기술과 솔루션
㈜우진플라임 사출성형기 “다단 사출로 성형하라”
작성자 : 편집부
2022-06-12 |
조회 : 5129
자료제공: 우진플라임 기술교육원 / 교수 한선근
1. 성형기술의 중요성
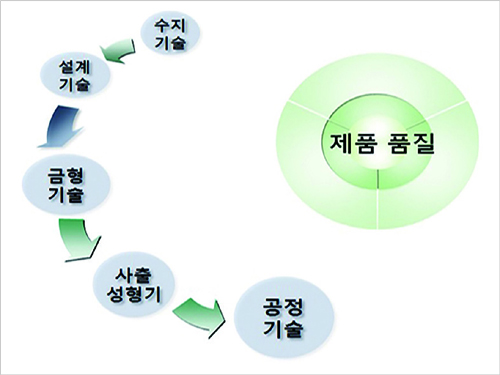
위 그림에서 보는 것처럼 사출성형 기술은 여러 가지 광범위한 지식과 기술이 모여 사출성형 기술이라는 하나의 기술이 완성되는 종합적인 기술의 집약체이다. 그리고 이와 같은 기술의 집약체를 통해 성형품이라는 결과물로 도출된다.
따라서 어느 한 과정에서 발생하는 문제점은 품질에 영향을 줄 수 있다. 따라서 모든 성형 기술자는 성형기술의 기본적인 부분을 이해하고 성형을 하여야 한다.
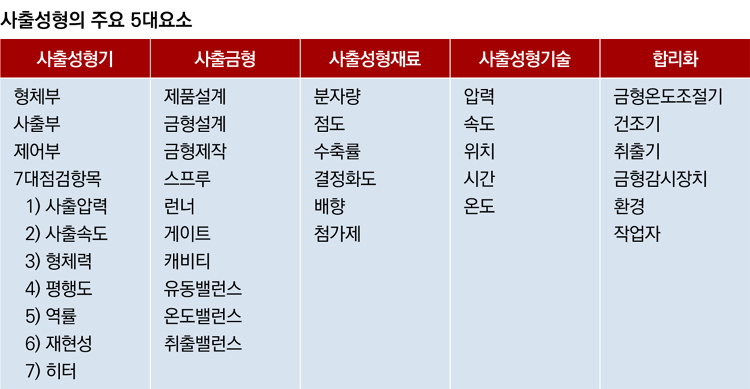
2. 성형조건의 5대 요소
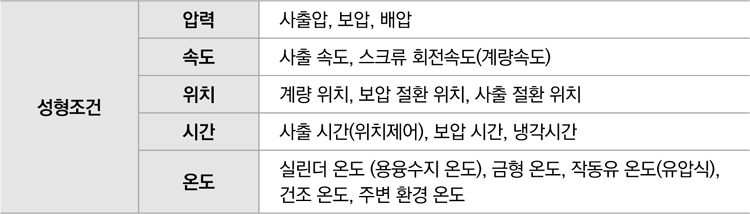
위 표의 요인은 상호에게 영향을 주어 모든 조건을 임의로 설정하는 것은 곤란하다.
3. 사출 속도
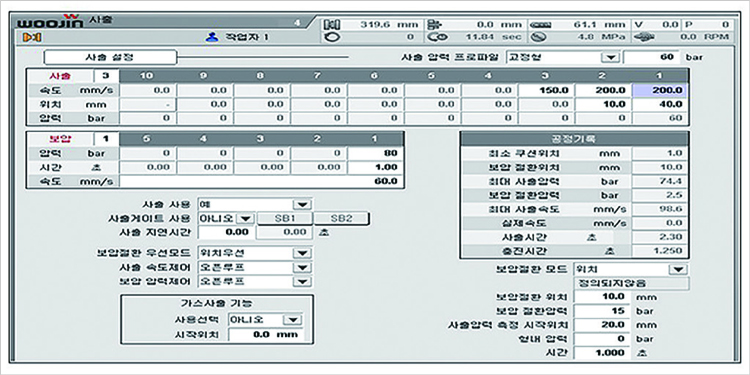
사출 속도는 수지의 유압 속도를 조정한다. 사출 속도 조정을 통해 성형품 표면의 불량 현상(젯팅, 플로우 마크, 웰드라인) 등을 해결할 수 있다.
