기술과 솔루션
자동차자동차용 고분자 소재의 난연 기술용 고분자 소재의 난연 기술
작성자 : 편집부
2023-04-16 |
조회 : 6285
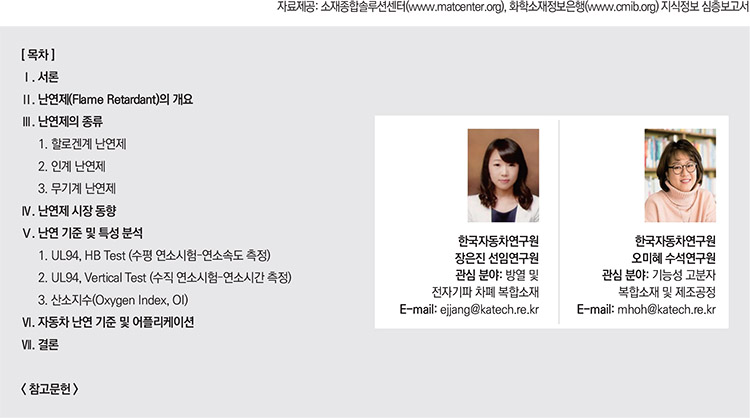
Ⅰ. 서론
경제성장, 도시화, 소득증가, 전자상거래 등의 급속한 확산은 가전제품과 전기·전자 제품, 자동차 등 소비재에 대한 수요의 성장을 촉진시켰고, 환경, 에너지, 안전 등과 관련된 엄격한 규제와 표준은 경량화 이슈로부터 금속에서 플라스틱으로의 소재 변환을 포함한 여러 변화를 이끌어냈다.
고분자 소재는 금속이나 세라믹 소재에 비해 내열성, 난연성 등은 떨어지지만 가볍고, 디자인 성형 가공성이 높은 강점으로 인해 생활용품에서 자동차, 전기·전자, 기계, 산업 분야에서 광범위하게 사용되고 있다.
고분자의 장점을 확대하고 결점을 보완하기 위한 방안 중 하나로 고분자에 첨가제를 사용한다. 첨가제는 플라스틱 또는 합성수지의 가공을 용이하게 하고 최종제품의 성능을 개량하기 위해 가공이나 중합 과정에서 첨가되는 물질로, 플라스틱의 취약성을 보완하고 요구 특성을 향상시키기 위해 사용된다.
첨가제에는 가소제, 열안정제, 산화방지제, 자외선안정제, 난연제, 활제, 충격보강제 등이 있으며, 제품의 기능, 용도에 따라 필수 불가결하게 첨가되는 물질들이다.
주재료인 Base Polymer에 제품의 물성을 향상시키거나 안정성 개선, 기능성 부여 혹은 원가절감을 목적으로 적절한 첨가제를 혼합하여 압출하거나(Compounding) 분산시킨 제품이 실용적으로 사용되고 있다.
범용수지, 열 경화 수지, 엔지니어링플라스틱에 대한 수요가 지속적으로 늘고 있다. 엔지니어링플라스틱(EP)의 세계 시장규모는 2018년부터 2023년까지 연평균 성장률(CAGR)은 3.51% 성장을 예측하고 있다. [그림1] 금속보다 다양한 응용이 가능한 경량 고기능 플라스틱에 대한 선호도가 높아짐에 따라 시장 확대가 촉진될 것으로 추정된다.
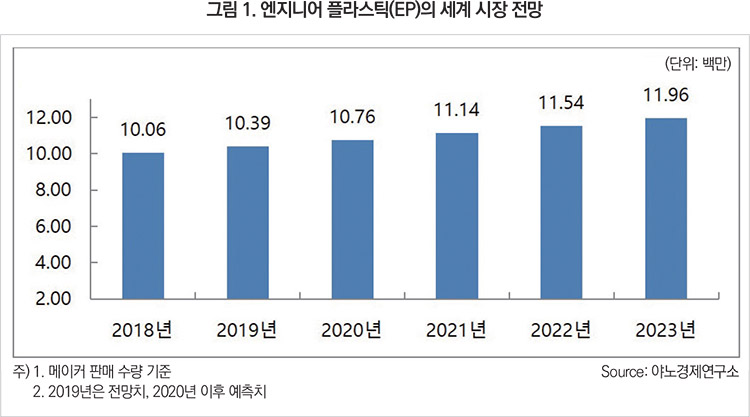
기능성 플라스틱에 대한 전 세계 수요는 꾸준한 성장을 기록하고 있으나, 기능성 플라스틱의 사용이 증가함에 따라 일반 가정과 차량은 화재 위험에 더욱 취약해졌다.
