기술과 솔루션
나노 셀룰로오스의 표면 개질 및 최근 응용 동향
나노 셀룰로오스의 표면 개질 및 최근 응용 동향
자료제공: 소재종합솔루션센터(www.matcenter.org), 화학소재정보은행(www.cmib.org) 지식정보 심층보고서
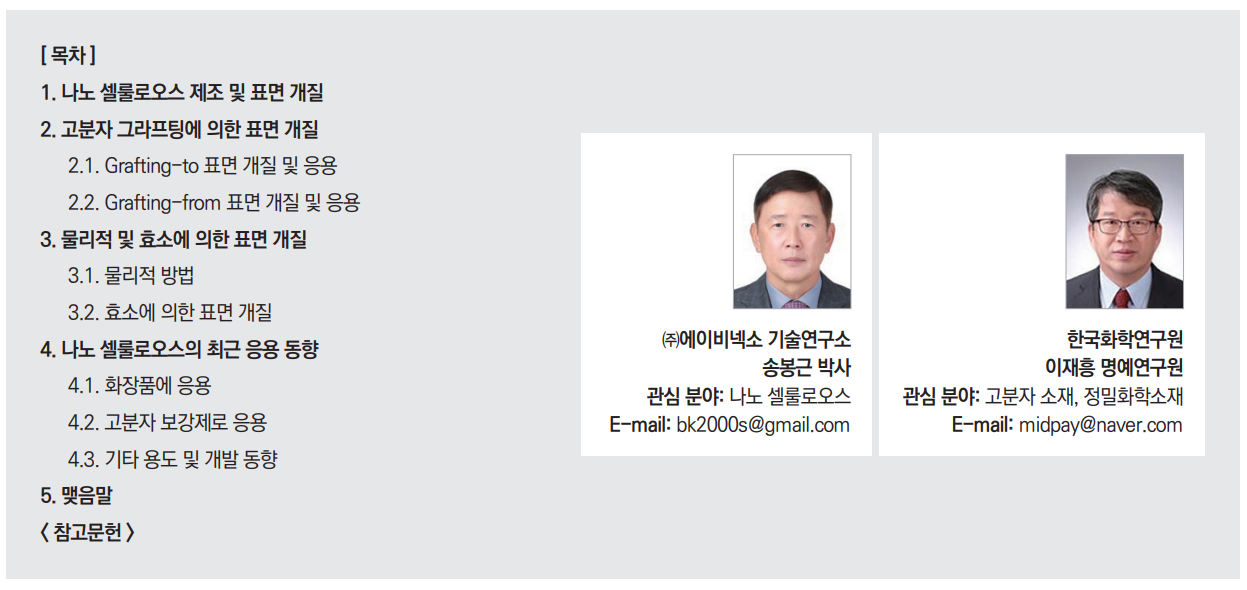
1. 나노 셀룰로오스의 제조 및 표면 개질
나무, 풀, 곡물, 해초 같은 바이오매스를 원료로 하는 유기 소재는 원유에서 출발하는 합성 유기 소재보다 탄소발자국(footprint)을 줄일 수 있고, 대부분은 사용 후 자연에서 분해가 일어나는 생분해 특성이 있어 최근 산업계, 학계에서 친환경소재로 많은 관심을 두고 있는 소재이다. 바이오매스 중에서 가장 많은 물질이 polysaccharide인 starch(녹말)와 cellulose(셀룰로오 스)이다.
둘 다 생분해 소재로 사용되고 있으나 특성, 가공성 등이 우수한 셀룰로오스가 좀 더 고성능 소재로 쓰이고 있다. 셀룰로오스는 주로 목본 및 초본류의 식물자원에서 얻을 수 있으며, 이외에도 조류(algae), 균류(fungi), 박테리아(bacteria) 등을 통해서도 각기 다른 특성의 셀룰로오스가 얻어진다. 목본계의 경우 셀룰로오스 함량이 전체 구성 성분의 약 40~55% 정 도를 차지하고 있으며, 펄핑공정을 통하여 일정량의 리그닌과 헤미셀룰로오스를 제거함으로써 약 80% 이상의 셀룰로오스로 구성된 펄프 섬유 형태로 얻을 수 있다.
최근에 셀룰로오스로부터 직경이 수~수십 ㎚, 길이가 수십~수백 ㎚이고 강도가 매우 우수한 셀룰로오스 나노파이버(CNF), 셀룰로오스 나노크리스탈(CNC) 등을 제조하는 다양한 기술이 개발되고 있다. 제조된 CNF, CNC 등의 나노 셀룰로오스(nano cellulose, NC) 입자를 플라스틱, 고무 등과 용융 컴파운딩 혹은 용액, 에멀젼 상태에서 복합화하여 고분자의 강도, 내열성, 배 리어성 등을 강화하여 활용하는 연구가 활발히 이루어지고 있다.
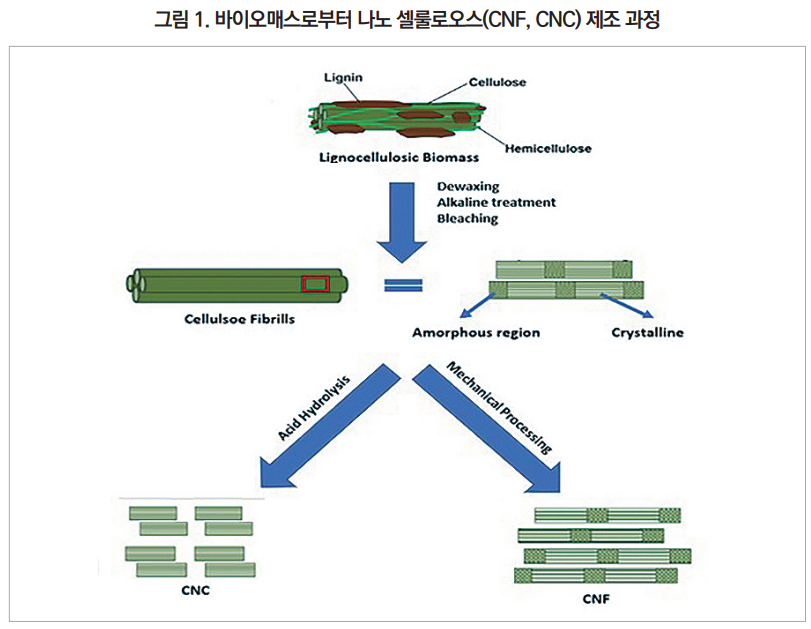
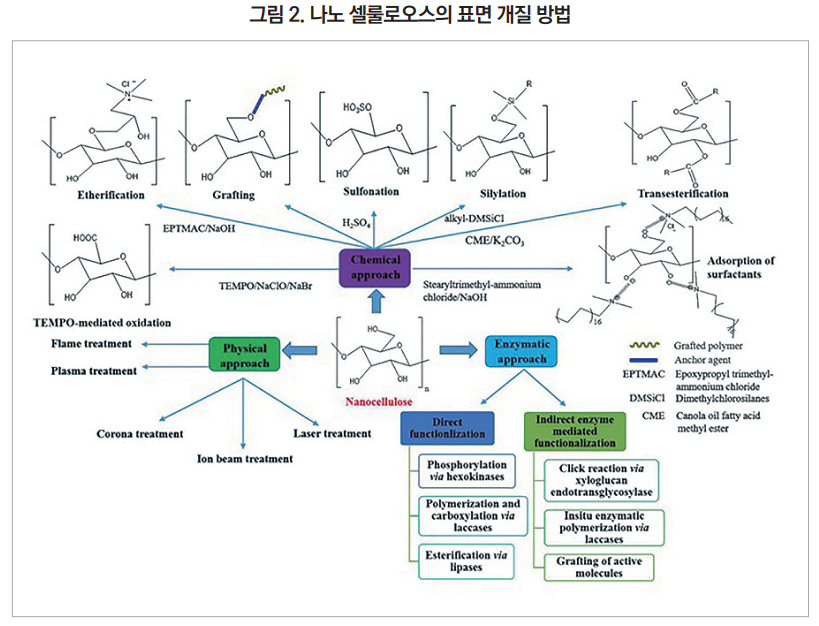
NC의 개요, 제조 방법, 응용에 대하여 화학소재정보은행의 심층보고서 여러 편에 잘 기술되어 있으며, 본 심층 보고서는 2023년 11월 발표된 심층 보고서 “나노 셀룰로오스 제조 및 표면 개질”에 이어 작성된 내용이다. NC와 고분자의 혼합 시 NC의 표면 특성이 분산성, 접착성에 직접 영향을 주고 결과적으로 복합체의 기계적, 광학, 전기적, 배리어 등의 특성을 좌우한다. 따라서 NC의 표면 특성을 화학적, 물리적으로 제어하는 연구가 이루어지고 있다.
