기술과 솔루션
가소화 스크류에 관한 모든 것 Part 1
WITTMANN innovations (Volume 14 - 1/2020)
Filipp Pühringer/heads the WITTMANN BATTENFELD
Process Engineering Development Department.
총 3부로 구성된 기획 시리즈 중 Part 1에서는 가소화 장치의 기본 설계와 사출장치의 올바른 선정에 관해 설명한다. 사출량을 기준으로 필요한 스크류 직경을 확인하는 방법을 보여준다. 평균 체류 시간에 대한 공식을 사용하여 재료의 활용도 및 열부하를 산정할 수 있다(높은 부품 품질을 위해 낮게 유지해야 한다). 마지막으로, 최대 사출압력과 사용 가능한 스크류 토크는 성공적인 사출성형 생산을 위한 핵심 변수이다. 이는 배럴 및 스크류 조합 선택을 위한 기본 원칙과 추가적으로 최적화를 위한 시작점이다.
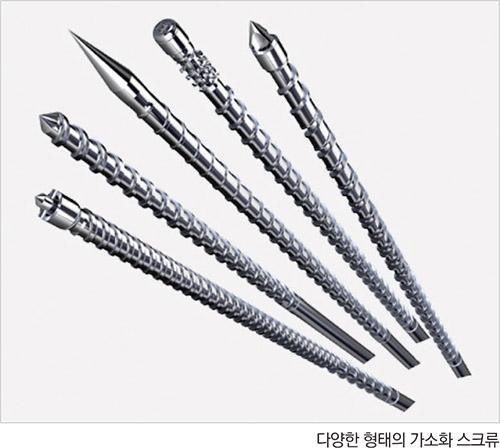
사출성형기를 설계하는 것은 실제로 매우 복잡한 작업이며, 기계를 선택할 때 잘못된 선택을 하지 않으려면 먼저 많은 주요 매개 변수를 식별하여 산출에 포함해야 한다. 고품질의 부품을 성형하는데 중요한 성공 요인이므로 가소화 장치에 특히 주의해야 한다. 이러한 장치가 충족해야 하는 요구 사항은 매우 복잡하지만, 장비 설계단계에서 이미 서로 다른 측면을 신중하게 균형 조정함으로써 목표 충돌을 제거할 수 있다. 예를 들어, 가능한 최고의 처리량에 대한 요구는 재료 균일성, 용융 품질, 운반 안정성 및 내마모성 요구 사항과 충돌한다. 내마모성은 가공된 재료의 유형에만 의존하는 것이 아니라 형상과 올바른 재료선택 간의 체계적인 상호 작용으로 인한 속성이다.
여기에 제시된 논의는 가소화 장치와 사출장치의 기본 설계를 계획할 때 고려해야 할 사항에 중점을 둔다. 가소화 장치와 사출장치의 기본 설계에 대한 정의는 다음 단계의 전제 조건, 즉 스크류 구조의 선정을 제공한다. 다음 시리즈에서는 새로운 스크류 구조의 개발에 대해 자세히 설명한다.(새로운 스크류 구조를 개발할 때의 제한 요인은 압력, 온도, 계량 토크 등과 같이 성형 재료와 기계에 가해지는 하중이다.)
가소화 장치의 기본 설계
사출량 Shot volume
성형할 재료에 따라 가소화 장치의 최적 작동 범위는 대략 1D에서 3D까지의 스크류 직경(D)이다. 사출장치를 로딩하기 위해 4D 이상의 계량 행정을 선택하면 더 이상 최대 공정 안정성을 보장할 수 없다. 가능한 결과는 계량 시간 변동, 공기 유입 및 장치의 마모 가속이다. 그 이유는 계량 행정이 증가하면 유효 스크류 길이*가 줄어들기 때문이다. 따라서, 채널의 길이는 압축 수준으로 단축되는데, 이는 재료가 용융을 위해 충분한 열을 흡수하는 시간이 짧다는 것을 의미한다. 결과적으로, 채널 내부의 압력이 상승하여 재료와 기계가 모두 변형된다. 사출량 VSCH는 다음과 같이 산출된다.
* 유효 스크류 길이: 재료 공급 구멍의 앞쪽 가장자리와 배럴의 작업 존 내부의 스크류 끝 사이에 있는 스크류 길이로 재료 이송 및 압력 상승에 결정적이다.

핫러너 금형의 경우 핫러너를 주기적으로 언로드해야 하는지 여부에 따라 핫러너 내부의 용융재료 압축을 고려해야 한다(예: 흐름이 용이한 재료로 오픈 핫러너의 경우). 용융 압축률이 높고 사출압력이 높을수록 핫러너의 계수 fHK가 높아진다. fHK의 일반적인 값은 0.1과 0.3 사이이다. 따라서, 비교적 작은 부품 중량 mT로도 필요한 스트로크양이 두 배가 될 수 있다.
