기술과 솔루션
스마트공장(Smart Factory)을 위한 사출성형 모니터링 데이터 분석 (부제: 사출성형 공정 그래프(Graph)에 대한 분석 및 이해)
최근 사출성형 산업계에서는 극심한 경쟁 구도에 직면하고 있으며, 이로 인하여 지속적인 생산성 향상, 엄격한 품질관리, 인건비 절감 등의 요구에 직면하고 있다. 이러한 산업환경 변화에 대응하기 위하여, 고품질 또는 대량 생산 플라스틱 제품을 중심으로 센서를 이용한 사출성형 모니터링 시스템의 활용이 확대되고 있다. 이 연재 기사에서는 각종 센서와 사출기에서 얻어지는 데이터(그래프)를 이해하고 활용하는 방법에 필요한 기본 지식에 초점을 맞추어 기사를 연재하고자 한다.
RJG 사는 사출성형 교육, 기술 및 리소스 분야에서 세계적인 리더로 인정 받고 있는 회사이며, 사출성형 공정 모니터링에 사용되는 센서와 장비를 생산/공급하고 있다. 본 기사의 게재된 자료들은 RJG 사의 모니터링 시스템(eDart/Copilot)에 기반을 두고 있으며, RJG 사에 Copyright의 모든 권한이 있음을 밝힌다.
자료제공: 이길호 대표이사(씨에이프로(주),
RJG 사 공식 컨설턴트/트레이너)
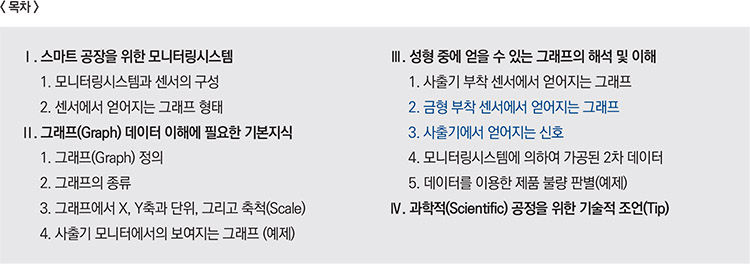
Ⅲ. 성형 중에 얻을 수 있는 그래프의 해석 및 이해
2. 금형 부착 센서에서 얻어지는 그래프
금형 캐비티(Cavity) 내부의 상태를 모니터링하기 위하여 일반적으로 압력 센서와 온도 센서를 사용하며, 기타 광학 속도 센서나 금형 변위 센서 등을 적용하기도 하지만 아직까지는 그리 널리 사용되지 않고 있다.
또한, 온도 센서도 얻을 수 있는 데이터는 매우 한정적이고 간단함으로, 여기에서는 압력 센서에 대한 내용을 중점적으로 다루고자 한다.
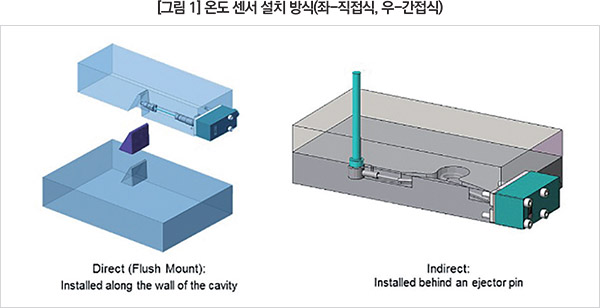
아래의 그림은 압전(Peizo) 센서와 스트레인 게이지(Strain Gage) 센서를 금형 내에 설치하는 방식에 따라 직접식(Direct)과 간접식(Indirect) 분류를 보여준다.
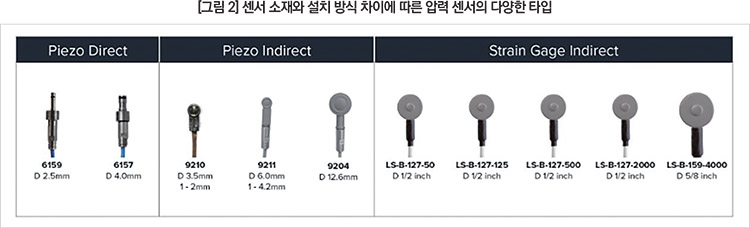
2.1 압력 센서에서 얻어지는 그래프
압력 센서는 유동이 지속적으로 이루어지는 유로(Flow Path) 上이나, 공정 중에 압력이 지속적으로 전달이 가능한 충분히 두꺼운 부분에 설치하여야 하며, 이러한 위치에 설치된 센서는 공정 제어와 모니터링을 위한 유용한 데이터를 얻을 수 있게 도와준다.