플라스틱은 일단 연소가 되면 소화가 어렵고, 연기나 유독가스가 발생하여 인체 유해성 문제가 발생한다. 따라서 화재가 발생하지 않도록 하는 것이 중요하다.
안전성을 고려한 각종 규제에 적합하고, 친환경적이며 인체에 유해하지 않은 난연제 개발이 필요하다. 자동차부품의 고분자 소재에 대한 난연성 및 방염처리는 지속적으로 개발이 필요한 상황이다.
Ⅱ. 난연제(Flame Retardant) 개요
난연제는 가연성을 감소시키거나 연소를 지연시키는 데 사용되는 물질이다. 플라스틱, 직물, 표면 마감, 코팅과 같은 제조된 재료에 첨가되는 다양한 화학물질을 포함한다. 플라스틱은 대부분 탄소, 수소 및 산소로 구성되어 있는 유기물로 가연성을 가지고 있기 때문에 용도에 따른 난연제의 사용이 필요하다.
고분자 소재의 난연 방법에는 소재 디자인 또는 분자구조 설계로 열적 안정성을 갖는 수지의 합성, 기존 고분자의 화학적 개량(반응형 난연제), 난연제의 블렌딩 또는 컴파운딩을 통한 물리적 첨가(첨가형 난연제), 난연제 코팅 또는 페인팅 방법 등이 있다.
이중 할로겐계(브롬계 및 염소계), 인계, 질소계, 무기계 난연제를 블렌딩 또는 컴파운딩 방법으로 혼합하는 것이 열가소성 고분자에 가장 많이 사용된다. 난연제는 사용법에 의해 첨가형과 반응형으로 나뉘고, 구성성분에 따라 유기계와 무기계로 분류된다. [표1]
무기계(첨가형)는 난연제 시장에서 가장 큰 부분을 차지하는데 가격이 싸고 할로겐화 유기화합물과 상승작용을 일으키며 충전제로 사용할 수 있기 때문이다. 유기계(첨가형)는 고분자와 컴파운딩이 쉽다는 장점이 있으며, 반응형은 난연 효과는 뛰어나지만 실제로는 코폴리머로 작용하기 때문에 비용이 많이 들고 제조하는 데 시간이 오래 걸리는 단점이 있다.
고분자 소재는 탄소, 산소, 수소를 주성분으로 이루어져 있기 때문에 연소되기 쉬운 것이 많은데 PE, PP, PS 등은 연소할 때 약 10kcal/g의 연소열이 발생한다. 비교적 연소되지 않는 PVC도 4.3kcal/g의 연소열이 발생된다. 연소 현상에는 가연성 성분, 산소, 열에너지가 필요 요소이며, 난연화의 기본은 이를 제거하는 것이다. [표2]
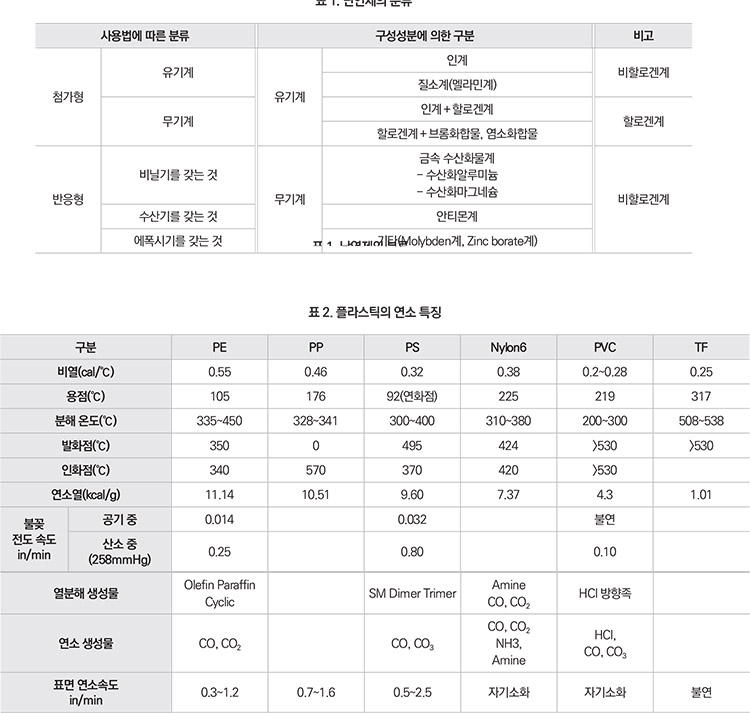
Ⅲ. 난연제의 종류
난연제는 크게 할로겐계 난연제, 인계 난연제, 무기계 난연제, 난연 상승제 등으로 나누어지며, 각각의 난연 메카니즘이 조금씩 차이가 있어 원하는 난연도를 얻기 위해서는 난연제의 종류와 양을 적절히 선택하여 사용해야 한다.
