추가 냉각 파이프 및 팬 또는 냉각수요 최소화를 위한 충전전력 감소이다.
장기적으로 모터스포츠 분야에 사용되는 수중 냉각 개념이 자동차 부문에 활용될 수 있을 것이다. 수중(또는 침지) 냉각은 셀과 버스 바(공통 전극)를 직접 냉각하는 유체 냉각 액체로 구성된다. 이를 통해 버스 바 두께와 무게를 줄이고 셀을 균일하게 냉각시킬 수 있다. 그러나 냉각 루프 무게 및 복잡성과 유체 재료 원가 때문에 이 접근 방식은 고성능 차량에 더 적합하다.
4.2. 수동 냉각 활성화
수동 냉각은 전지를 최적 온도로 유지하기 위해 히트 싱크, 히트 스프레더, 히트 파이프 또는 열 인터페이스 재료에 의존하는 에너지 효율적인 솔루션이다.
향상된 금속 매트릭스 복합 재료는 알루미늄 및 구리 냉각 플레이트와 비교하여 향상된 열전도율을 제공할 수 있다. 고 방전율 전지 팩이 시장에 진입함에 따라, 열을 즉시 방출할 수 있는 새로운 냉각 플레이트 재료가 필요하다. 위성 및 항공 우주 부문의 냉각 기술이 응용될 수 있지만, 자동차 부문에 적합하려면 공정 개선이 필요하다.
4.3. 전지 가열
추운 기후에서 작동하는 전지는 상당한 열화를 겪고, 특히 BEV 버스와 같은 응용의 경우 HVAC 시스템의 추가 요구사항을 통해 상당한 스트레스를 받는다. 또한 전지 팩을 최적 온도로 가열하는 데 사용되는 에너지는 전지 자체에서 발생하므로 열 관리 시스템 에너지 사용량을 줄이는 것이 우선이다.
4.4. 열, 접착 및 접합 재료 합리화
전지 모듈 및 팩에는 온도 및 구조적 무결성을 유지하기 위해 많은 열, 접착 및 밀봉 재료가 포함되어 있다. 접착 및 열관리 특성을 제공할 수 있는 다기능 재료는 전지 팩 내부의 습식 공정량을 줄이는 데 중요할 것이다. 이러한 새로운 수지와 재료는 수명 종료 규정을 준수하기 위해 재활용이 가능해야 한다.
4.5. 열 폭주 감지 및 방지
리튬이온 전지 및 기타 전지 화학물질의 화재 위험을 이해하는 것은 차량 내의 안전한 사용과 제조, 보관 및 운송을 위해 필수적이다.
열 폭주는 압력 증가, 가스 및 미립자 배출, 화재 또는 최악의 경우 폭발을 유발한다. 빠른 속도로 실행할 수 있는 향상된 테스트 및 검증을 통해 예방 및 억제 전략을 개발할 수 있다. 열 폭주를 저지하거나 확산할 수 있는 새로운 재료 및 설계 기능에 관한 추가적 연구가 필요하다.
5. 모듈 및 팩의 수명 주기 및 수명 종료
5.1 수명 전체에 걸친 추적 및 모니터링
신뢰할 수 있는 데이터를 보장하기 위해, 무선 주파수 식별(RFID)은 BMS가 보유한 상태 데이터를 보완하는 하나의 방법이다. BMS에는 일정 수준의 중복이 있지만, RFID는 생산 및 생산지에 대한 추가 데이터를 보유할 수 있다.
5.2 이차 수명을 가능하게 하는 전지 팩 설계
일정 기간 사용한 전기자동차용 전지의 재활용은 매력적인 옵션이 될 것이다. 주택, 그리드 밸런싱 및 상업 건물용 전기저장 장치 등에 전기 자동차용 전지의 재활용 방안은 매우 의미가 있을 것이다. 지속적으로 새로운 셀을 만드는 것보다 셀을 재사용하는 것이 환경적인 면에서 매우 매력적인 대안이 될 수 있다.
전지 팩의 기계식 설계를 단순화하면 재사용 가능한 모듈과 셀을 쉽게 추출할 수 있다. 이를 통해 재처리 비용을 줄이고 채택 가능성을 높일 수 있다. 마지막으로 전압, 전류 및 전지 상태를 정확하게 기록하고 시간 경과에 따라 성능을 수집할 수 있는 표준화되고 투명하고 충실도가 높은 BMS 데이터도 필요할 것이다.