복잡한 제품의 경우에는 시뮬레이션을 이용하여 유동 패턴, 유동 거리, 그리고 유동 말단 등의 결과를 검토하여 센서의 위치를 결정하는 것이 바람직하다.
위의 [그림 3]에서 PST와 EOC라는 약어를 현장에서 많이 사용하며, PST는 Post Gate의 약자로 게이트 직후를 의미하며, EOC는 End of Cavity로 유동 말단을 칭한다. PST는 V/P절환과 벨브게이트 제어(Control)에 많이 사용되며, EOC는 미성형, 치수 변화, 싱크 등과 같은 제품의 품질(Qulaity)을 모니터링하는 데에 주로 이용된다. 일반적으로 게이트에서 전체 유동 거리의 20% 이내의 지역을 PST, 유동 거리의 80% 이후의 지역을 EOC로 규정한다.
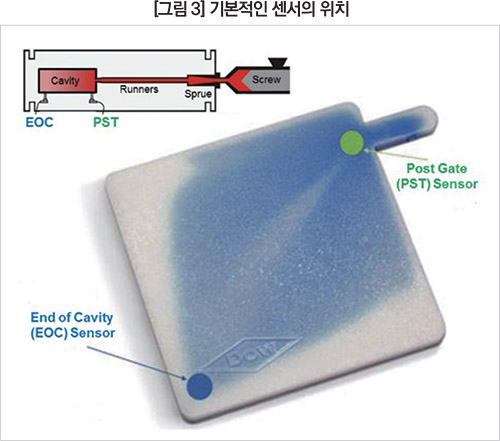
2.1.1 EOC 위치의 압력 센서에서 얻어지는 그래프
일반적으로 EOC 위치는 유동 말단, 즉 V/P절환이 이루어지는 시점 근처임으로 충진 공정에서의 압력이 전달되기 어렵다. 아래 [그림 4]에서와 같이 V/P절환 이후에 유동이 이루어지는 위치에 센서가 위치하면 충진 이후의 충전(Packing)과 보압(Holding) 공정의 압력 변화만을 측정할 수 있다.
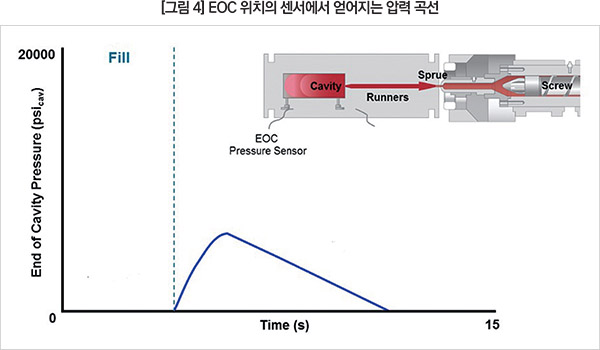
아래 [그림 5]에서와 같이 충진(Filling) 이후에 압력의 상승이 시작되며, 이는 유동이 제품의 끝단에 도달하고, 게이트로부터 전달되는 압력에 의하여 재료의 밀도가 올라가는 충전(Packing) 현상이 발생하게 된다. 일반적으로 사출기에서는 재료의 충진(Filling)과 보압(Holding) 공정으로 분류하여 사출기의 조작변수를 입력하지만, 실제 금형 내에서는 재료의 충진과 보압의 변화 사이에 재료가 압력을 받아 밀도가 상승하는 충전(Packing)이라는 단계가 존재한다.
위의 그래프에서 얻어지는 초기 기울기(Slope), 즉 ‘△압력(Pressure)/△시간(Time)’은 게이트(Gate)를 통과한 사출압력이 제품 끝단에 얼마나 이른 시간에 얼마만큼의 압력을 전달하는가를 나타낸다.