1. 할로겐계 난연제
할로겐계 난연제의 주된 난연 메커니즘은 가스상에서 라디칼 트랩 효과에 의한 OH 라디칼의 안정화이다. 연소의 추진역할을 하는 활성 OH와 활성 H가 라디칼 HX에 의해 트랩되어 안정화되는데, HX는 불연성이고 희석효과와 함께 산소를 차단하는 효과가 있다.
할로겐계 난연제는 브롬계와 염소계로 나눌 수 있지만, 브롬계 난연제가 압도적으로 많다. 브롬계 난연제는 난연화 효과가 뛰어나며, 비용 대비 성능 면에서 뛰어난 난연제로 전기기기나 OA기기의 하우징 재료, ABS, PS, PBT, PET, 에폭시 수지 등의 주요 난연제로 사용되고 있다. 소량이 사용되므로 고분자 수지의 물성에 큰 영향을 주지 않는다는 장점이 있다.
현재 환경문제로 큰 압박을 받고 있으나, 난연 특성이 매우 우수하고, 아직까지는 브롬계 난연제는 대체할 만한 난연제가 개발되지 않아 국내/외에서 계속되고 있는 대체제에 대한 연구와는 별도로 브롬계 난연제의 수요가 해마다 늘고 있다.
염소계 난연제는 염소화 파라핀, 염소화폴리에틸렌, 지방족 염소계 난연제 등이 있으며, 염소계 파라핀 및 폴리에틸렌의 경우 가격이 저렴하나 열 안정성에 취약하며, 지방족 난연제의 경우 가격이 다소 비싸다. 브롬계에 비해 난연 효율성이 다소 낮다.
할로겐 난연제의 종류로는 데카브로모디페닐 옥사이드(DBDPO, Decabromodiphenyl oxide), 데카브로모디페닐 에탄(DBDPE, Decabromodiphenyl ethane), 헥사브로모사이클로이도데칸(HBCD, Hexabromocyclododecane), 테트라브로모비스페놀-A(TBBA, Tetra bromo bisphenol-A), 테트라브로모비스테놀 A 비스 2,3-디브로모프로필 에테르(BDDP, Tetra bromobisphenol A Bis 2,3-didromopropyl ether) 등이 있다.
2. 인계 난연제
인계 난연제는 연소할 때 열분해에 의해 폴리메타인산을 생성하고, 이것이 보호층을 형성하는 경우와 폴리메타인산이 생성될 때의 탈수 작용에 의해 생성되는 탄소 피막이 산소를 차단하여 연소를 막는 경우가 있다.
인계 난연제는 크게 무기계와 유기계로 분류하며, 무기계로는 크게 적인, 암모늄 포스페이트, 암모늄 포리포스페이트 등이 사용된다. 적인은 응축 상에서의 분해를 방해하고 탄화율을 높여 난연 작용을 하며, 주로 나일론 에폭시 수지 등에 사용된다.
암모늄 포스페이트는 셀룰로스, 직물, 종이, 나무 등에 사용된다. 암모늄 폴리포스페이트는 탄화 촉진을 통한 난연 작용으로 폴리엔, 에틸렌-비닐 아세테이트, 우레탄 탄성중합체에 첨가되어 사용하기도 한다. 유기계에는 지방족 유기인 첨가제 및 할로 알킬 포스페이트 등이 있으며, 이때 chloroalkyl 작용기는 난연제가 증발하거나 물에 녹아 씻기는 것을 막아준다.
인계 난연제의 종류로는 암모늄 폴리포스페이트(APP, Ammonium Polyphosphate), CG-P(Red Phousphours), 트리스2-클로로에틸 포르세이트(TCEP, Tris(2-chloroethyl)phosphate), 아이소포로필페닐 다이페닐 포스페이트(IPPP, Isopropylphenyl Diphenyl phosphate), 트리페닐 포스페이트(TPP, Tripheyl phosphate), 트리에틸 포스페이트(TEP, Triethyl phosphate) 등이 있다.
3. 무기계 난연제
열에 의해 휘발되지 않으며 분해되어 물, 이산화탄소, 이산화황, 염화수소와 같은 불연성 기체를 방출하게 되며 흡열반응을 한다. 기체상에서는 가연성 기체를 희석시켜 플라스틱 표면을 도포하여 산소의 접근을 방지하고, 동시에 고체상 표면에서 흡열반응으로 플라스틱 냉각 및 열분해 생성물의 생성을 감소시키는 효과가 있다.