저분자량 물질과 반응시켜 NC의 표면에 친수성, 소수성을 부여하는 방법에 대하여 전편에 보고하였으며, 본 보고서에서는 고분자, 물리적 방법, 효소 등을 이용하여 표면을 제어하는 방법과 NC/고분자 복합체의 최근 응용 동향에 관하여 기술하였다. 그림 1에 목재로부터 CNF, CNC의 제조 방법을 간략하게 나타내었다. 그림 2에는 화학, 물리, 효소 등의 방법을 이용하여 나노 셀룰로오스의 표면을 개질하는 방법을 정리하였다
2. 고분자 그라프팅에 의한 표면 개질
고분자 그라프팅 반응에 의한 나노 셀룰로오스의 표면 개질은 나노 셀룰로오스/고분자 복합소재의 물리적, 화학적 특성 향 상을 위한 대표적 방법이다. NC 표면에 있는 수산기(-OH)는 표면 반응의 화학적 연결고리 역할을 하여 작은 유기 분자를 NC에 도입하거나 거대분자인 고분자를 표면에 성장시킬 수 있다. 고분자를 이용한 표면 그라프팅은 도입된 고분자에 따라 계면 특성이 조절될 수 있으므로 극성 용매뿐 아니라 비극성 용매에서도 안정적인 현탁액을 만들 수 있다.
고분자 그라프팅은 그림 3에 나타낸 바와 같이 세 가지 방식의 경로로 분류할 수 있다. 즉 “grafting-to”, “grafting-from”, 그리고 “grafting-through”로 분류할 수 있다. “Grafting-to”법은 말단에 반응기를 갖는 고분자 사슬을 미리 합성하고, 이를 나노 셀룰로오스의 표면 -OH 그룹과 반응시키거나 커플링제를 통해 결합시킨다. 이 접근 방식은 그라프트된 고분자의 특성을 잘 제어할 수 있지만, 입체 장애로 인해 높은 그라프트 밀도를 얻기가 어려운 단점이 있다.
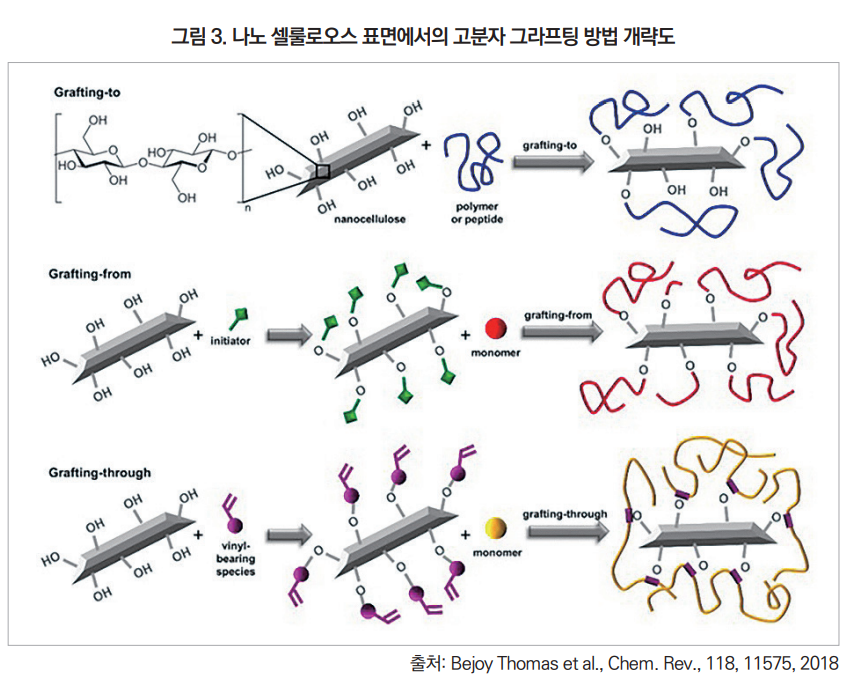
“Grafting-from”법은 나노 셀룰로오스 표면을 개시제(initiator)로 기능화(활성화)시키고, 활성화된 표면에서 단량체가 직접 중합되어 성장한다. 이 방법을 사용하면 “grafting-to” 방식으로 얻은 것보다 그라프트 밀도가 더 높고 다양한 고분자 그라프트 를 생성할 수 있으나, 생성된 고분자의 특성 분석이 어려울 수 있다. 한편, “Grafting-through”법은 중합 가능한 화합물, 즉 비닐기와 같은 중합 가능 그룹을 셀룰로오스 표면에 미리 도입하고, 이후 개질된 셀룰로오스 표면에서 단량체가 중합 반응을 진행한다.
위의 그라프팅 방법 중 “grafting-from” 법이 가장 효율적인 것으로 알려져 있으며, 이 방법은 셀룰로오스 표면에서 그라프 팅 시에 개환중합(ROP), 라디칼 중합, 원자 이동 라디칼 중합(ATRP) 및 Reversible addition fragmentation chain transfer(RAFT)과 같은 다양한 중합 방식을 적용할 수 있다. 아래에 고분자 그라프팅에 의한 나노 셀룰로오스의 표면 개질에 대한 몇 가지 사례를 기술하였다.
2.1. Grafting-to 표면 개질 및 응용
“Grafting-to”법은 미리 합성된 고분자를 나노 셀룰로오스의 표면에 그라프팅하여 표면 특성을 맞춤화하는 방법이다. 나 노 셀룰로오스 표면에 고분자 그라프팅은 특히 자기조립(self-assemble)을 형성하거나 비극성 용매에서 나노 셀룰로오스의 분산성을 개선하기 위해 많은 관심을 받고 있다.