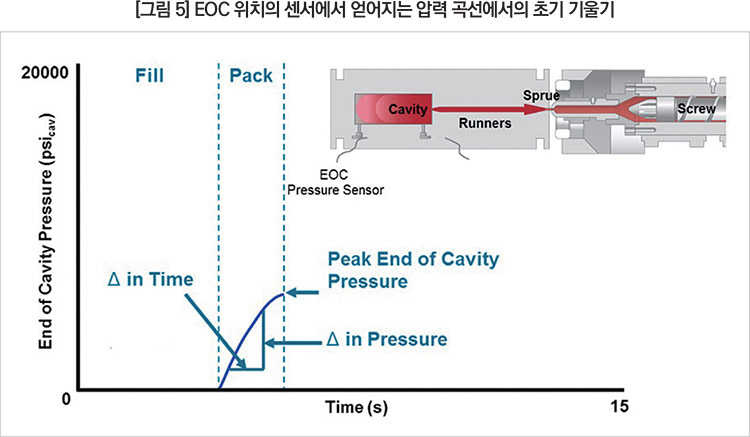
이는 사용하는 수지의 점성(Viscosity)와 사출기의 V/P절환 능력 등에 따라 달라지며, 일반적으로 기울기가 완만한 경우에 센서에서 측정되는 압력의 최고점(Peak Pressure)이 낮아진다.
아래 [그림 6]에서와 같이 충전이 완료된 후의 그래프에서 얻어지는 기울기(Slope), 즉 ‘△압력(Pressure)/△시간(Time)’은 감소(-)하는 형태로 나타나며, 제품 끝단이 고화됨에 따라 내부의 압력이 시간에 따라 얼마나 감소하는지를 보여준다. 일반적으로 이를 냉각률(Cooling Rate)이라고 칭하며, 금형 조건(냉각수 온도, 냉각수 유속, 냉각라인의 설계…)과 재료의 열적 특성에 의하여 달라진다.
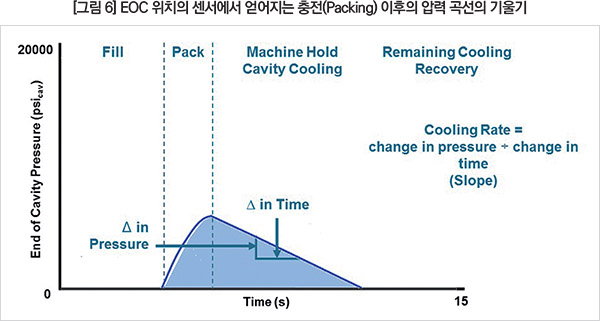
EOC 위치의 센서 그래프에서 얻어지는 정보는 기울기(Slope), 최고점(Peak), 그리고 적분(Integral)으로 분류할 수 있으며, 이를 이용하여 다음과 같은 정보 들을 산출할 수 있다.
1. 기울기(Slope) – (+)기울기는 충전속도, (-)기울기는 냉각속도
2. 최고점(Peak) – 제품 끝단에서의 최고 작용 압력
3. 적분(Integral) – 전 공정 중에 제품 끝단에 작용한 압력의 총 이력 또는 양
위의 값들을 이용하여 제품 끝단의 상태를 유추할 수 있으며, 사용하는 재료의 종류에 따라 각각의 값들의 중요도가 변화한다. 예를 들어 비결정성(Amorphous) 재료의 경우에 압력에 관련된 최고점(Peak)이나 적분(Integral)이 더 중요하고, 반결정성(Semi-crystalline) 재료는 냉각속도(냉각률) 값의 변화에 조금 더 집중하여야 한다.
EOC 위치에서의 압력 값이 Zero이거나 매우 낮은 경우에는 제품에 미성형(Short-Shot)이 발생할 확률이 매우 높으며, 이러한 현상을 이용하여 대량 생산하는 소형 부품이나 두께의 변화가 심한 제품, 사출기의 안정성이 낮은 경우, 그리고 재료의 일관성이 낮은 경우에 EOC 위치의 센서를 불량품 선별에 이용하기도 한다.
2.1.2 PST 위치의 압력 센서에서 얻어지는 그래프
PST 위치는 유동이 캐비티로 유입되는 게이트 부근을 이야기하며, 사출기의 영향을 가장 많이 받는 지역으로 V/P절환과 같은 사출기의 변화를 포함하는 압력 곡선을 보여준다.
