기술과 솔루션
스마트공장(Smart Factory)을 위한 사출성형 모니터링 데이터 분석 (부제: 사출성형 공정 그래프(Graph)에 대한 분석 및 이해)
최근 사출성형 산업계에서는 극심한 경쟁 구도에 직면하고 있으며, 이로 인하여 지속적인 생산성 향상, 엄격한 품질관리, 인건비 절감 등의 요구에 직면하고 있다. 이러한 산업환경 변화에 대응하기 위하여, 고품질 또는 대량 생산 플라스틱 제품을 중심으로 센서를 이용한 사출성형 모니터링 시스템의 활용이 확대되고 있다. 이 연재 기사에서는 각종 센서와 사출기에서 얻어지는 데이터(그래프)를 이해하고 활용하는 방법에 필요한 기본 지식에 초점을 맞추어 기사를 연재하고자 한다.
RJG사는 사출성형 교육, 기술 및 리소스 분야에서 세계적인 리더로 인정 받고 있는 회사이며, 사출성형 공정 모니터링에 사용되는 센서와 장비를 생산/공급하고 있다. 본 기사의 게재된 자료 들은 RJG 사의 모니터링 시스템(eDart/Copliot)에 기반을 두고 있으며, RJG 사에 Copyright의 모든 권한이 있음을 밝힌다.
자료제공: 이길호 대표이사(씨에이프로(주),
RJG 사 공식 컨설턴트/트레이너)
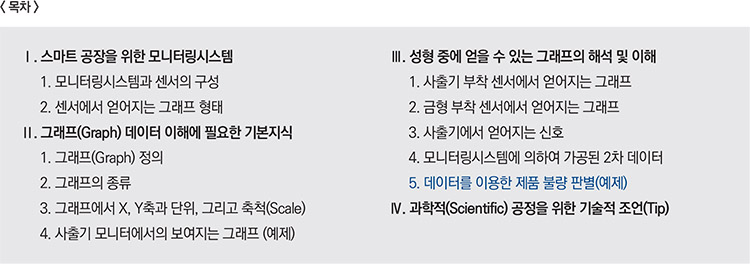
Ⅲ. 성형 중에 얻을 수 있는 그래프의 해석 및 이해
5. 데이터를 이용한 제품 불량 판별(예제)
사출 성형품의 불량은 적절하지 않은 금형 설계, 사출기의 불안정한 작동, 부적절한 성형조건, 그리고 재료의 변동성 등의 요인에 의하여 발생하며, 여기에서는 초기 시사출에서 발생하지 않지만 양산 중에 부정기적으로 발생하는 성형품 불량에 대하여 중점적으로 얘기하고자 한다.
일반적인 대부분의 성형품 불량은 캐비티의 형상과 두께 분포, 게이트의 형태/위치/개수, 런너의 형태와 배열 등의 금형 설계 변경으로 해결이 가능하다. 그러나 양산에서 돌발적으로 발생하는 불량은 금형 외에 다른 요인에 의하여 발생할 확률이 높음으로 지속적인 모니터링을 통한 품질 관리가 필요하다.
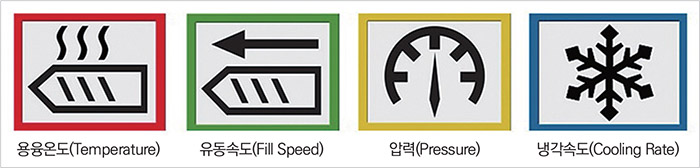
사출성형에서 발생하는 불량을 제어하기 위해서는 사출기와 성형조건, 그리고 재료에 대한 폭넓은 이해가 필요하며, 많은 변수(Parameter)들과 불량 현상과의 관계를 직접적으로 파악하기보다는 4대 변수를 매개로 이해하는 것이 많은 도움이 된다.
4대 변수는 용융온도(Melt Temperature), 충진 속도(Fill Speed), 압력(Cavity Pressure), 냉각 속도(Cooling Rate)를 말하며, 이들과 불량 발생 원인 관계에 대한 이해는 시스템적(Systematic)인 사고를 할 수 있는 기본적인 지식을 제공한다.