Kloser와 Gray는 PEO-g-CNC의 입체적 현탁액(steric suspension)을 제조하기 위해 CNC의 수성 현탁액에 에폭시 말 단의 폴리(에틸렌옥사이드)(PEO)를 공유 결합으로 간단하게 그라프팅 하는 방법을 보고하였다. 이 방법에서는 처음에 셀룰 로오스로부터 황산 촉매 가수분해에 의해 CNC가 제조된 다음 황산 에스테르 그룹을 제거하기 위해 수산화나트륨으로 처리 되었다. 강알칼리성 조건에서의 친핵성 반응은 PEO 사슬과 CNC 백본 사이에 공유 결합 에테르 연결을 위해 PEO의 에폭시 고리열림 반응이 진행되었다. 제조된 PEO-g-CNC는 안정적인 콜로이드 현탁액을 형성하였으며 몇 달 후에도 침전이 발생 하지 않았다.
Rosiloet 등은 CNC 표면에 10-undecanoyl chloride를 공유 결합하여 가교 가능한 이중 결합을 포함하는 조밀한 탄화 수소 브러시(m-CNC)를 개발하였다. 이를 이용하여 폴리부타디엔(PBD) 고무 매트릭스 내 m-CNC의 농도가 0~80wt%로 조절된 복합 필름을 UV 광 유도 티올-엔 클릭 반응으로 제조하였다. 복합재에서 m-CNC의 중량 분율이 높을 때는 m-CNC 와 고무질 PBD가 서로 삽입된 도메인(intercalated domains)을 형성하여 16MPa의 강도 및 190MPa의 모듈러스를 갖는 복합재가 생성되었다.
낮은 m-CNC 중량 분율(10wt%)을 사용하면 생성된 복합재의 영률과 강도 향상은 무시할 정도로 나 타났다. m-CNC 중량비를 30~35wt%로 증가시키면 복합재의 모듈러스 및 인장 강도에 급격한 변화가 일어났다. 형광 분자도 공유 결합을 통해 나노 셀룰로오스 표면에 그라프팅될 수 있다. 나노 셀룰로오스의 형광 라벨링은 바이오 이 미징 및 센싱 분야에 이용될 수 있다. 즉, 나노 셀룰로오스의 고유 특성을 이용하며 다양한 형광 바이오센서 개발용 플랫폼으 로 활용될 수 있다.
Fanet 등은 낮은 수준의 세포 독성을 갖는 두 가지 다른 형태(구형 및 막대형)의 형광 CNC를 고안하였다. 이 형광 라벨을 만들기 위해 CNC 표면 –OH기는 포름산을 사용하여 Fischer 에스테르화 반응에 의해 카르보닐기로 개질되었다. 이어 암모 니아와의 이민 반응 후, 2차 이미노 그룹과 fluorescein isothiocyanate(FITC)의 isothiocyanate moiety 사이에 공유 결합 이 형성되어 형광성 CNC(FITC-g-CNC)를 생성하였다(그림 4). FITC-g-CNC는 30~36%의 높은 형광 양자 수율을 보여 바이오 이미징 및 라벨링을 위한 다기능 바이오 프로브로 사용할 수 있었다. FITC-g-CNC는 친수성 폴리비닐알코올(PVA) 및 소수성 PLA에서 보강재로서도 분산성이 우수해 형광 기능 외에도 기계적 특성이 향상되었다.
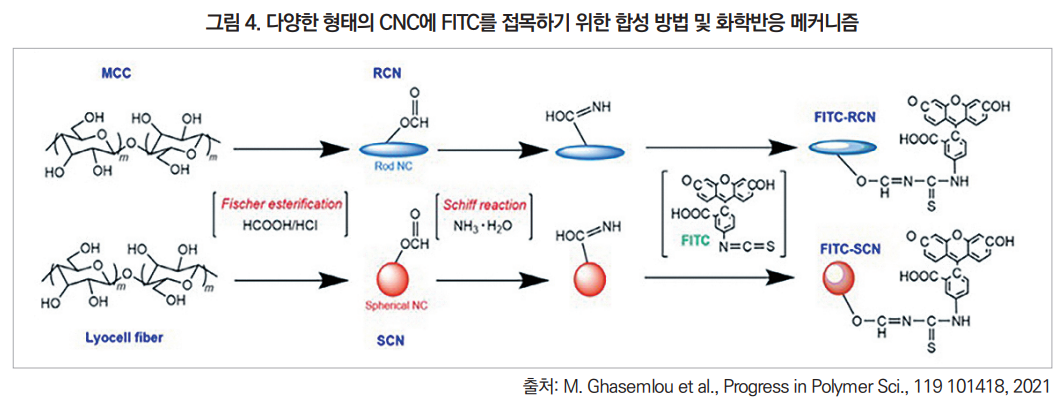
Chuet 등은 2단계 반응으로 형광성 1,8-나프탈이미드 염료(NANI)와 PEG-NH2 브러시를 CNC 표면에 공유 결합으로 도입하여 수중에서 잘 분산되는 우수한 형광 나노프로브를 개발하였다. 이와 같은 개질 방법으로 제조된 TOCNC은 높은 염 용액에서도 우수한 분산성을 가지고 있으며, 550nm에서 황록색 형광을 방출하여 생물의학 연구에 응용될 수 있다.
2.2. Grafting-from 표면 개질 및 응용
2.2.1. 개환중합에 의한 표면 개질
개환중합에 의한 셀룰로오스 표면의 그라프트 중합은 가장 많이 사용하는 grafting-from 법으로 나노 셀룰로오스 표면 에서 에폭사이드, 락톤, 락탐 등의 환(cyclic) 모노머를 그라프팅 중합할 수 있다. 개환중합에서는 촉매인 stannous octoate(Sn(Oct)2)로 활성화된 나노셀룰로오스 표면의 OH- 그룹이 개환중합을 직접 개시하여 일어난다.
Sn(Oct)2는 높은 효 율성과 낮은 독성으로 인해 ROP 공정에서 가장 널리 사용되는 촉매이다. 또한, 이 방법을 사용하면 나노 셀룰로오스 본래 의 구조적 특성을 유지하면서 미세 조절된 사슬 길이와 고밀도 그라프팅 사슬을 갖는 나노 셀룰로오스를 제조할 수 있다. 촉매에 의한 락톤의 개환중합은 폴리에스테르 기반 나노복합체 개발에서 분산 및 상용성 문제를 개선할 수 있다. 락톤 및 락타이드와 같은 환 모노머를 중합하는 표면 개시 개환중합법은 셀룰로오스 섬유에 임의의 말단 그룹을 가지면서 그라 프트 사슬의 밀도를 잘 제어할 수 있다. Hafrén 및 Córdova에 의해 처음 보고된 이후로 많은 연구자가 개환중합 조건을 최적화하려고 시도하였다.
예를 들어, Carlsson 등은 반응 시간이 PCL 그라프트 함량 및 분자량 각 각과 둘 모두에 영향을 주는지를 조사하였다. 개환중합 반응은 단량체, 용매로서 톨루엔, 개시제로서 벤질 알코올 등의 혼합물을 사용하여 90℃에 서 수행되었다. 결과는 CNC 표면에서 반응 시간이 길어지면 PCL 사슬이 대부분 더 크게 성장했지만, 그라프팅된 사슬의 분지도(DS) 값은 3~7% 범위에서 일정하게 유지되어 겉보기에는 개환반응 시간과 무관한 것으로 나타났다. CNF를 보강재로 사용한 복합체 제조를 위해 비극성 매트릭스 고분자 내에 친수성 CNF의 분산성을 향상시키기 위하여 Lönnberget 등은 CNF 표면에 PCL 사슬 길이를 다르게 접목하였다.