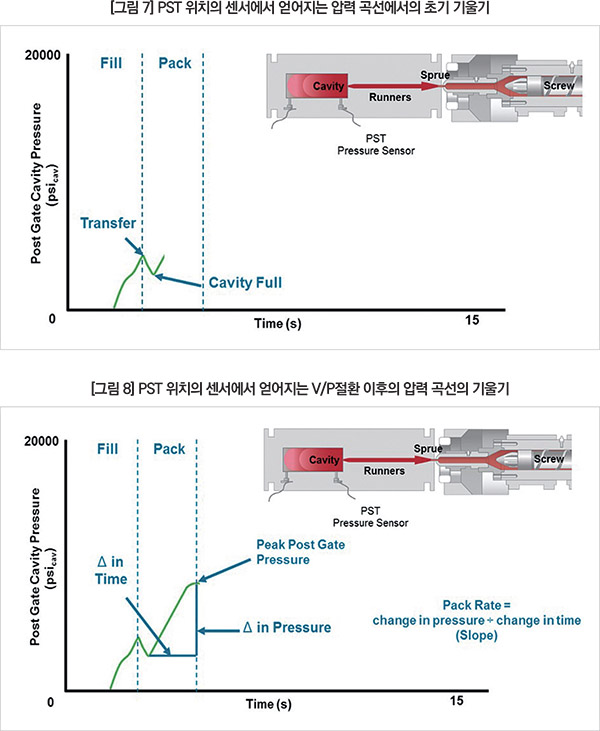
[그림 7]에서와 같이 V/P절환을 포함하는 충진(Filling), 충전(Packing) 공정의 압력 변화를 보여주며, 절환(Transfer) 시간은 사출기의 절환 시점과 일치한다. 그 후에 사출기가 속도 제어에서 압력 제어로 변환되는 시점에 금형의 내압은 순간적으로 감소하게 되며, 이때 압력이 가장 낮은 지점이 캐비티가 완전 충진(Filling)되는 시점을 나타낸다.
[그림 8]에서와 같이 캐비티가 완전히 충진(Filling)되는 시점을 지나면, 압력은 다시 상승하여, 캐비티의 내부에 압력이 일정 수준으로 상승하게 된다. 이때 상승되는 압력의 값은 사출기의 보압(Holding) 압력 조건에 의하여 결정되며, 기울기(Slope)는 사출기의 압력 응답성(Pressure Response)과 재료의 점성(Viscosity)에 크게 영향을 받는다.
아래 [그림 9]에서와 같이 충전이 완료된 후의 그래프에서 얻어지는 기울기(Slope), 즉 ‘△압력(Pressure)/△시간(Time)’은 감소(-)하는 형태로 나타나며, 게이트 부근이 고화됨에 따라 내부의 압력이 시간에 따라 얼마나 감소하는지를 보여준다.
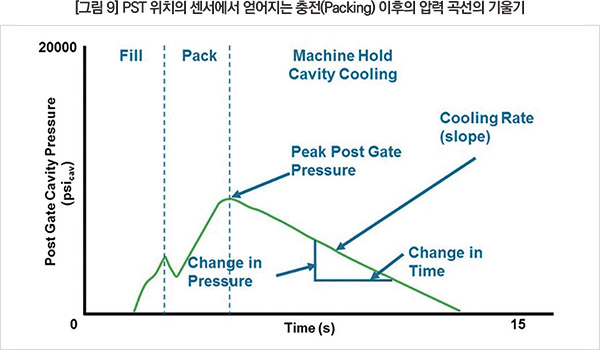
PST 위치의 센서 그래프에서 얻어지는 정보는 EOC 위치의 센서와 거의 유사하며 기울기(Slope), 최고점(Peak), 그리고 적분(Integral)으로 분류할 수 있으며, 다만 차이점은 압력 상승 시기에 2번의 기울기가 나타난다는 점이다.