4. 사출 압력(Injection Pressure)
스크류 선단의 수지에 작용하는 최대 압력을 말한다. 유압식의 경우 스크류 전체에 작용하는 유압의 힘(사출력)을 스크류 단면적에서 뺀 이론치로 표시된다.
스크류 직경을 바꾸는 것은 직접 사출 압력을 바꾸는 것이 되므로 스크류 직경을 가늘게 하여 사출 압력을 높게 하는 경우 사출 용량, 사출률, 가소성 능력의 감소를 고려해야 한다.
5. 이론 사출량과 실 사출량
사출성형을 하기 전 이론 사출량과 실 사출량을 알고 있으면 편리하다. 계량량을 예측할 수 있고 가상의 성형조건을 설정할 수 있다. 이론 사출량과 실 사출량 수식과 수지별 상수는 사출기 선정의 이론 사출 용량을 구하는 공식은 아래 표와 같이 구할 수 있다.
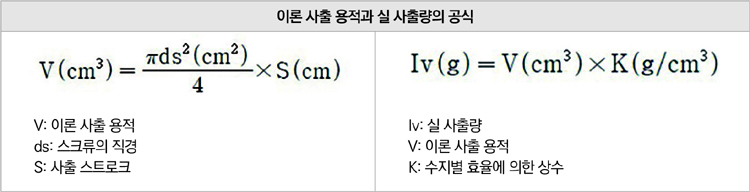
1) 다단 사출이란?
압력, 속도, 위치를 2단계 이상으로 조건을 설정하여 수지를 금형에 밀어 넣는 것을 뜻한다. 압력, 속도, 위치가 2단계 이상이면 다단 사출이라 할 수 있다.
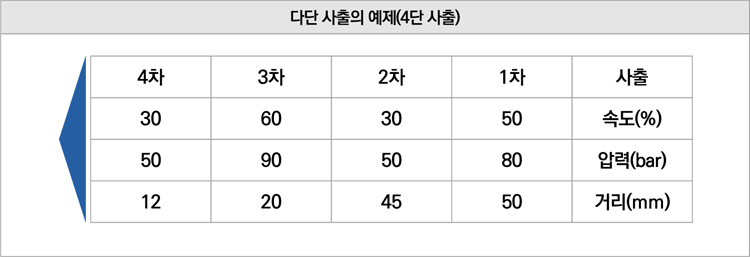
2) 위와 같이 조건을 나누어 설정하게 되면, 불량이 나타나는 구간을 나누어서 불량을 해결할 수 있다. 제품에서 문제점이 되는 Point가 몇 군데인지 파악하여 단계가 최소 2~최고 10단계까지도 설정할 수 있으며, 불량이 있는 구간을 나눈 후 구간의 속도와 압력을 조정하여 불량을 해결할 수 있다.(사출 단계 및 화면의 구성은 각 성형기의 모델과 제조사에 따라 다를 수 있음)
3) 다단 사출 구간 설정 방법
사출(충진)의 단계에서 제품의 두께, 형상, 수지의 종류에 따라 다르지만 95~98% 정도를 성형시킨다. 사출 구간에서 100% 성형하는 것은 바람직하지 않다. 이러면 경우에 따라 오버 패킹, 잔류응력 등으로 휨, 뒤틀림, 백화 등의 불량이 발생할 수 있다.