그라프팅 밀도뿐만 아니라 그라프팅된 PCL 사슬 길 이는 개환중합 시스템에 포함된 촉매 및 자유 희생 개시제(free sacrificial initiators)의 양을 변화시킴으로써 조정 가능한 것으로 나타났다. PCL 그라프팅 후 유기용매에서 CNF의 분산성이 크게 향상되었으며, 가장 긴 PCL 사슬을 가진 PCL-gCNF는 보강 효과가 우수하여 강한 생체 복합재료를 제조할 수 있었다. 또한, 그라프트 고분자의 양은 free initiators 대비 단량체의 비율을 증가시켜 제어할 수 있었다.
2.2.2. SI-ATRP에 의한 표면 개질
원자 전자 라디칼 중합(atom transfer radical polymerization, ATRP)은 전이 금속 콤플렉스를 촉매로, 알킬할라이드 (R-X)를 개시제로 사용하여 개시 라디칼을 생성하고, 여기에 단량체가 중합하여 분자량 분포가 좁은 고분자를 만드는 방법 이다. 촉매에 있는 전이 금속은 Cu, Fe, Ru, Ni 등이 사용되며, 이온중합과 달리 아미노, 에폭시, 하이드록시, 비닐 그룹 같 은 단량체 기능기에 중합이 큰 영향을 받지 않으며, 저가의 Cu를 사용하는 이점이 있다.
표면 개시 원자 전달 라디칼 중합(surface initiated atom transfer radical polymerization, SI-ATRP)은 개환중합과 함께 가장 일반적인 grafting-from 법으로 나노 셀룰로오스 표면에 고분자 사슬을 성장시킬 수 있다. 또한, SI-ATRP 및 단일 전자 전달 리빙 라디칼 중합(single electron transfer living radical; SET-LR)과 같은 리빙 라디칼 중합은 나노 셀룰로오 스 표면에 고분자 그라프팅에 사용할 수 있다.
구리 매개 SI-ATRP는 고분자 브러시로써 다양한 단량체 중합을 통해 나노 셀룰로오스의 표면을 제어할 수 있다. 일반적 으로 구리 매개 SI-ATRP는 2단계 반응으로 진행되며, 반응은 습식 화학반응 또는 화학 기상 증착을 통해 나노 셀룰로오스 의 OH- 또는 -COOH 그룹에 브롬화 사이트를 형성하는 것으로 시작된다. 그다음 공정은 중합을 유도하기 위해 거대분자 프라이머 역할을 하는 브롬화된 나노 셀룰로오스와 단량체의 추가 반응으로 진행된다. SI-ATRP는 나노 셀룰로오스 표면에서 높은 그라프팅 밀도, 제어된 고분자 사슬 길이 및 낮은 분산성을 가진 고분자를 합 성하는 데 널리 사용되고 있다.
SI-ATRP를 통한 그라프팅은 나노복합체의 빌딩 블록부터 반응성 나노물질 제조에 이르기 까지 가능하다. 예를 들어, Le Gars 등은 SI-ATRP를 통해 CNC 표면에 다양한 길이로 그라프팅된 폴리(글리시딜 메타크릴 레이트)(PGMA) 브러시를 제조하였다. 먼저, CNC는 ATRP 반응에서 일반적으로 사용되는 개시제인 α-bromoisobutyryl bromide(BIBBR)로 브롬화 시키고, 이어서 브롬화된 개시제 사이트(BIB-CNC)로부터 원하는 모노머인 글리시딜 메타크릴 레이트(GMA)를 성장시켰다.
생성된 PGMA 체인은 1시간 후에 CNC 표면의 약 40%를 덮었으며, 24시간 후에는 PGMA가 전체 중량의 80%를 차지하였다. SI-ATRP 또는 전자 전달로 재생된 표면 개시 활성화제(SI-ARGET)를 통해 희생 개시제로서 BIBBR의 존재 하에 CNC 표면에 소수성 폴리스티렌(PS) 및 친수성 폴리(4-비닐피리딘)(P4VP)의 그라프팅도 연구되었다. SI-ARGET 시스템이 그라 프팅에 기여함을 알 수 있었고, 고전적인 SI-ATRP 방법에 비해 더 긴 사슬을 얻을 수 있었지만, 그라프팅 밀도는 낮았다.
또 한, SI-ATRP에서는 BIB-CNC의 거의 모든 Br 개시 부위가 반응하는 반면, SI-ARGET 시스템은 스티렌 또는 4-비닐피리 딘 여부에 무관하게 6~7%의 Br 부위만이 개시하는 것이 관찰되었다. CNC보다 더 복잡하고 부분적으로 무정형 구조를 가진 CNF의 SI-ATRP는 다른 양상을 나타내었다. Moritset 등은 두 가지 경로를 통해 제어된 SI-ATRP를 사용하여 CNF 표면에 폴리(n-부틸 아크릴레이트)(PnBA) 및 폴리(2-(디메틸 아미노) 에틸 메타크릴레이트)(PDMAEMA) 브러시의 그라프트 중합 가능성을 연구하였다.
첫 번째 경로에서는 BIBBR 개시제를 CNF 에어로겔에 화학 기상 증착(1단계)한 다음 DMF에서 용액 에스테르화(2단계) 를 포함하는 2단계 에스테르화 공정을 기반으로 높은 수준의 브롬화(높은 개시제 밀도)를 사용하였다. 두 번째 경로는 물에 서 DMSO로의 점진적인 용매 교환을 기반으로 한 낮은 수준의 브롬화(낮은 개시제 밀도)를 사용하였으며, 이어서 용액 에 스테르화를 진행하였다. 브롬화 정도가 높은 경우 그라프팅은 CNF 주변에 강하게 서로 얽힌 고분자 브러시를 형성했지만, CNF 사슬의 붕괴가 관찰되었다.
반면, 낮은 수준의 브롬화로 그라프팅을 통해 얻은 것들은 파편화가 적고 CNF의 구조적 무정형이 유지되었다. 이 관찰을 바탕으로 저자들은 DS가 낮은 브롬화를 사용하여 CNF의 예상치 못한 열화를 유발할 수 있는 사이드 체인 브러 시의 형성을 억제할 수 있다고 발표하였다.
2.2.3. RAFT에 의한 표면 개질
RAFT(reversible addition-fragmentation chain transfer polymerization) 중합법은 thiocarbonylthio compound 같은 사슬이동제와 reversible chain transfer 메커니즘을 사용하여 분자량 분포가 좁은 고분자를 만드는 방법이다. RAFT 는 말단 그룹을 쉽게 티올로 환원할 수 있어서 그림 5와 같이 추가로 개질할 수 있는 기능 그룹을 제공할 수 있는 주요 이점 이 있다.