무기계 난연제는 종류가 많지만, 주로 플라스틱용으로 생산되는 수산화알루미늄, 산화안티몬(삼산화, 화산화), 수산화마그네슘, 주석산아연, 인제품, 구아니딘, 몰디브덴산염, 지르코늄 등이 무기계 난연제에 포함된다. 이러한 난연제들은 각각 특성이 다르고 첨가하는 양에 따라 많게는 수지 양의 50wt% 이상에서 소량 첨가까지 다양하다.
무기계의 주요 제품은 수산화알루미늄, 안티몬계로 수산화알루미늄은 가격이 싸고 첨가량이 많다. 수산화알루미늄은 무기계 대표적 난연제로 난연제 전체의 30%를 차지하고 있는데, 무독성(할로겐비 함유), 저 발연성으로 가공 기계의 부식성이 적고 전기절연성도 우수하며 가격이 싸기 때문에 현재 가전제품, 자동차, 건축, 전선, 케이블 등 분야에서 난연 충진제로 사용된다.
수산화알루미늄은 분해 온도가 낮아 가공온도가 230℃ 정도로 낮은 고분자 수지에만 사용 가능하며, 다량 사용해야 하는 단점으로 인해 고분자 수지의 물성에 영향을 줄 수 있다.
흡열 분해에 의해 물을 생성하여 난연 효과를 얻고, 생성수에 의한 냉각 작용으로 연소를 방지한다. 분말 입자 사이즈에 따라 다양한 용도로 사용할 수 있다. 난연화 대상 수지로는 UPE, 페놀, 에폭시, 멜라민, 아크릴 등의 열경화성 수지를 비롯해 PVC, PE, PP, EVA 및 합성고무, 라텍스, 제지, 합성섬유 등이 있다.
삼화안티몬은 녹는점이 656℃로 높고, 입자가 미세하여 분산성이 좋다. 할로겐계 난연제의 난연성을 증가시키기 위한 보조제로 이용되기도 하며, 안티몬의 할로겐화물은 연소할 때 기상이 된 할로겐 화합물이 라디칼 반응을 정지시켜 난연 효과를 얻는다. 다양한 응용성과 저가의 가격이 장점이다.
난연 대상은 UPE, 페놀, 에폭시, 폴리우레탄, PVC, PE, PP, PS, ABS 등 각종 범용 합성수지와 고도의 난연 효과가 요구되는 엔지니어링플라스틱까지 광범위하게 사용되며, 투명성을 요구하는 MMA 수지에는 아직 적용되지 않고 있다.
수산화마그네슘은 연기 발생이 적고, 부식성이 낮으며, 높은 온도 안정성이 장점이다. 각종 산화마그네슘의 원료, 중간체로서 사용되고 있고, 배합량 당 난연 효과는 수산화알루미늄보다 우수하다.
분해 온도가 수산화알루미늄보다 약 100℃ 정도 높은 약 330℃에서 분해된다. 특히 적인, 카본블랙 등과 함께 사용하면 난연효과가 상당히 향상된다. 난연대상은 폴리올레핀, 나일론, PVC 등과 일부 합성고무 등에서 사용한다. 현재 가격이 싸고 유독가스 및 연기 발생을 억제하는 등의 특징을 갖고 있어 향후 안정적인 수요가 예상된다.
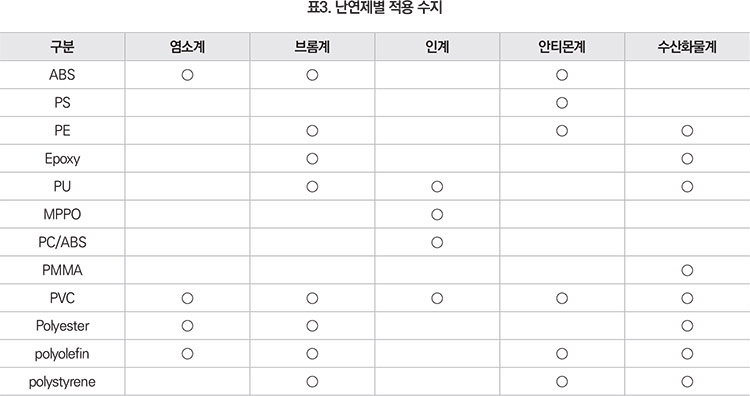
Ⅳ. 난연제 시장 동향
난연제의 전 세계 소비량은 연간 225만 톤 이상이다. IHS Consulting의 2017년 시장조사에 따르면, 수산화알루미늄은 38%의 점유율로 가장 큰 단일 난연제이며, 할로겐계 난연제는 일반적으로 상승효과를 위해 산화안티몬과 함께 혼합되어 사용되는 브롬계 및 염소계 제품으로 총 31%를 구성한다.