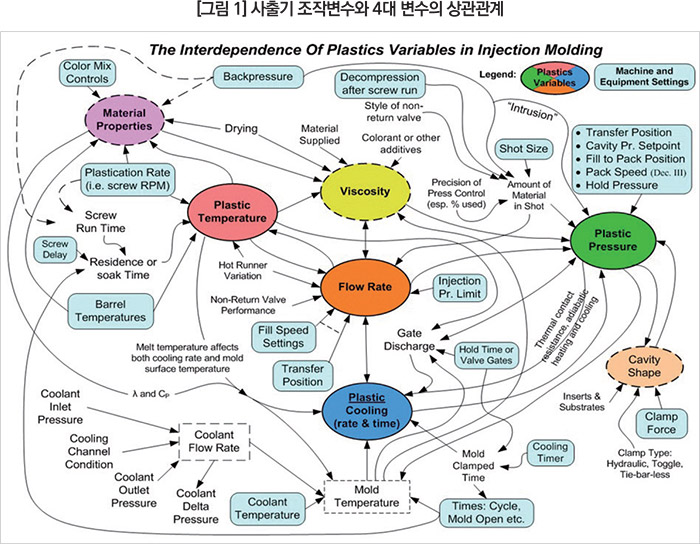
일반적으로 양산에서 외부의 변수에 의하여 불규칙적으로 발생하는 Short Shots(미성형), Flash(플래쉬), Sink-mark(싱크 마크), Dimensional Variations(치수안정성), Warp(변형), Gloss Gradient(표면광택 차이), Strength(강도 차이) 등과 같은 불량을 4대 변수와 연관시켜 분류하고 사고하면, 비교적 손쉽게 원인과 해결책을 파악할 수 있다.
[그림 1]에서 보는 바와 같이 재료의 물성 중에 가장 중요한 점도(Viscosity)와 4대 변수는 직간접적으로 관계가 있으며, 이러한 4대 변수는 사출기의 많은 조작변수와 관련되어 있다. 많은 조작변수를 직접적으로 공정 중의 재료의 물성 변화와 연관시키고 원인과 해결책을 찾기가 쉽지 않음을 알 수 있으며, 4대 변수에 대한 이해와 활용이 중요함을 보여 준다.
캐비티 내의 압력/온도 센서의 필요성
제품의 불량 유무는 사출기의 동작과 재료, 그리고 외부 환경의 일관성(Consistency)에 의하여 결정되지만, 사출기에서 나타내는 성형 결과값이나 그래프로 이를 판단하기가 쉬운 것은 아니다. [그림 2]에서 보는 바와 같이 재료의 압축성과 점성으로 인하여 사출기에서 나타나는 압력과 캐비티에서 측정하는 압력의 측정범위가 현격하게 차이가 나기 때문이다. 예를 들어 사출기의 충진 최대 압력 값이 100MPa인 경우에 캐비티 유동 말단부의 압력이 압력 손실로 인하여 10MPa로 작용하고, 유동 말단의 압력이 5MPa 변동함으로 미성형이 발생한다면, 사출기에서의 압력 변화를 이용하여 유동 말단의 미성형(Short-shot)을 감지할 수 있는 가능성이 5%, 캐비티 압력센서를 이용하면 가능성이 50%일 것으로 예측이 가능하다.
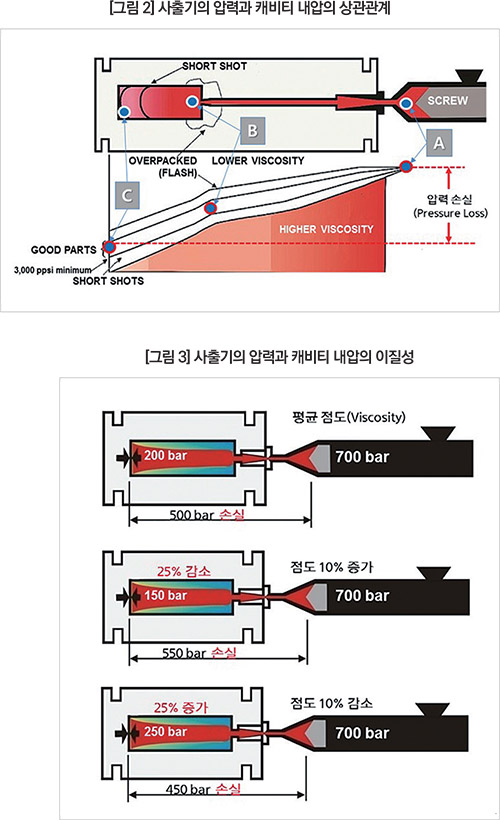
[그림 3]에서는 사출기에서의 압력이 일정하더라도 캐비티의 압력이 달라지는 사례이며, 이는 사출기의 압력 변화를 모니터링하여 성형품의 불량 유무 판정하는 것이 어려움을 보여준다. 사출기의 압력이 700bar로 일정하게 매 공정에 작용하더라도, 충진된 재료의 점도(Viscosity)가 다르면 충진 말단에서의 압력은 점도의 높고 낮음에 따라 크게 변화하며, 일반적인 플라스틱 재료의 점도 편차인 +/- 10%의 변화에도 46% 정도의 압력 변화가 발생한다.