① 1단 사출 : 게이트 전(캐비티 내 수지의 충진성을 위해 중고속으로 사출)
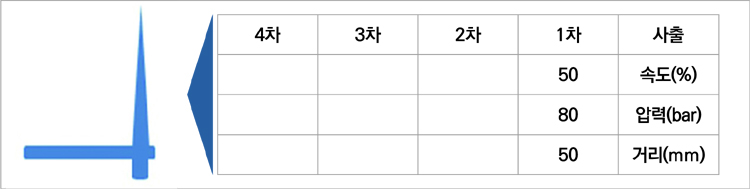
계량을 완료하고 게이트 앞쪽까지 사출을 진행하는 것으로 속도와 압력은 50% 이상으로 설정을 하는 것이 좋다. 스프루와 런너에서 나올 수 있는 불량이 없기에 빠르고 조금 높은 압력을 사용하여도 무방하다.
② 2단 사출 : 게이트 후(젯팅, 게이크 마크 방지를 위해 저속으로 사출)
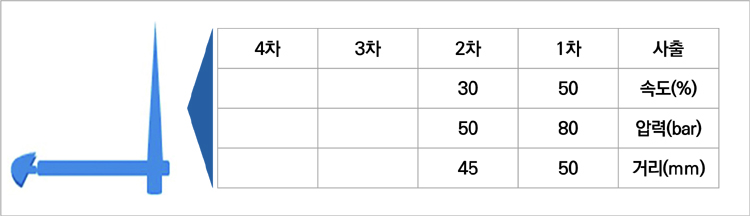
2차의 위치는 게이트를 지나서 조금 사출될 정도의 거리를 찾는다.
2차 사출은 대부분 저속으로 사출을 하여야 되기 때문에 정밀도 높은 제품은 1차와 2차의 위치를 최소로 하는 것이 좋으며 일반적인 제품은 1차와 2차의 위치의 범위를 넓게 하는 것이 양산 시 재현성에 문제가 없다.
③ 3단 사출 : 성형품 80~90%(웰드. 플로우 마크, 방지를 위해 중고속으로 사출)
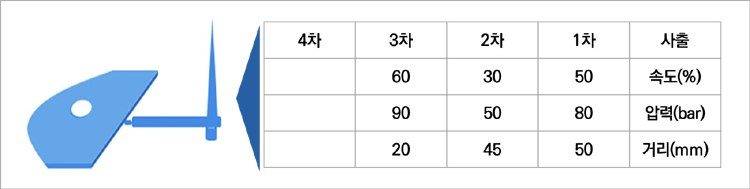
사출 단계는 제품을 80~90% 정도를 사출한다. 이는 규정된 것은 없으며 성형품의 모양, 불량 등 다양한 요인에 따라 변할 수 있으므로 제품의 형상과 불량을 잘 파악하고 사출을 진행하여야 한다.
④ 4단 사출 : 성형품 95~98%(Gas 몰림으로 인한 탄화 방지를 위해 저속으로 사출)
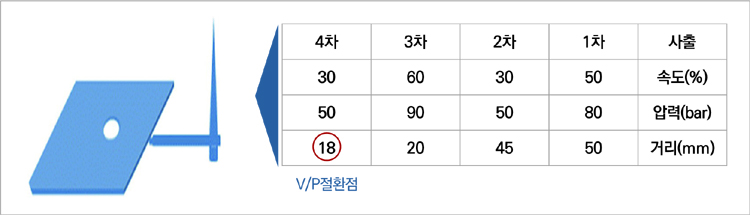
사출 단계를 4단으로 늘리고 성형품의 95~98% 정도 사출한다. 이때 사출되는 거리가 보압 절환점(V/P 절환점)이 된다. 성형품의 두께, 형상에 따라 4차에 사출되는 거리는 달라질 수 있으며 과패킹, 잔류응력 방지를 위해 사출로 100% 성형하지 않는 것이 중요하다.(미세하거나 매우 얇은 성형품 또는 사출기 압력이 부족한 경우는 100% 성형하기도 함) 이와 같은 방법으로 다단 사출을 진행하여 각각의 위치를 찾게 되면 불량이 나타나는 구간의 속도와 압력을 조정하여 불량을 해결할 수 있다.
아래 그림은 사출(충진) 구간의 사출 속도를 위치별로 표시한 것이다.