유기 인 및 기타 난연제(예: 무기 인화합물, 질소 및 아연 기반 난연제)는 나머지를 31%로 구성된다. 지난 10년 동안 기존 할로겐계 난연제를 보다 지속 가능한 비 활로겐계 제품으로 대체하는 추세가 있었다.
난연제의 소비는 지난 4년 동안, 특히 전자 제품에서 크게 증가했으며, 2016년에서 2021년 사이에 매년 3.1%의 연간 성장률로 계속 증가할 것으로 예측하고 있다. 난연제는 주로 플라스틱/수지 산업에서 소비되고, 섬유 및 고무 제품이 나머지 대부분을 차지한다.
아시아는 2016년 50%의 점유율로 가장 많은 양의 난연제를 소비했으며, 중국은 26%로 가장 큰 단일 소비자였다. 세계 난연제 시장의 상위 5개 업체는 2017년 전체 시장 점유율의 48%를 차지하며, 경쟁 우위로 인해 주요 업체는 국제 및 현지 시장에 더 집중하고 있다.
또한 제품 업그레이드를 통한 판매량을 늘리는 데 주력하고 있다. 예로, 2017년 10월 랑세스는 PBT, PA6, PA66를 기반으로 비 할로겐 난연제의 제품군을 확장했다. 다른 주요 회사는 BASF SE, Clariant, ICL, Italmatch Chemicals S.p.A, MPI Chemie B.V., Albemarle, Broadview Technologies, Dover Corporation 및 Thor Group Ltd 등이 있다.
우리나라의 경우 난연제 시장은 종류별 시장규모가 작아 대기업은 주로 응용제품인 난연 수지 개발에 관심을 가지고 있으며, 국내 난연제 생산업체들은 중소기업으로 이루어져 있다. 국내 난연제 시장은 글로벌 메이커로부터 제품을 수입하여 공급하고 있는 수입 에이전트들이 시장을 주도하고 있으며, 수십 개의 수입업체가 각각 종류의 제품을 대규모 장치산업의 수요 기업들에게 공급하고 있는 수요자주도 시장구조이다. 글로벌 경쟁력 강화를 위한 대·중소기업 상생 방법 모색이 필요하다.
중소기업의 기술력 향상과 시장 안전성을 위한 Value chain 구조를 만들어야 하며 비경쟁 기업 간의 협력관계 또는 보완적 협력관계를 구축할 필요가 있다.
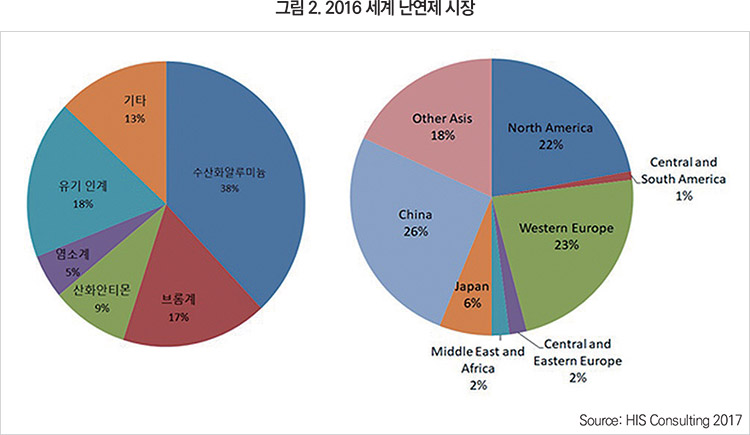
Ⅴ. 난연 기준 및 특성 분석
난연화 기술을 통해 난연성이 부여된 수지들의 난연성 측정 방법에는 연소속도 측정(UL94, HB Test), 연소시간 측정(UL94, Vertical Test), 산소지수(Oxygen Index) 측정 등이 있다.
제품에 의한 신체 상해, 인명 및 재산피해를 줄이고, 방지하기 위한 제품의 안전에 관한 표준 개발 및 평가를 진행하는 UL(Underwrite Laboratories Inc.)은 미국 내에서 신뢰성이 높이 평가되고 있으며, 소비자들의 선호가 높기 때문에 생산업자, 판매자, 수입업자 대부분이 요구하고 있다.
난연제 평가등급으로 활용되는 UL94는 전기전자제품 등의 난연성을 평가하는 항목으로 난연성을 시험하는 방법에는 시편을 수평으로 놓고 불을 붙여 측정하는 방법으로 UL94HB(Horizontal Burning Test)와 시편을 수직으로 세워놓고 시험하는 방법인 UL94V(Vertical Buring Test)가 있다. UL94의 난연 등급은 HB
1. UL94, HB Test(수평 연소시험 – 연소속도 측정)
UL94HB는 시험 시편을 수평으로 설치해 놓고 버너로 불을 붙여 1분 동안 타들어 간 길이를 평가하는 것으로 수직 시험보다 규격 자체가 까다롭지 않기 때문에 일반적으로 플라스틱의 경우 대부분 이 수준을 만족시키고 있다. 이는 가장 낮은(최소 화염 저항) UL94 등급이다.