위의 2가지 예는 사출기의 성형 결과를 이용하여, 제품의 불량 유무를 판정하기에는 낮은 가능성을 가짐을 보여주며, 이는 캐비티 내의 센서를 활용함으로써 극복할 수 있다.
다음은 양산 공정에서 가장 많이 발생하는 2가지 불량, 미성형(Short-shot) 또는 플래쉬(Flash)와 치수 불균일(Dimensional Inconsistency)을 중심으로 그래프의 특성과 불량을 판독하는 데에 필요한 팁(Tip)을 이야기하고자 한다.
5.1 미성형(Short-shot)/플래쉬(Flash)
미성형(Short-Shot)과 플래쉬(Flash or Burr)는 4대 변수의 관점에서 보면, 온도, 압력, 속도와 관계가 있으며, 모두 점도의 변화에 영향을 끼쳐서 불량이 발생한다. 예를 들어 온도가 높으면 점도가 낮아지고 압력의 전달이 용이하여 압력이 과도하게 상승하고 플래쉬(Flash)를 유발할 가능성이 커지며, 반대로 온도가 낮아지면 압력 전달이 쉽지 않아 유동 정체 현상이 발생하고 끝단의 압력이 과도하게 낮아 미성형을 유발한다.
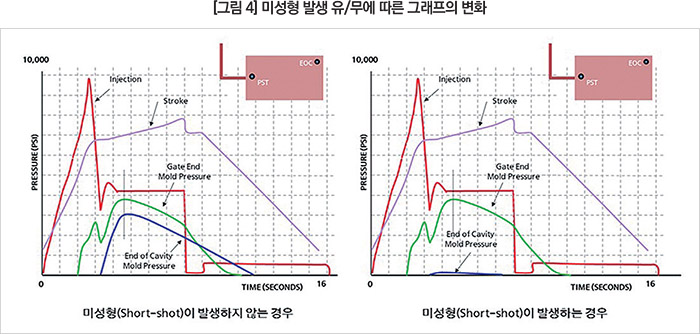
[그림 4]에서와 같이 유동 말단의 압력센서에서 관측되는 그래프가 정상적인 상태에 비하여 과도하게 낮은 경우에 말단이나 근처의 얇은 보스(Boss) 또는 리브(Rib)에서 미성형이 발생할 확률이 높아진다.
미성형의 유/무는 성형조건 변경 실험을 통하여 정확한 압력(센서) 기준을 설정하는 것이 바람직하다.
유동 말단 예측에 대한 Tip
아래의 그림에서와 같은 두꺼운 부분과 얇은 부분이 혼재되어 있는 제품에서 EOC 센서의 위치를 선정하기 위해서는 유동 말단 예측에 매우 주의를 기울여야 한다. 일반적으로 위의 우측 그림과 같이 게이트와 게이트 사이를 웰드라인 형성과 유동 말단 지역으로 예측할 수 있으나, 극단적인 경우에는 유동 말단의 위치가 아래의 그림과 같이 속도의 변화에 의하여 변경될 수도 있음을 주의하여야 한다.
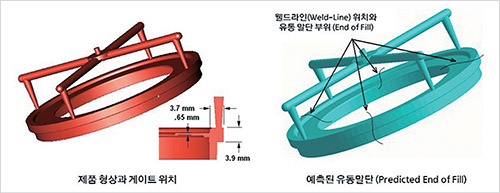
이러한 속도에 따른 유동 말단의 변경을 예측하기 위해서는 유동 해석(Filling Simulation) 소프트웨어를 이용한 해석이 매우 유용하며, 이 외에도 시사출(Mold Trial) 시에 속도를 변화해가며 유동 말단의 위치를 확인하고 센서를 설치하는 방법도 사용된다.