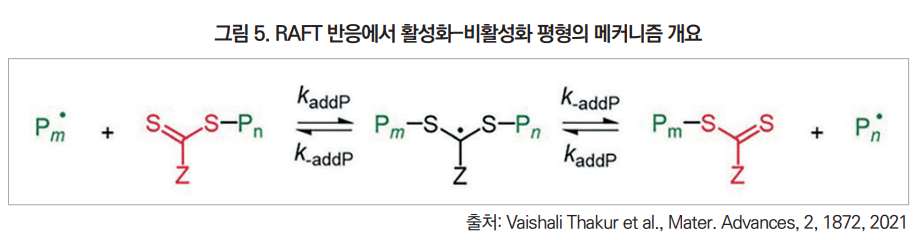
RAFT를 사용하여 셀룰로오스 표면에 폴리(2-(디메틸 아미노)에틸 메타크릴레이트)를 그라프팅한 후 중합체 사슬은 산 성 조건에서 셀룰로오스로부터 절단될 수 있으므로 분리한 중합체의 특성을 분석할 수 있고, 이 특성은 용액에서 단순 중 합한 고분자와 비교할 수 있다. 동일한 절차와 특성 분석을 셀룰로오스에 그라프팅된 폴리스티렌에 적용한 결과, 그라프팅 된 폴리스티렌은 분자량 분포가 좁고 그라프팅 밀도와 적용면적(coverage)이 향상되었다. RAFT 법으로 셀룰로오스 표면에 항균성 고분자를 성장시킬 수 있다.
탄소수가 8, 12 또는 16인 알킬 브로마이드를 사 용하여 셀룰로오스 표면의 폴리(2-(디메틸아미노)에틸 메타크릴레이트) 사슬에 양이온 전하를 부가하였다. 그런 다음 이들 물질을 하이브리드 셀룰로오스 재료가 있는 상태에서 박테리아 용액을 배양하여 대장균에 대한 항균 활성을 테스트하였다. 비변성 및 1-bromooctane quaternized 고분자 그라프팅 셀룰로오스가 가장 높은 항균 활성을 나타내는 것으로 나타났다. 더 긴 알킬 사슬은 셀룰로오스의 소수성을 증가시켰고, 따라서 용액에서 물질과 박테리아 사이의 상호 작용을 감소시켰다.
2.2.4. 자유 라디칼 그라프팅에 의한 표면 개질
자유 라디칼 중합된 온도 감응성 폴리(N-이소프로필 아크릴아미드, p-NIPHM)과 CNC의 혼합 특성 변화를 연구하기 위해 물리적으로 흡착된 셀룰로오스와 공유 결합된 셀룰로오스를 제조하였다. 물리적으로 흡착된 CNC는 친수성이 더 우 수하여 균일하게 최대로 로딩할 수 있었다. 반면에 공유 결합된 CNC는 팽윤 정도가 더 크며 다공성 구조와 같은 특성으로 인해 확산이 잘되는 겔이 생성되었다. CNC/겔 조합은 순수한 폴리아크릴아미드 겔과 비교하여 압축 후 형태 복원성이 우 수하였다(그림 6).
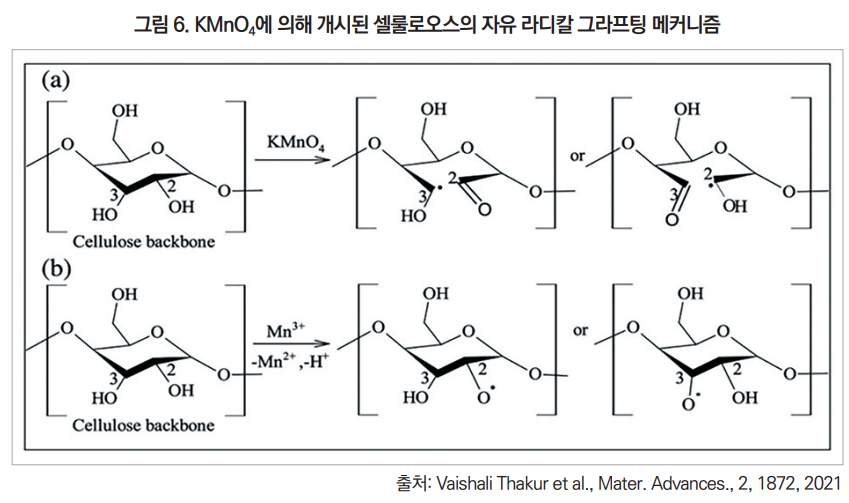
3. 물리적 및 효소에 의한 표면 개질
3.1. 물리적 방법
전기 방전(플라즈마 처리), 초음파 처리, UV 조사 및 표면 세동 방법 등은 대표적 CNC의 물리적 표면 개질 기술이다. 플라 즈마 개질의 주요 특성 중 하나는 벌크 특성을 손상하지 않고 표면 특성을 개질할 수 있으며, 나노 셀룰로오스 표면에 카르복 실기, 카르보닐기 및 산소 함량을 증가시킬 수 있는 점이다.
또한 플라즈마 방전과 함께 초음파 조사와 같은 기술 조합을 사 용하면 나노섬유 코팅의 습윤 및 산화를 더욱 증가시키는 것으로 보고되었다. 바이오 소재 분야에서는 박테리아에서 제조된 나노 셀룰로오스(BNC) 표면을 질소 플라즈마로 개질하여 셀룰로오스 표 면-셀 상호 작용을 촉진하기 위한 연구에서 처리된 표면에서 세포주의 뚜렷한 성장 현상이 나타났다. 한편 산소 플라즈마를 사용하여 BNC 표면을 개질할 경우 형태 구조 및 표면 특성을 변형시켰고, 친수성 막이 형성됨을 관찰하였다.
3.2. 효소에 의한 표면 개질
효소 또한 나노 셀룰로오스 표면을 개질하는 데 사용될 수 있다. Afrin과 Karim은 두 가지 접근법을 사용하였다. (a) 효소 가 나노 셀룰로오스와 직접 접촉하는 직접 개질, (b) 간접적인 효소 매개 개질 방법으로 나노 셀룰로오스를 제조하고, 이를 추가로 기능화하는 것으로 이들 효소 개질법이 화학적 개질 방법에 비해 친환경 개질 방법이라고 결론지었다.
Islam 등은 CNF를 개질하는 데 있어 결정 구조를 보존하기 위해 형태를 손상하지 않고 표면만 개질하는 것이 중요하다고 보고하였다. Hydrolases 및 산화환원효소(oxidoreductases)는 가장 일반적으로 사용되는 두 종류의 효소이다. 글리코시다아제, 프로 테아제 및 리파아제가 자주 사용되는 hydrolases 효소인 반면, 산화환원효소의 경우 락카아제, 티로시나아제 및 퍼옥시다아 제가 주로 사용되는 효소이다. 생의학 응용과 관련하여 효소를 사용, 개질하여 기능화된 나노 셀룰로오스는 화학적 경로로 개질된 제품에 비해 독성을 피할 수 있는 많은 이점을 가지고 있다.
또한, 고밀도의 하이드록실 그룹의 존재를 기반으로 BNC도 개질될 수 있다. Kalhori와 Bagherpour는 공학 응용을 위한 BNC의 활용이 중요하다고 주장하였다. 예를 들어 Akhlaghi 등은 BNC가 시멘트 모르타르의 기계적 특성을 향상하는 것을 관찰하였으며, 시멘트 복합재의 보강재로서 BNC 섬유의 적용성을 확인하였다.