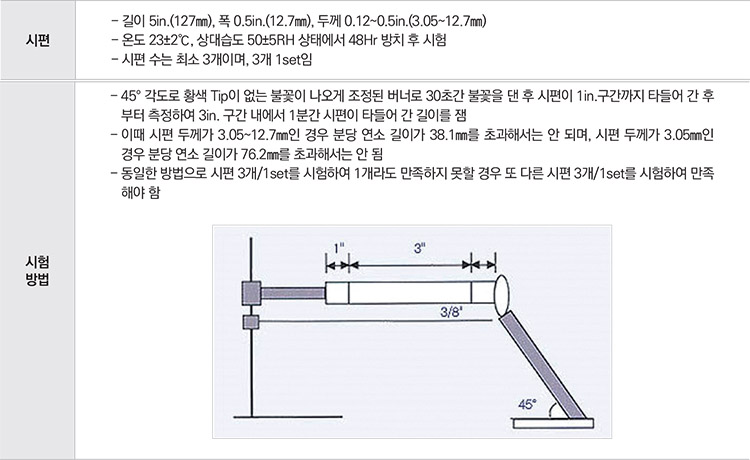
2. UL94, Vertical Test(수직 연소시험 – 연소시간 측정)
UL94V는 시편을 수직으로 세워놓고 버너로 시편에 불을 붙여 일정 시간 내에 저절로 시편에 붙은 불이 꺼지는 정도를 평가하는 것으로 불이 꺼지는 정도에 따라 V-2, V-1, V-0, 5V 등으로 나뉜다.
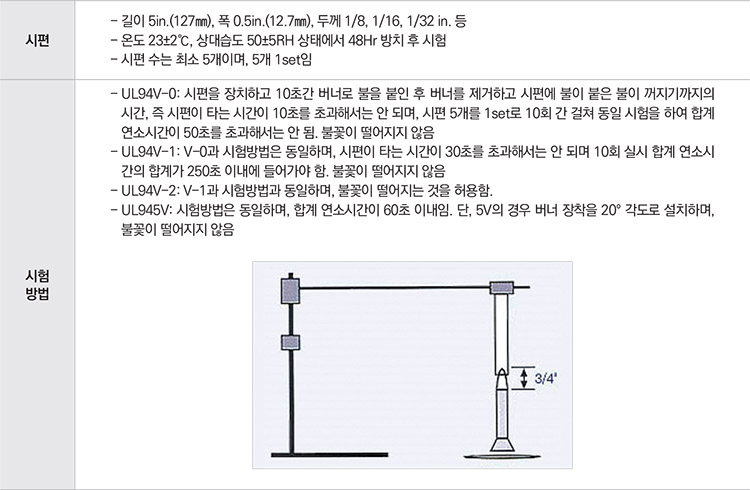
3. 산소지수(Oxygen Index, OI)
난연화는 가연성 성분, 산소, 열에너지를 제어하는 것인데, 연소 시 필요한 산소량을 측정하면 플라스틱의 난연 특성을 예상할 수 있다. 산소지수(Oxgen Index, OI)는 일정 수지가 연소되기 위해 필요한 산소의 농도로 분자구조에 따라 결정된다.
일반적으로 물질의 점화 또는 발화 저항성이 클수록 산소지수 값은 크다. 공기 중 산소 농도가 약 20% 정도이므로, 산소지수가 20 이상인 재료들은 일반적인 대기에서 연소되기 어렵고, 산소지수가 20 이하인 재료들은 쉽게 연소가 이루어진다고 판단할 수 있다.