1. 1차 기울기(1st Slope) – (+)기울기이며, 충진(Cavity Filling) 속도
2. 2차 기울기(2nd Slope) – (+)기울기이며, 충전(Packing) 속도
3. 3차 기울기(3rd Slope) - (-)기울기이며, 냉각(Cooling) 속도
4. 최고점(Peak) – 게이트 부근에 작용하는 최고 압력
5. 적분(Integral) – 전 공정 중에 게이트 부근에 작용한 압력의 총 이력 또는 양
[그림 10]은 융용 재료가 런너와 게이트를 통과할 때에 유동성(점도) 변동을 심하게 유발하는 설계로 제작되었을 때에 캐비티의 압력 변동이 심각해 짐을 보여주며, 이외에도 사출기 불안정이나 재료의 물성 변화 등이 이러한 변동을 유발하는 요인으로 작용하기도 한다.
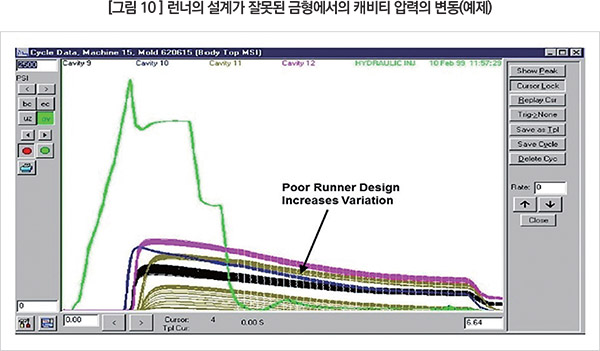
센서에서 얻어지는 값들을 통하여 게이트 내의 상태를 유추할 수 있으며, 이를 이용하여 캐비티 내에 동일한 압력 분포를 매 사이클마다 얻을 수 있도록 제어할 수 있다. 예를 들어 PST 위치의 압력 센서에서 측정되는 값을 기준으로 V/P절환하는 사출 방법을 사용하면, 양산에서 계속적으로 동일한 품질의 제품을 생산하기 쉬워진다.
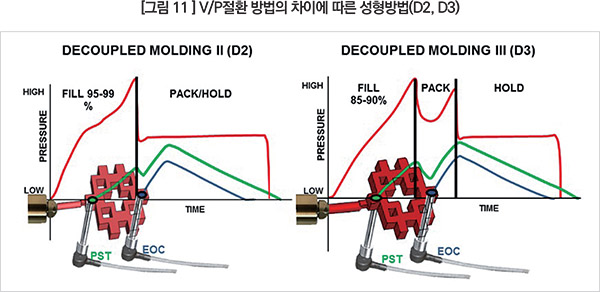
위의 [그림 11]에서와 같이 사출기의 위치를 기준으로 V/P절환을 하는 일반적인 방법을 Decoupled Molding II(D2)라고 하고, PST 위치에 설치된 내압 센서의 압력 기준값을 이용하여 V/P절환을 하는 방법을 Decoupled Molding III(D3)라고 한다.
Decoupled Molding II(D2) 성형방법은 사출기의 위치를 기준으로 V/P절환을 수행함으로, 금형의 특성이나 재료의 변화를 고려하지 않으며, 이러한 이유로 캐비티 내에 동일한 압력 분포를 매 사이클마다 유지하는 데에 어려움이 있다. (그림 12)
[그림 13]에서 보는 바와 같이 D2 방법에 비하여 D3 방법의 가장 큰 이점은 여러 가지 변동에도 캐비티 내에 동일한 압력 분포를 유지할 수 있음이며, 최종적으로는 제품 품질의 동일성을 유지할 수 있는 데에 있다.