우측의 그림은 속도에 따른 유동 말단에서의 압력의 안정성을 보여주는 그림이며, 속도가 느릴수록 안정성을 낮아져 각 Cycle마다 압력 크기와 작용 시간이 일정하지 않으며, 고속일수록 안정성이 높아져 각 Cycle마다 압력 곡선의 형상이 균일함을 알 수 있다. 이는 점도의 특성에 기인한 것으로 전단률(충전 속도)이 높을수록 점도가 낮아지면서 변동성이 줄어들기 때문이다.
안정성(Stability)와 불안정성(Instability)의 판별에 대한 Tip
일반적으로 한 Cycle에서의 압력과 온도, 그리고 속도의 변화를 보는 사이클 그래프로 모든 양산 과정을 모니터링 할 수 없으며, 그래프의 곡선에서 얻어지는 값들, 예를 들어 최대/최소 압력값, 적분값, 기울기 등을 기준으로 불량 판별을 수행한다. 여기에서는 선정된 기준값들이 생산 과정에서 어떤 패턴으로 변화하고 분류할 수 있는지를 고찰하여 보고자 한다.
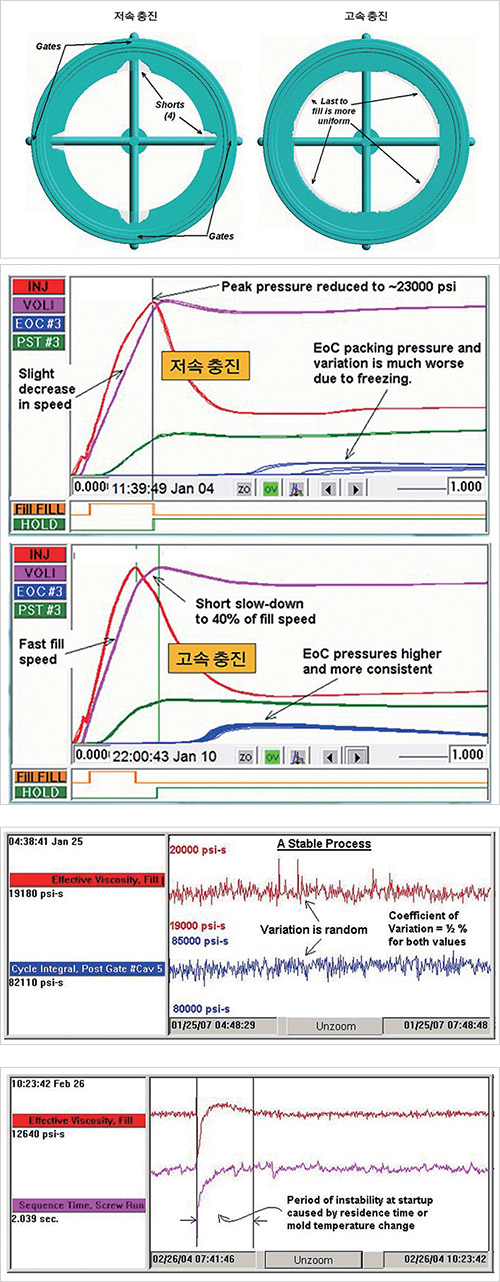
(1) 안정적인 프로세스 패턴
우측의 그림은 안정적인 프로세스의 예를 보여주며, 작은 변동이 존재하지만 크게 변화하는 패턴을 보여주지 않는다. 점도에서 흥미로운 변동이 몇 가지 있지만, 대체로 표시된 3시간 동안은 안정적이고, 상승, 하락 또는 순환적 추세가 없으며, 변동은 각각의 평균값에 비해 작음을 볼 수 있음으로 안정적이다.
(2) 시작 시 불안정 프로세스 패턴
우측의 그림은 사이클이 중단되고 다시 시작할 때 발생하는 전형적인 현상으로, 프로세스가 안정화되는 데 일정 이상의 시간이 요구됨을 볼 수 있다. 제품이 Q/C 요구 사항을 만족하더라도 프로세스는 약 25분 동안 안정되지 않고 있으며, 이는 128개 캐비티를 가지는 대형 금형에서 나온 결과이다.