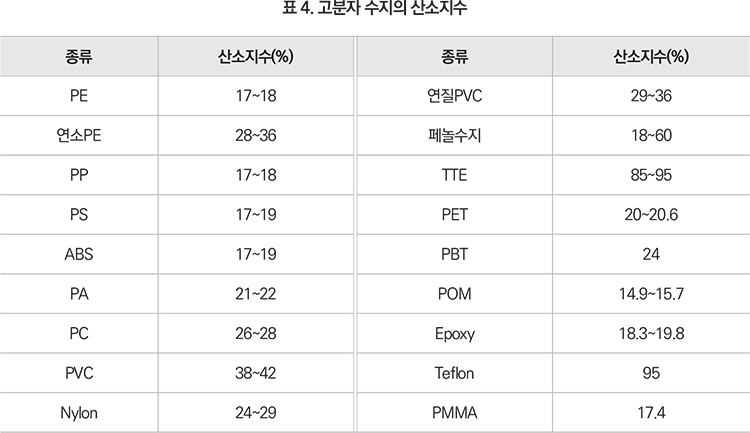
Ⅵ. 자동차 난연 기준 및 어플리케이션
자동차의 난연 기준은 다양하므로 자동차 엔지니어는 재료 선택 시 특정 국가, 국제규격 또는 산업 요구 사항을 고려해야 한다. 미국의 자동차 내부 인테리어 난연 기준은 FMVSS 302에 따라 테스트 된다. 유럽, 캐나다 및 일본에서는 ISO 3795가 기술적으로 동등한 표준이며, 중국 GB 8410, 영국 BS AU 169a 및 기타 여러 국가에서도 자동차의 난연 표준을 유지한다.
Mitsubishi, Mercedes-Benz 및 Volvo와 같은 완성차 업체도 자체 난연 사양을 가지고 있다. FMVSS 302와 같은 표준은 자동차 내부에 적용되지만, 난연성 폼에도 사용된다.
자동차 제조업체가 더 많은 전자 제품을 추가함에 따라 UL94V-0 및 UL94HB는 엔진 구성 요소의 더 많은 부품에 나타난다. VOC(Volatiile Organic Compounds)가 낮은 발포체에 대한 업계의 관심은 GADSL(Global Automotive Declarable Substance List)에 나타나는 난연제 사용에 대한 의사결정을 주도하고 있다. (https://www.gadsl.org)
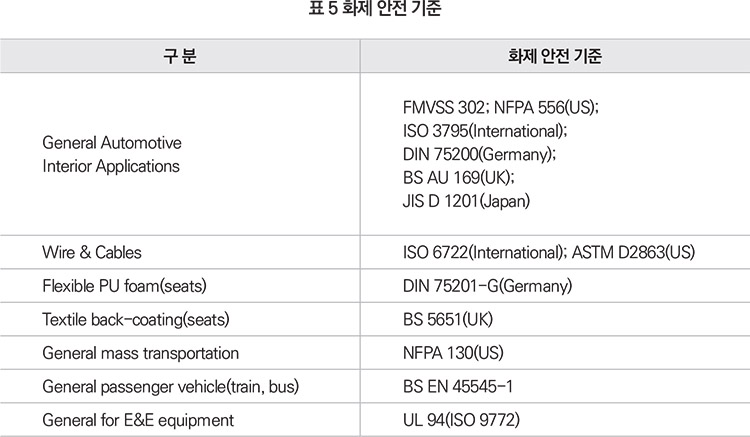
FMVSS 302 및 기타 화재 안전 표준에는 팔걸이, 헤드라이너, 시트 백, 시트 쿠션, 선바이저 및 트림 패널과 같은 내부 구성 요소에 사용되는 자동차 폼이 포함되며, 난연성 자동차 폼은 공기 흡입구, 매니폴드, 펌프 및 캠 및 밸브 커버에 사용된다.
전기자동차에서 난연성 플라스틱 재료는 배터리 모듈, 충전기 커넥터, 차량측 소켓, 충전 건 등과 같은 구성 요소에 사용되며, 모두 난연성 소재로 부품을 만들어야 한다.
전기자동차용 충전 커넥터는 충전 스테이션과 같은 충전 시설을 전기자동차와 연결하며 충전 성능과 안전에 직접적인 영향을 미친다. 우수한 성능을 갖춘 플라스틱 하우징은 현재 전원 배터리 하우징의 주요 개발 방향이며 점점 더 많은 기업이 난연성 맞춤형 플라스틱 부품을 사용하여 전원 배터리를 사용하기 시작했다.