굳은 스프루를 사용한 금형의 경우 계수 fHK는 0을 향하는 경향이 있다. 굳은 스프루 시스템의 중량은 부품 중량 mT에 포함되고 그에 따라 고려된다는 점에 유의하는 것이 중요하다. 잔류 용융 쿠션량(VMP)은 스크류 직경(D)과 관련하여 변해야 한다. 일반적으로, 0.1 내지 0.3D의 스크류 스트로크가 보압 단계의 끝 배럴 내부에서 발견되어야 한다. 따라서 용융 쿠션량 VMP는 다음과 같이 계산되어야 한다.
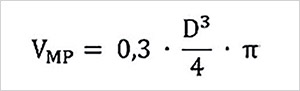
스크류 직경은 이론 사출 용적에서 도출할 수 있다. 이미 언급한 바와 같이, 계량 스트로크는 1~3D 스크류 직경 길이와 동일한 거리로 정의할 수 있다. 따라서 다음 제한 직경이 스크류에 적용된다.
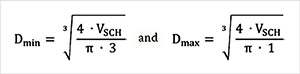
스크류 직경의 최종 선정에서 성형할 모든 부품의 특성을 고려해야 한다. 계산된 직경 범위를 신중하게 고려한 후 실제 스크류 직경이 선정된다.
체류 시간 Residence time
체류 시간은 배럴 내부에 지정된 플라스틱 입자가 소요한 시간이다. 그러나 배럴 내부의 복잡한 흐름 과정으로 인해 모든 용융 분율에 동일하게 적용되는 정확한 시간 범위는 없지만, 특정 체류 시간 분포가 있다. 이는 채널 체적, 총 사이클 시간, 재료 벌크 밀도, 용융 밀도 및 배압 및 스크류 속도와 같은 공정 매개 변수와 같은 요소에 따라 다르다.
체류 시간 분포는 균일성과 충분한 가소화에 관한 재료 품질에 대한 정보를 제공한다. 체류 시간 분포가 넓을수록 균질화 효과가 높아진다. 체류 시간 분포를 계산하는 것은 복잡한 수학적 작업이다. 그러나 실제로는 평균 체류 시간 tV에 대한 단순화된 공식이 종종 평가에 충분하다. 평균 체류 시간은 플라스틱 입자가 배럴 내부에서 평균적으로 소요하는 시간이다. 평균 체류 시간은 재료의 열 손상의 첫 번째 지표로 제공된다.
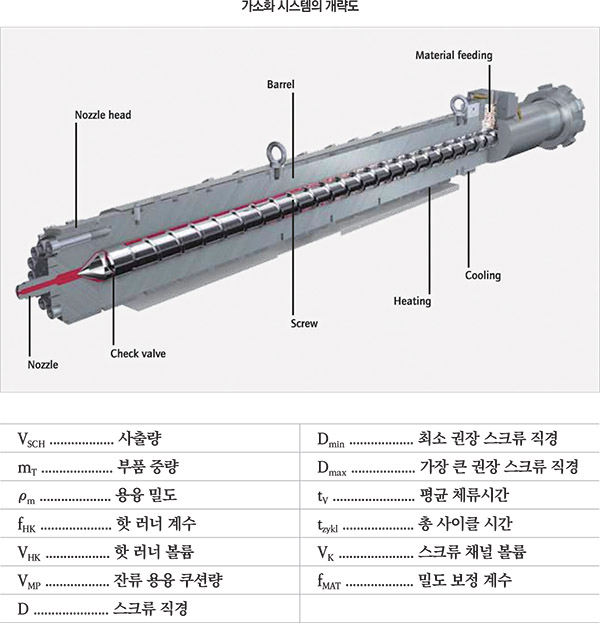
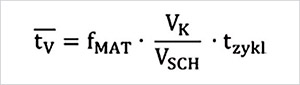
계수 fMAT는 변하는 재료 밀도를 고려한다. 예를 들어, 고체 재료의 밀도는 용융 수지의 밀도보다 높으며, 이는 다시 과립화된 원재료에서 발견되는 벌크 재료 밀도보다 높다. 실험에 따르면 이 요소는 일반적으로 0.8과 0.9 사이이다.
따라서, 산출된 체류 시간은 스크류의 공급 존에서 과립 입자 사이의 빈 공간에 의해 감소된다.
일반적인 유형의 플라스틱의 경우 2분에서 약 8분 사이의 최적 시간 창이 예상된다.