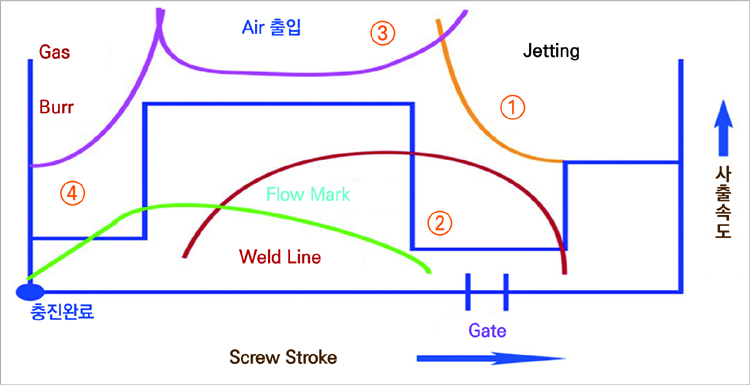
⑤ 보압 설정하기
수지가 용융 상태에서 냉각되면서 수축이 발생하게 되는데 이 수축량을 보상하기 위해 압력이 필요한데 이걸 보압이라 한다.
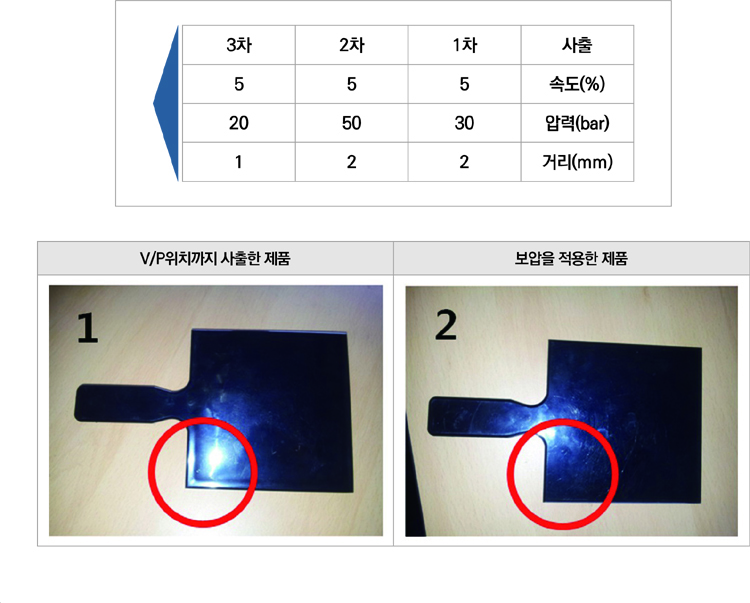
보압은 속도로 제어하는 구간(사출, 충진)에서 압력으로 제어하는 구간(보압)이다.
보압도 3차까지 설정을 하는데, 1차 보압은 저압으로 설정 스킨층 형성(Burr에 대한 대책) 2차 보압은 1차 보압 보다 압력은 높게(수축, 치수 해결) 설정한다.
3차 보압은 2차 보압 보다 낮게 설정하여 게이트 Seal까지 압력 유지, 뒤틀림, 과패킹, 잔류응력 방지를 위해 저압으로 설정한다.
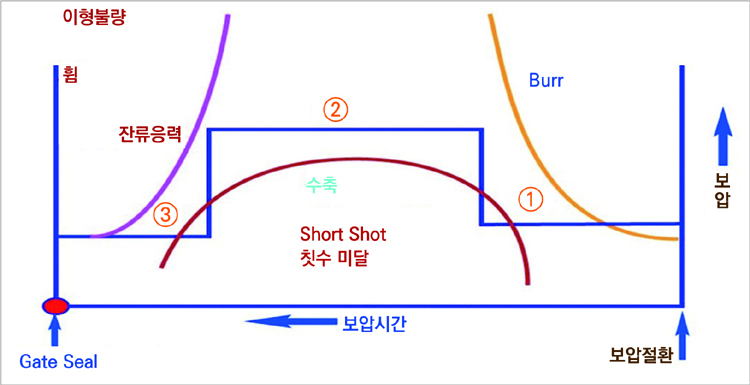