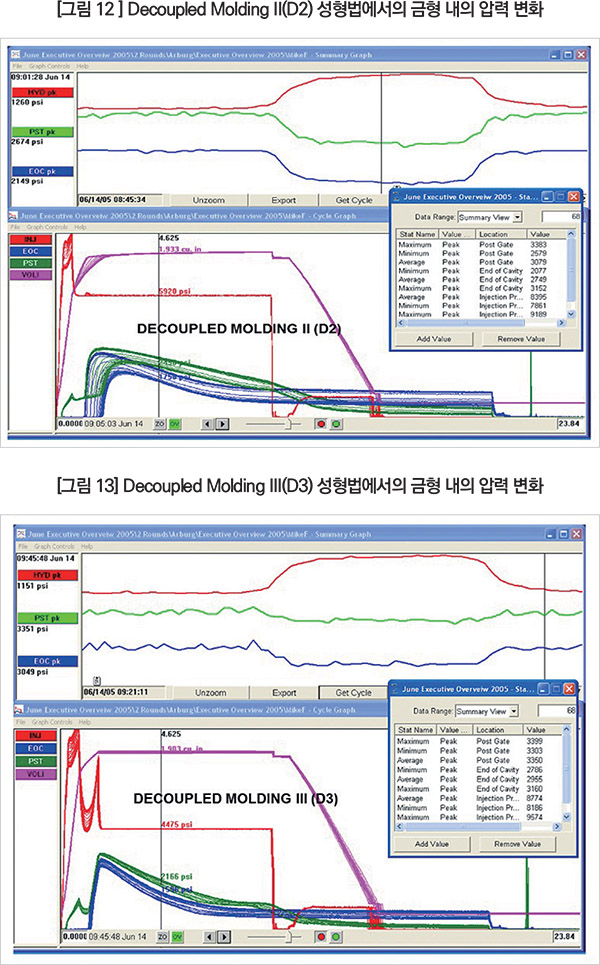
2.2 온도 센서에서 얻어지는 그래프
온도 센서는 캐비티 벽면의 온도 변화를 측정하며, 실제 캐비티 내에 유입되는 용융 재료와는 측정되는 온도에 차이가 존재한다. 이는 용융 재료가 온도 센서의 상단과 접촉하지만, 온도 센서 측면이 금형과 접촉하고 있어 금형으로 빠르게 열을 방출되기 때문이다.
온도 센서를 이용하면 금형과 용융 재료의 온도 변화를 감시할 수 있으며, 유동이 센서를 통과하는 시점을 측정할 수 있다. 이를 이용하여 순차(Sequence)성형을 이루도록 밸브(Valve) 게이트의 열리는 시점을 자동으로 제어한다.
[그림 14]에서 점선은 기준이 되는 템플릿(Template) 곡선이며, 실선은 변화된 조건이나 환경에 의한 현재 측정한 곡선이다. 온도가 하강하면 캐비티의 압력이 감소하며, PST 지점보다 EOC 지점에서의 압력 감소가 더욱 심함을 볼 수 있다.
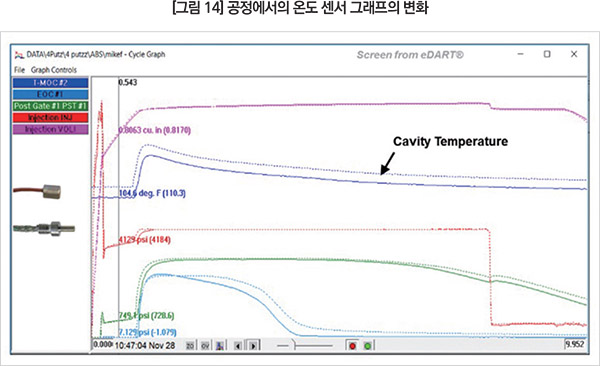
2.3 금형 변위 센서에서 얻어지는 그래프
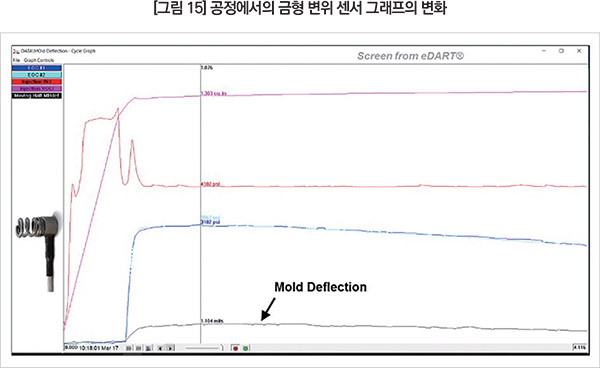
용융 재료가 유입되면서 캐비티 내의 압력이 증가하고, 이때 금형이 벌어지는 것을 억제하기 위하여 사출기에서 노즐의 반대편에서 형체력(Clamp Force)를 금형에 가하게 된다. [그림 15]와 같이 일반적으로 금형은 충진과 보압 공정 중에 플래쉬(Flash or Burr)가 발생하지 않을 정도로 미세하게 벌어지게 되며, 금형 변위 센서는 변위의 변화를 측정하여 캐비티의 형상(두께) 변화, 형체력의 만족 여부, 그리고 금형의 이상 유무 등을 감시할 수 있게 도움을 준다.