4. 나노 셀룰로오스의 최근 응용 동향
CNF는 자체로 고강도, 고 탄성율, 고 투명성, 고 표면적, 저선열 팽창계수를 가져 고분자 컴파운딩용 필러, 가스 고 배리어 성 등의 용도로 활용이 가능하다. CNF 제조에 널리 사용되는 표면 개질 방법은 1편에 기술한 TEMPO 매개 산화 방법으로 표면에 -COOH 그룹을 갖게 된다. 제조된 초미세 CNF는 나노미터 크기에서 오는 큰 표면적과 수소결합을 쉽게 할 수 있는 – COOH로 인하여 수분산 상태에서 CNF들이 서로 연결된 네트워크 구조, 즉 겔이 만들어진다.
여기에 힘을 가하면 네크워크 구 조가 파괴되어 흐름성이 좋아지고 힘을 그치면 다시 네트워크 구조로 되어 흐름성이 적은 성질, 즉 thixotropic 성질을 갖는다. 이를 이용하여 증점 효과, 기름 분리 방지, 미입자 등의 침강 방지, 흘러내림이 적은 스프레이 제품 등이 개발되고 있다(그림 7).
최근에 CNF가 갖는 고유의 특성을 이용하여 다양한 산업 분야에서 다음과 같은 용도도 활용되고 있다(그림 8). - 분산 안정제: 착색제, 세라믹, 화장품, 섬유, 고무, 플라스틱 등 - 표면 처리제: 전자부품, 섬유, 플라스틱 등 - 지력 증강제: 종일, 펄프 등 - 증점제 및 유화제: 색재, 화장품, 농약, 생활용품, 세라믹 등 - 보강제: 고무/플라스틱 등으로 용도가 개발되고 있다. 이 중에서 대표적인 몇 가지 활용에 관하여 기술한다.
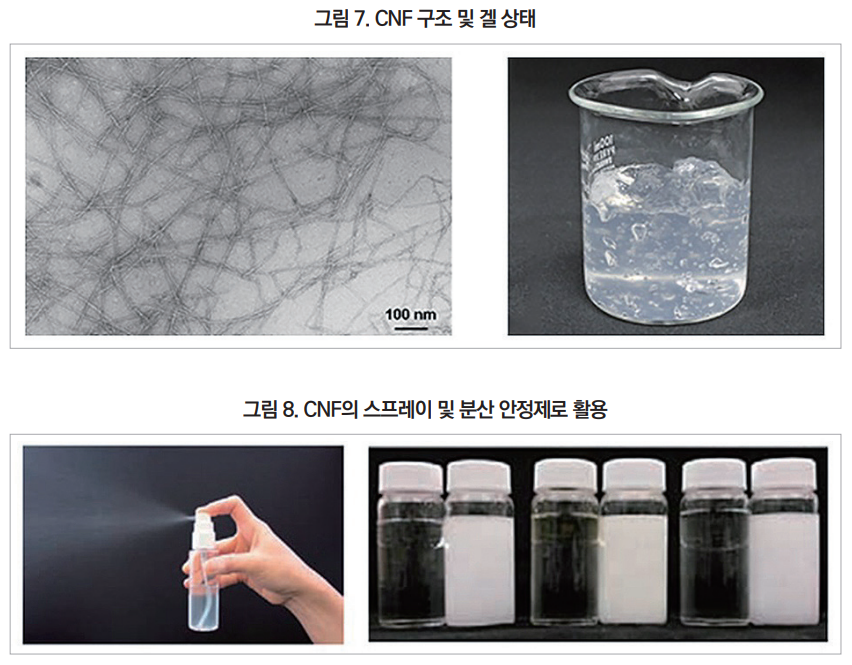
4.1 화장품에 응용
앞서 언급한 바와 같이 바이오매스로부터 제조된 CNF는 친수성, thixotropic성으로부터 유래하는 보습, 증점, 유화 안정, 고체 침강 방지, 안료의 응집억제 등의 기능을 가져 이를 이용하여 기능성 화장품 제조에 널리 응용되고 있다. 일본의 애원제지는 감귤로부터 CNF를 제조하는 기술을 개발하였으며, 제조된 CNF는 증점, 보습 기능이 있어 보습크림, 린스/샴푸 같은 화장품의 원료로 사용되고 있다.
이 제품은 점도를 높이고, 자외선으로부터 피부보호 효과가 있다고 알려져 있다. 애원제지는 감귤의 이미지를 이용하며 식품 첨가에도 활용을 추진하고 있으며, 빵 제조 시 첨가하면 경도가 높아지고 보습과 백색이 양호해져 식감 개선이 기대되고 있다.
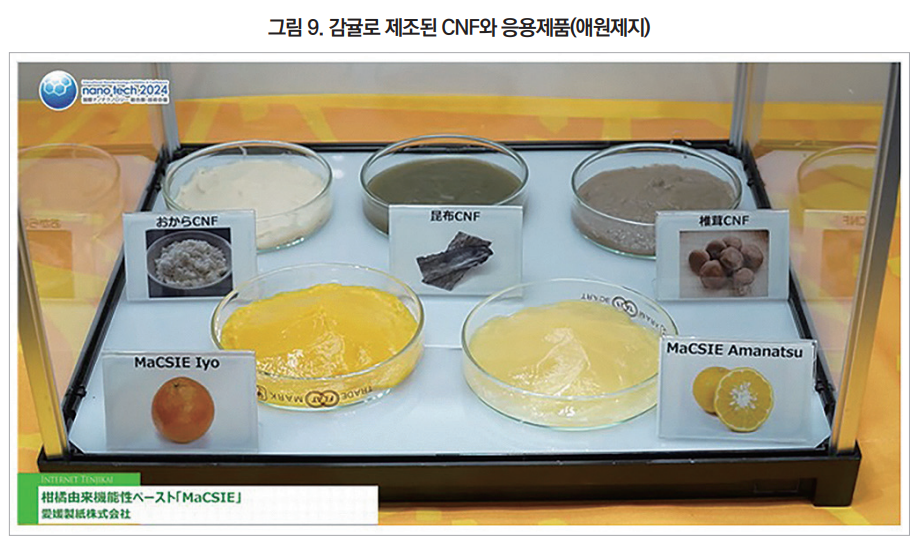
4.2 고분자 보강제로 응용
CNF는 고강도, 저밀도, 환경 친화 특성이 있어 플라스틱, 고무에 보강제로 혼합하여 기계 부품, 자동차 부품 등의 소재로 활용되고 있다. 일본의 아사히케미칼 사는 커지는 환경 대응 이슈에 대응하기 위해 CNF와 폴리아세탈, 나일론수지와의 복합체를 개발하 였다. 아세탈 수지와 CNF의 복합체는 진동 흡수 능력, 차음성, 저 마찰계수, 저 마모성 등의 특성을 나타내 기어 부품, 전기 자동차 모터 소재, 차음재, GREASELESS 베어링 등의 소재로 개발되고 있다(그림 10).
나일론수지와의 복합체는 우수한 내열성, 미끄럼성, 고강도, 저밀도와 reworkability를 가져 소형 부품, 얇은 시트, 경량 부품 등의 소재로 개발되고 있다. 특히 GF 복합체와 비교해보면 5번 재가공 후에도 특성을 유지하는 reworkability성이 우 수하다(그림 11).