체류 시간이 최소 1분 이하로 떨어지지 않아야 한다. 또한, 첨가제 및 베이스 폴리머의 유형에 따라 플라스틱의 열 안정성에 큰 차이가 있음을 언급해야 한다. 따라서 일부 특수 유형의 재료(예: 렌즈 생산용)는 30분 이상의 체류 시간을 쉽게 견딜 수 있는 반면, 의료 성분이 있는 플라스틱의 경우 분해 프로세스가 이미 2분 후에 시작될 수 있다.
특정 스크류 구조를 개발하는 단계에서 정확한 채널 볼륨은 아직 알려지지 않았다. 여기에서 기존 표준 3존 스크류의 볼륨을 예비 방향으로 사용할 수 있다. 동일한 원리에 따라 작동하는 스크류의 경우 일반적으로 볼륨이 표준값에서 약간 벗어난다.
원칙적으로, 체류 시간의 계산은 스크류의 전체 길이에 대한 제1 기준값을 제공할 수 있다. 스크류는 매우 짧은 체류 시간 동안 연장되고 매우 긴 체류 시간 동안 단축된다.
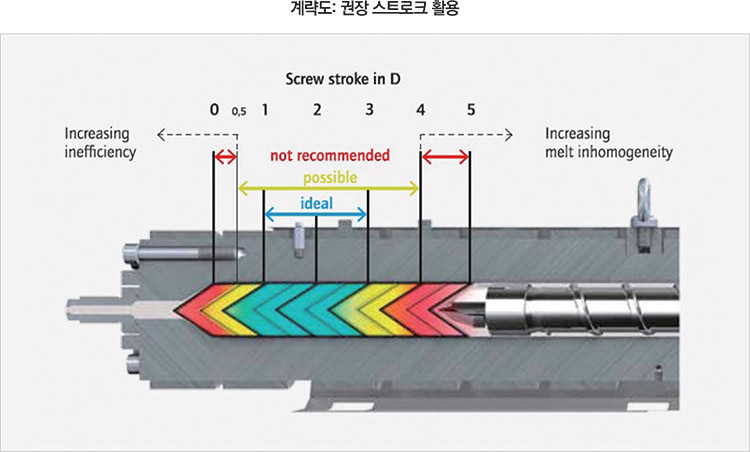
최대 스크류 토크 Maximum screw torque
모든 사출장치에는 최대 스크류 구동 토크가 있다. 설치된 드라이브 시스템에 의해 고정된다. WB의 사출성형기는 다양한 장비 변형과 함께 사용하여 더 높은 구동 토크를 제공한다. 이와 관련하여, 구동 스크류의 기계적 강도도 고려해야 한다. 여기서 가장 얇은 단면이 제한 요인이다.
따라서, 구동 토크는 스크류 파손을 방지하기 위해 각 타입의 스크류의 강도에 맞춰진다. 필요한 토크를 결정하기 위해, 성형할 재료의 점도뿐만 아니라 스트로크 활용률 및 체류 시간과 같은 미리 정의된 변수가 결정적이다.
WB(Wittmann Battenfeld)는 정확한 계산 도구를 사용하는 것 외에도 이전에 설치된 수많은 시스템에서 광범위한 경험을 바탕으로 각 경우에 올바른 선택을 할 수 있다.
최대 사출압력 Maximum injection pressure
모든 경우에 가능한 최대 사출압력을 확인해야 한다. 사출장치의 모든 크기에 대해 서로 다른 치수의 배럴을 선택할 수 있다. 특히 큰 배럴의 경우 최대 사출압력을 준수해야 한다. 스크류의 단면적이 더 크기 때문에, 동일한 사출력을 얻도록 더 낮은 절대 사출압력이 설정될 수 있다.
또 다른 중요한 점; 스크류 직경이 작을수록 특정 사출압력 대 사출력의 전달 비율이 높아져 제어 정확도에 영향을 미칩니다. 이것이 궁극적으로 어떤 크기의 큰 장치에 작은 배럴을 설치할 수 없는 이유이다.
실제로, 요구되는 사출압력은 경험에 의거한 값으로부터 도출되거나 계산에 의해 결정된다(예를 들어, 충진 시뮬레이션에 의해). 그럼에도 불구하고 충분한 예비를 제공하기 위해 기계 공학 설계를 해야 한다.
의사 결정을 위한 기본 변수
사출량, 체류 시간, 최대 스크류 토크 및 최대 사출압력: 이러한 핵심 파라미터를 명확하게 하면 스크류의 크기를 결정하고 스크류에 맞는 올바른 사출장치를 선택할 수 있게 하거나 혹은 두 가지 결정에 강하게 제한해야 한다.
“Wittmann innovations” 매거진의 다음 호인, 이 기획 시리즈의 두 번째인 Part 2에서는 3-존 스크류의 예를 사용하여 주어진 스크류의 형상을 시뮬레이션 평가하는 기본 방법이 제시된다.