[그림 16]은 금형 변위 센서의 실물과 설치하는 방법을 보여준다. 이 센서는 압력 센서와 거의 유사한 기능을 가지고 있으며, 센서의 상단에 설계된 스프링 상수(Spring Constant)를 가지는 스프링을 이용하여 측정된 힘(Force)를 변위로 환산하여 모니터링 시스템에 그 값을 나타낸다. 금형의 변위가 증가하면 캐비티 내의 용융 재료가 고화되는 과정에서 금형의 복원력으로 인하여 과도한 압력이 재료에 작용하게 되며, 이는 이상 변형과 같은 예측 불가능한 문제를 유발할 수도 있다.
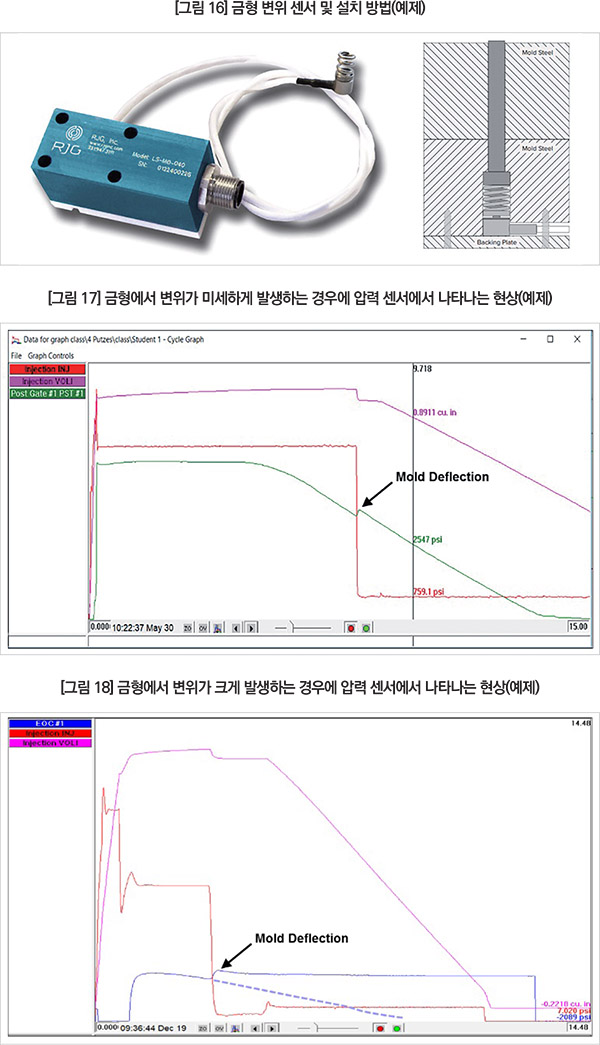
위의 [그림 17]은 금형의 변위가 미세하게 발생하여 캐비티의 형상을 변화시키는 경우에 나타나는 압력 센서의 반응을 보여주는 그래프이며, 사출기에서 보압(Holding)의 작용이 멈춘 후에 미세하게 압력이 캐비티에 추가됨을 볼 수 있다.
[그림 18]은 금형의 변위가 심하게 발생하여 캐비티의 형상을 크게 변화시키는 경우에 나타나는 압력 센서의 반응을 보여주는 그래프이다. 사출기에서 보압(Holding)의 작용이 멈춘 후, 점선과 같이 수축에 의한 압력의 감소가 일어나야 하지만 냉각이 진행됨에 따라 수축이 감소하지 않고 계속 지속되는 현상이 발생한다.
캐비티에 설치된 압력 센서로도 금형의 변위가 발생하는 현상을 감시할 수 있으나, 정량적으로 기준을 선정하기 위해서는 금형 변위 센서가 필요하다. 금형 변위 변화 추이를 장시간 모니터링하는 경우에 금형 노후화 경고나 유지보수에 유익한 데이터를 확보할 수도 있다.
3. 사출기에서 얻어지는 신호
대부분 사출기는 외부로 신호를 출력하는 단자를 제공하고 있으며, 이러한 신호는 밸브(Valve) 게이트, 취출 로봇 등을 제어하는 데에 사용된다. 모니터링 시스템에서도 압력이나 온도 센서에서 얻어지는 곡선 데이터를 각 공정(충진⇨보압⇨계량/냉각⇨금형 열림⇨취출⇨금형 닫힘)별로 세분화하고, 사출기 동작과 데이터를 연계하기 위하여 외부의 신호를 선택적으로 받아들일 필요가 있다.