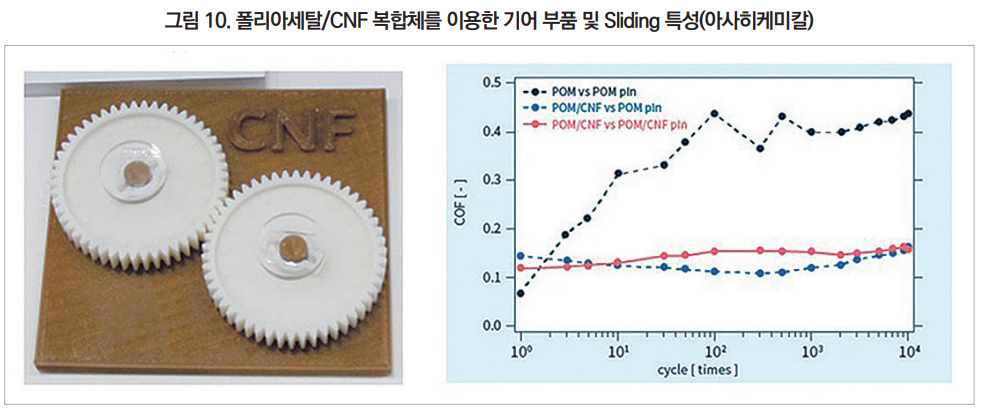
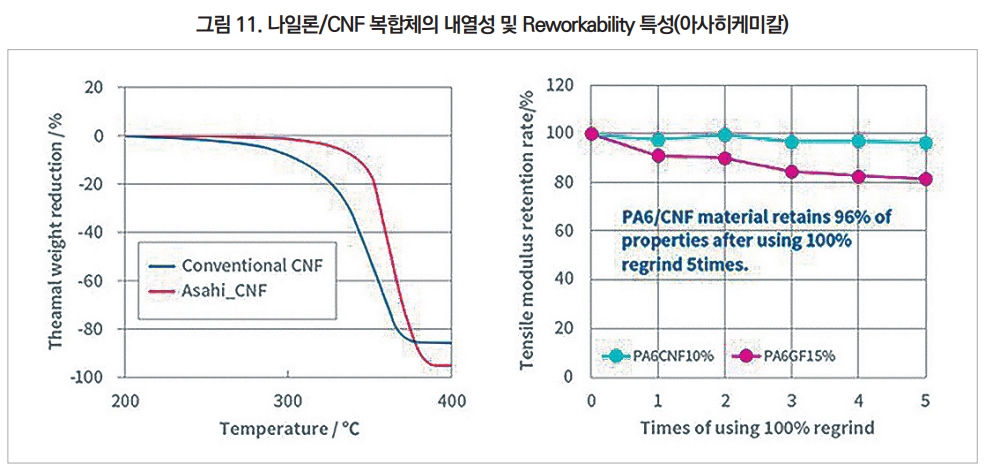
일본제지는 CNF를 천연고무에 균일하게 분산시켜 고강 도와 에너지 로스를 줄인 고무 시트 ‘셀렌피아 엘라스’를 개발하였다. 고무 보강에 가장 많이 사용하는 화석연료 유 래의 카본 블랙(탄소 미립자)보다 소량으로 동등한 강도를 가졌고, 에너지 로스는 약 20% 삭감할 수 있다고 한다(그림 12).
4.3 기타 용도 및 개발 동향
일본의 제일공업제약은 CNF 제조 및 응용에 대한 연구 개발을 활발히 추진하고 있는 기업이다. TEMPO 산화법으 로 제조된 CNF(상품명 “RHEOCRYSTA”)는 섬유 폭 3㎚ 의 초미세 섬유로 투명성, 증점성, 분산성이 우수하여 도 료, 잉크, 세라믹, 코팅, 포장재 등에 이용될 수 있으며, 현 재 화장품 제조에 사용되고 있다.
미래 산업용 소재로서도 개발되고 있으며, LiB 전해질 첨가제, 수소탱크용 고 배리 어 소재로 연료전지차, 수소 스테이션용 수소탱크에 활용 이 기대되고 있다. 의료용으로는 창상 치료, 재생의료 재료 로 기대되고 있다. 일본의 공작기계 메이커 스키노머신 사는 알루미나, 바 륨티탄 같은 세라믹 바인더용 CNF 슬러리를 개발하였다.
폴리비닐알코올 수지와 함께 수계 바인더로 사용하여 세라믹 기판의 중간재인 그린 시트 제조 시에 소량 첨가로 강도, 굴곡성을 향상할 수 있다. 파우더 제품용은 용제계에 활용하여 전자부품, 모빌리티 제조공정용으로 전개하고 있으며, 압출 성형으로 하니콤 제조에 적용을 추진 중이다(그림 13).
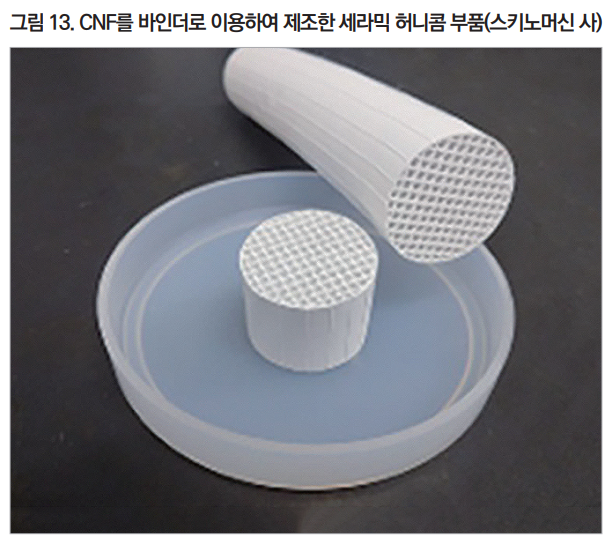
CNF의 활용에 가장 큰 제약은 고가의 제조 비용이다. 일본의 교토에 있는 수정화학(垂井化學)은 CNF의 미세화에 필요한 독자의 화학 기술 및 제조 에너지 저감을 통해 기존 제품보다 저렴하게 CNF를 사업화하여 판매 및 응용 분야를 개척하고 있 다. 섬유 폭은 약 3㎚로 스프레이로 뿌려도 겔 형상을 유지하여 무기, 미세금속 분말 혼합에서 균일하게 분산시키며 안정화 한다.
또한 고농도에서는 분산제 첨가제로 사용 가능하다고 보고하였다. CNF는 표면에 친수성 그룹인 –COOH, -OH 등을 갖고 있어서 소수성 고분자와의 혼합 시 분산이 어렵다. 이를 개선하기 위해 전편과 본 보고서의 2, 3장에서 언급한 표면 개질 기술이 연구되고 있으나, 이들 방법은 화학반응 공정이 수반된다.
일본의 한본약품공업은 간단한 방법으로 소수성 고분자에 CNF의 분산성을 향상하기 위한 첨가제를 개발하였다. 폴리글 리세린계 2종류의 분산제를 사용하여 폴리프로필렌-CNF 복합체에서 CNF의 응집을 억제시킬 수 있었다. 즉, 고분자와 CNF 혼합 시 분산제를 첨가하는 것만으로도 우수한 분산 효과를 얻을 수 있다. 이 분산제는 계면활성제로서 표면의 친수성 부분에 흡착해서 표면을 소수성화 한다.