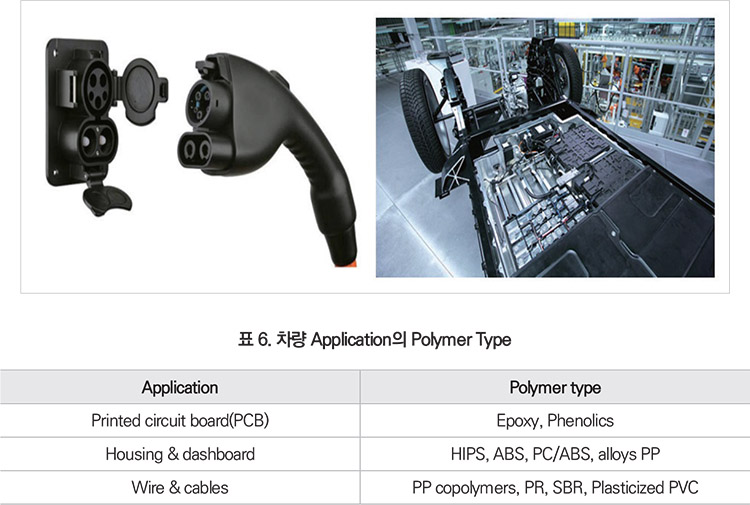
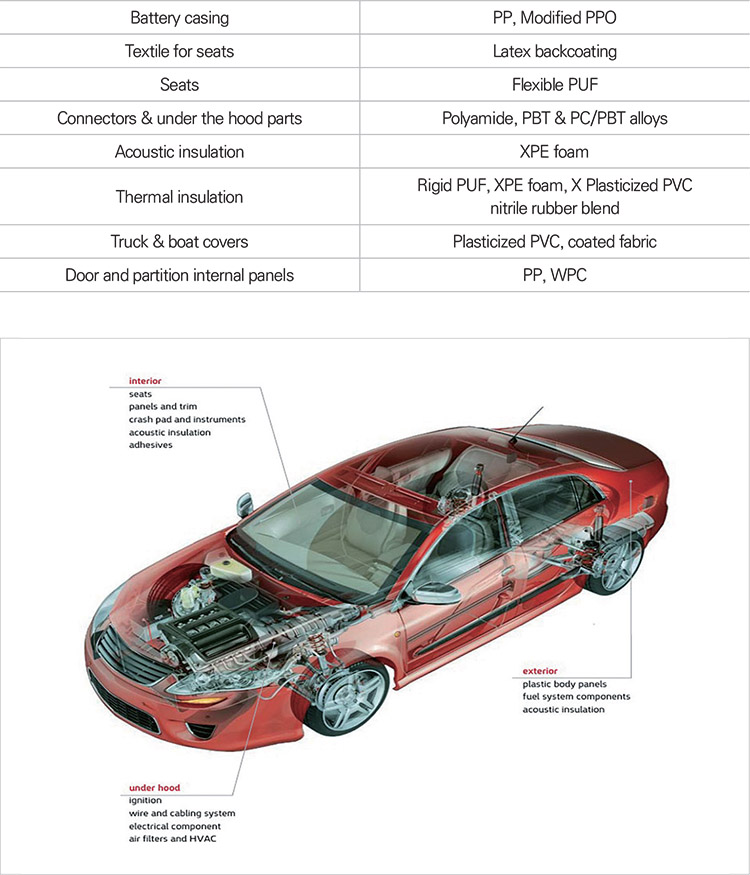
Ⅶ. 결론
플라스틱의 용도가 건축, 전기·전자, 자동차, 항공, 선박, 케이블 등 다양한 산업 분야에서 광범위하게 확대됨에 따라 화재 안전 규제의 증가와 함께 난연제의 수요가 지속적으로 증대되고 있다. 최근에는 높은 난연성과 환경에 적합한 재료의 개발이 요구되고 있는 상황이다.
난연성과 전기적 특성, 내열성, 기계적 물성, 성형 가공성 등의 밸런스가 우수한 난연재료의 개발이 요구되고 있다. 환경적 측면에서는 특정 난연제의 경우 사용이 엄격히 규제되는 등 EU를 비롯한 미국에서는 화학 물질들에 대한 사용등록, 평가, 인가 제한 의무 등에 대한 관리가 강화되고 있다.
비 할로겐, 저 유해 가스, 저 발연화 등에 초점을 두고 새로운 난연제에 대한 연구와 개발이 필요하다. 난연제의 경우에는 안전·생명 문제와 직결되기 때문에 규제가 더 엄격하게 정해져 있다.
난연 규격에 적합하지 못하면 사용 자체가 제한될 수 있으며, 심지어 법적 규제 대상이 된다. 따라서 이러한 세계적 추세와 법적 규제 내용을 잘 파악하여 사전에 면밀히 대비하여야 할 필요가 있다. 한발 더 나아가 리사이클이 가능한 재료 개발에도 역점을 두어야 한다.
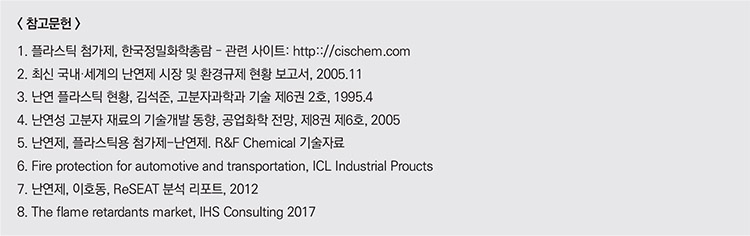