5.3 전지 셀 추출 실현
전기 자동차용 전지가 이차 수명용으로 성공적으로 상용화되는지 여부에 관계없이 전지는 결국 재활용해야 한다. 전지 팩은 일반적으로 사용 단계에 맞게 설계된다.
실란트, 접착제 및 기계적 구조는 주행가능 거리, 성능 및 안전성을 극대화하도록 맞춤화된다. 전지를 효과적으로 재활용하려면, 구조가 단순한 전지 팩을 설계하고, 재활용 불가능한 접착제와 실란트를 제거하며 간단한 자동화 공구(인간 노동이 아닌)를 사용하여 전지 팩의 기계적 분해를 가능하게 하는 것이 최우선 과제이다.
전기 화학반응에 의한 전지 발열의 요인에는 분극 현상에 의한 반응열, 저항에 의한 Joule 열, 그리고 엔트로피 열 등이 있다. 여기에서는 발생 열의 처리 혹은 극한 환경에서 전지 시스템 내부의 열 물성(비열, 전도도, 밀도 등)과 작동조건(충·방전 속도, 외부온도 등)의 영향을 효과적으로 대처하는 기술들이 필요하다.
리튬이온 전지팩을 안전하게 사용하기 위해서는 셀 제조 이후에도 전지 시스템 운영을 위한 배전 및 열관리, 보호 관리 등이 필수적으로 부가되어 전지의 안전성을 관리하여야 한다.
영국자동차협회에서 발간한 리튬이온 전지 보고서는 셀과 팩에 대한 로드맵에 대하여 리튬이온 전지의 셀 디자인, 전기분배 시스템, 열, 기계적, 팩 통합, 수명 사이클 및 모듈 및 팩의 수명 주기 등에 대한 로드맵으로 세분하여 기술 로드맵을 참고하면 관련 전지 관리기술에 도움이 되기를 기대한다.
리튬이온 전지의 본격적인 대중화를 위해서는 전지팩 제조단가를 현재의 125$/kWh에서 2035년 1/2 이하 수준인 65$/kWh으로 낮추어야 한다. 이에 대한 대안으로 첫째, 비용량이 높은 양극 및 음극 소재 개발이 필요하다.
둘째는 현 리튬이온 전지 제조공정의 단순화 및 자동화를 위한 제조공정 혁신이다, 마지막으로, 사용 후 성능이 다소 낮아진 전지팩의 2차 활용과 관련 소재의 재활용이다. 이는 제조산업의 친환경 정책과도 잘 맞는 부분이다.
정부는 2021년 7월, 2030 이차 전지 산업(K-Battery) 발전전략을 발표하였다. 리튬이온 전지 관련 기업들뿐만 아니라 산학연관 협력에 의한 기술개발의 장을 마련하고 있으며, 전지 산업 밸류체인 형성을 위하여 노력하고 있다.
한 분야에 명성과 신뢰를 쌓기는 어려워도 잃는 것은 한순간이다. 그동안 공들여 쌓은 리튬이온 전지의 국제적 선두자리를 잃지 않도록 모두 힘을 합하여 리튬이차전지 산업의 한계를 극복하고, 지속 성장하기를 바라는 마음이다.
주1) 리튬이온 이차 전지가 정식 명칭이지만, 본 원고에서는 리튬이온 전지(Lithum ion Battery: LIB)로 표기하였다.
주2) 본 심층 보고서의 내용은 리뷰 자의 주관적 의견이고, 관련 회사의 공식 입장과 다를 수 있다.
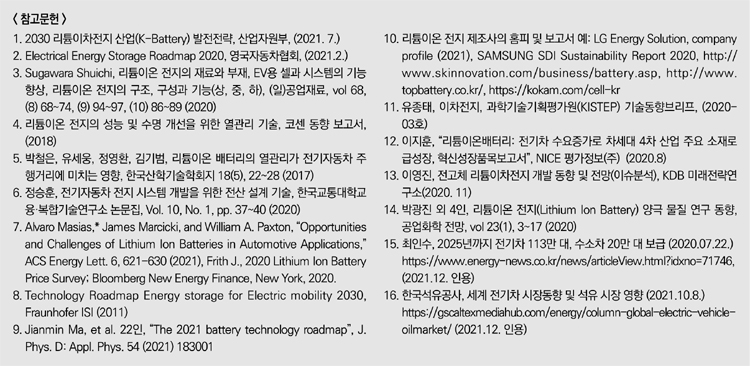