또한 이 방법을 사용하면 CNF 수분산에서 수소결합이 어려워 3차원 네트워크 생성 이 억제된다고 발표하였다. 일본의 동아합성은 셀룰로오스의 나노 피브릴화에 사용하는 고가의 특수 장비를 사용하지 않고 일반 교반기를 사용하여 투자비가 적게 드는 방법을 개발하였다.
이 기술은 강산화제인 NaOCl을 고농도로 사용, 목재를 산화시켜 CNF를 제조할 수 있는 방법이다. 이 방법을 사용하면 제조 에너지를 삭감하고 CO2 배출량도 억제 가능해서 전체 제조 비용을 종래의 1/5로 줄일 수 있다고 발표하였다. 저점도 페이스트, ABS 수지/광 경화 수지 등의 보강제, 세라믹 등의 분산제로 응용 분야를 개척 하고 있다 일본의 Fujiki 사는 CNF 마스터배치(M/B)를 개발하였다. TEMPO 법으로 개발된 CNF를 건조하여 분말을 제조하고, 이 를 식물계 왁스, 변성 로진 등과 혼합, 3본 롤로 가공하면 분산이 잘되는 M/B 상태가 되며, 이를 이용하여 PP, PS, PE 복합체 제조에 이용할 수 있다(그림 14).
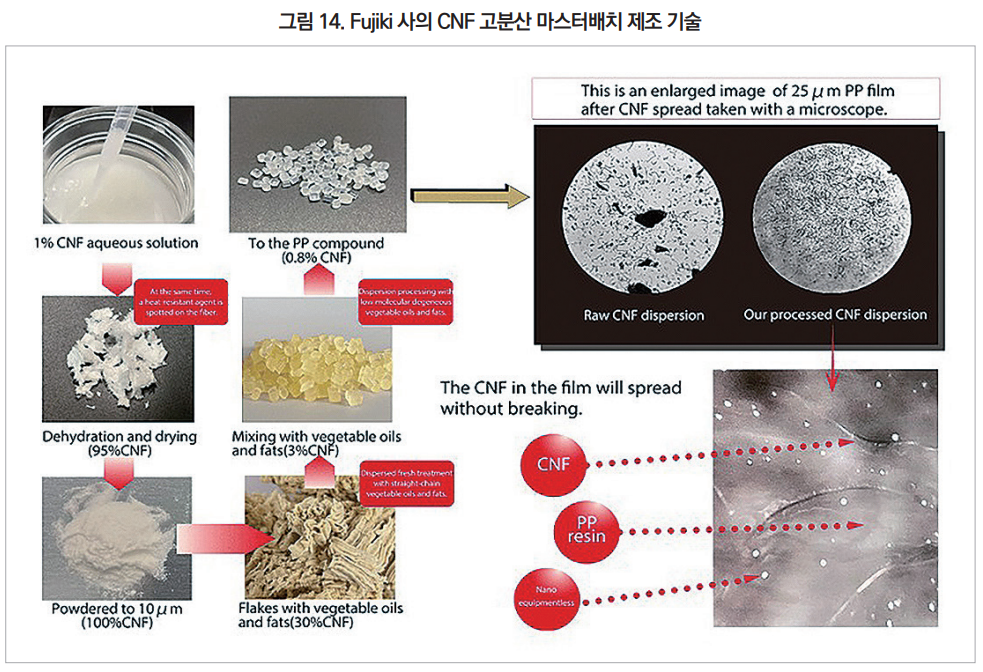
나노 셀룰로오스는 바이오매스 자원에서 풍부하게 얻을 수 있으며, 생분해성을 갖고 있어 탄소중립 실현에 기여할 수 있는 주요 환경 친화 소재이다. 셀룰로오스에 있는 OH-그룹은 저분자, 고분자, 효소 등과 화학반응으로 친수성, 소수성 표면으로 개 질을 가능하게 해주며 개질된 나노 셀룰로오스는 용융, 용액, 에멀젼, 분말 상에서 다른 소재와 혼합 시 분산성을 향상시킬 수 있기 때문에 여러 응용이 기대되고 있다.
최근에 셀룰로오스 나노섬유(CNF) 및 나노결정(CNC)이 갖는 고강도, 저비중, 환경 친화 등의 특성을 활용하고자 나노 셀룰 로오스 제조 및 표면 개질과 새로운 응용 분야 탐색이 활발하게 진행되고 있다. 현재까지 진행된 주요 응용 분야는 고분자 복합 소재, 바이오 메디칼, 용수 및 폐수처리, 다양한 센서 및 웨어러블 소재, 화장품, 식품 포장 등 광범위한 영역에 걸쳐있다.
1, 2편 에 걸친 본 심층 보고서에서는 저분자, 고분자, 물리, 효소를 이용하여 CNF의 표면을 개질하는 방법과 최근 시도되고 있은 응 용에 대하여 중점을 두고 기술하였다. 나노 셀룰로오스가 이들 영역에서 성공적으로 활용되기 위해서는 에너지 절감 등의 공정개선과 최적화를 통한 원가절감 및 대량생산 기술, 환경친화적인 표면 개질 기술과 응용에 대응하는 맞춤형 표면 개질 기술 및 분산 기술 개발 등에 더 많은 노력 이 필요하다.
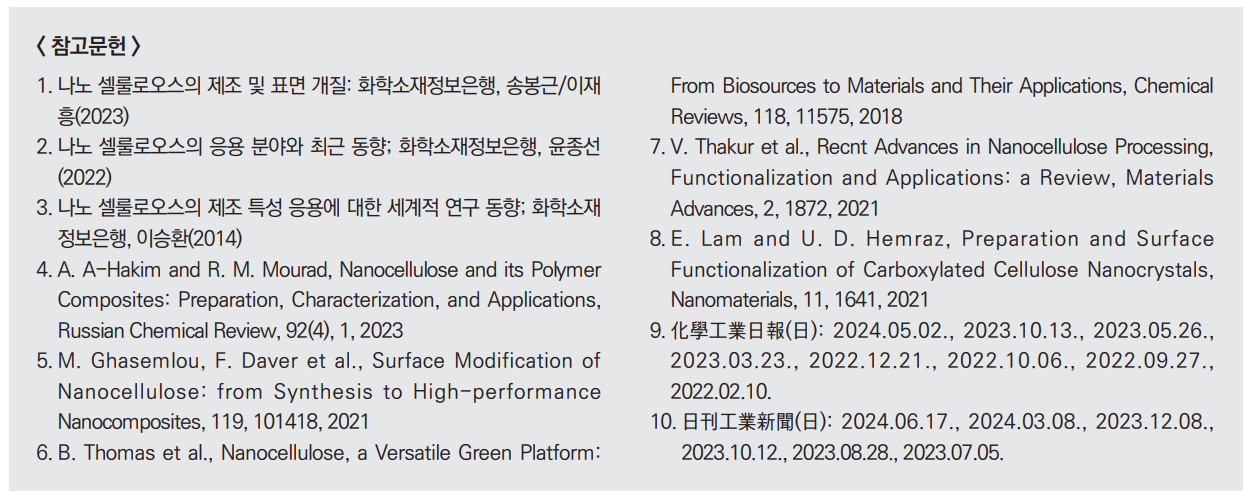