모니터링 시스템에서 필요로 하는 신호는 0V/24V 디지털 신호이며, 아래의 [그림 19]에서와 같은 모듈을 이용하여 사출기와 모니터링 시스템을 연결한다. 2개의 케이블 연결 단자는 사출기에서 전달되는 신호를 모듈로 입력하는 곳이며, 다른 하나는 모니터링 시스템으로 신호를 송신하는 기능을 한다.
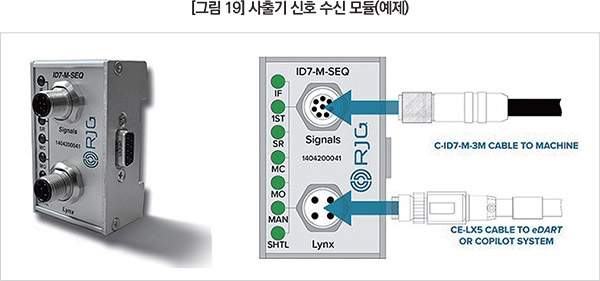
일반적으로 모니터링 시스템에서 필요한 사출기의 신호는 아래와 같으며, 24V 공통(Common) 선을 사출기에 연결하여야 한다. 사출기의 단자에 케이블을 연결할 때에는 사출기 기술자의 도움과 조언을 받아 진행하는 것이 바람직하다.
1. IF(Injection Forward): 사출기 스크류가 전진 신호할 때에 내보내는 24V 신호
2. 1ST(Fill): 사출기가 충진 공정을 수행할 때에 내보내는 24V 신호
3. SR(Screw Run): 스크류가 계량을 위하여 회전할 때에 내보내는 24V 신호
4. MC(Mold Clamp): 금형이 닫히고 형체력이 작용할 때에 내보내는 24V 신호
5. MO(Mold Open): 금형이 열려 있을 때에 내보내는 24V 신호
6. MAN(Manual): 사출기가 수동(Manual)모드로 있을 때에 내보내는 24V 신호
7. SHTL(Shuttle): 셔틀(Shuttle) 성형의 회전 테이블의 위치변화에 내보내는 24V 신호
그 외에 전동식 사출기인 경우에 사출압과 스크류의 위치를 아날로그 신호로 출력하여 모니터링 시스템에서 수신할 수 있으며, 적절한 모듈을 선정하여 각 위치의 배럴(Barrel) 온도나 노즐 온도도 출력단자에서 직접 수신할 수 있다.
사출기 신호는 필수 요건은 아니지만 더욱 효율적으로 각 공정 데이터를 세분화하여 더욱 정확한 2차 계산 결과를 도출하는 데에 사용되며, 또한 사용자가 그래프를 보다 쉽게 이해하는 데에도 도움을 준다.
사출기 신호를 연결하지 않는 경우에, 아래 [그림 20]과 같은 금형 열림과 닫힘을 알 수 있는 형 개폐 스위치(Proximity Switch)를 이용한다.
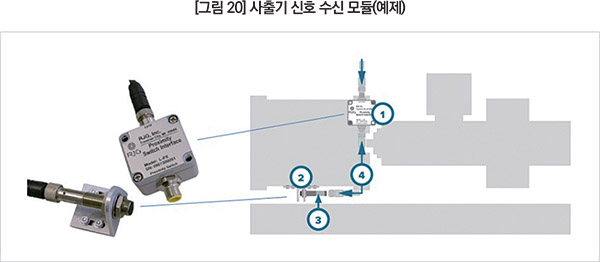
본문에서 사용된 그림이나 표 등은 RJG 사 또는 씨에이프로(주)와 사전 협의 없이
무단으로 사용될 수 없음을 양지하여 주시기 바랍니다.
기술된 내용에 대하여 더욱 자세한 내용을 원하시면, www.rjginc.com의
‘Resource Center’를 방문하시거나, 씨에이프로(주)(대표전화: 02-2081-1870)로
문의 주시기 바랍니다.
다음호에 계속…