(3) 한 캐비티의 불안정한 순환 프로세스 패턴
우측의 그림은 캐비티 #1에서의 말단부의 압력 적분 값이 명확한 순환 패턴을 가지고 변화하는 것을 알 수 있으며, 변화 수준은 약 3%의 변동 계수를 가지고 있다. 이런 패턴의 원인을 찾아서 안정화하는 것이 대량 생산에서 불량품을 최소화하는 가장 빠른 길이며, 이 경우는 금형 온도 조절기가 5도 정도 주기적으로 변화하는 것이 원인으로 판명되었다.
(4) 다중 순환 변화 프로세스
우측의 그림은 불안정한 배압(2,300~2,700psi)으로 인하여 샷 크기의 변화를 유발하여 발생하는 현상을 보여주며, 캐비티를 충진하는 시간(CFill t)이 배압의 변화에 따라 변화함을 볼 수 있다. 이러한 공정에 서는 안정적인 품질의 부품을 만드는 것이 매우 어려우며, 이를 해결하기 위해서는 사출기의 모터 성능을 점검하고 최적화된 배압과 스크류의 회전속도를 선정하여야 한다.
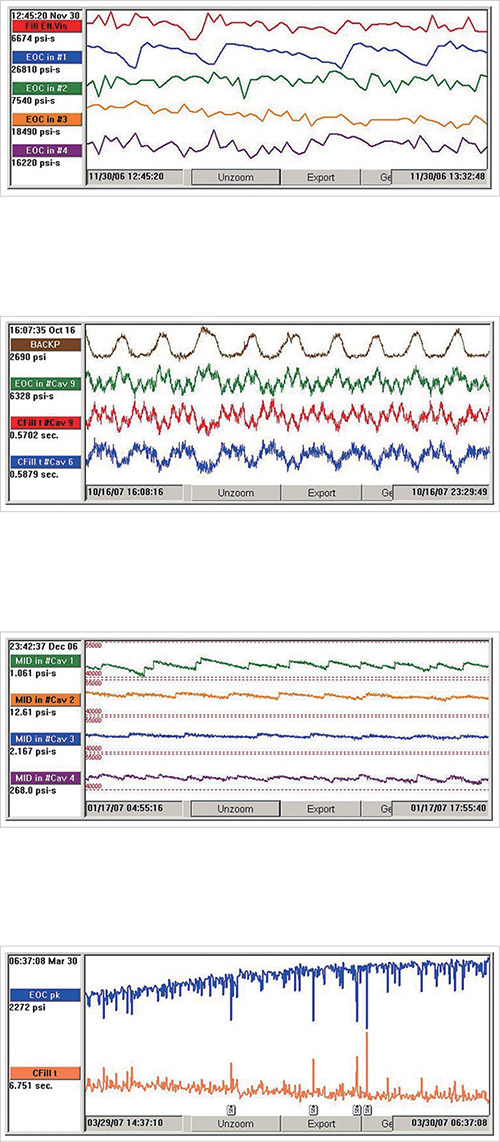
(5) 다양한 주기를 갖는 순환적 변화 프로세스
우측의 그림은 모든 순환 패턴이 동일하게 일정한 주기를 갖는 것은 아니며, 각 캐비티가 서로 다른 주기의 패턴을 가지고 있다. 사이클은 각 주기의 끝에서 갑작스러운 변화가 나타나며, 이러한 패턴은 핫 러너 팁이 천천히 막혔다가 더 높은 압력으로 인해 갑자기 파편이 방출된 다음 다시 매끄럽게 흐르는 상황에서 이러한 그래프를 보여준다.
(6) 단기 안정성 – 장기 불안정성 프로세스
우측 그림의 초기 약 2시간 분량의 데이터에서 눈에 띄는 변동은 없고 데이터는 무작위 패턴을 보임으로 우리는 이를 안정적인 프로세스라고 결론 내릴 수 있다. 하지만, 금형의 크기가 큼으로 인하여 온도는 꾸준히 상승하게 되어, 전 공정(약 16시간) 동안 안정적이지 않음을 알 수 있다.
공정 중에 온도가 지속적으로 상승하면서 캐비티 충진 시간은 7.6초에서 6.6초로 감소했고, 캐비티 피크의 끝은 1,400psi에서 2,300psi로 증가하였기 때문에 프로세스는 처음에는 안정적으로 보였지만 전체적으로는 안정적이지 않은 것으로 판단할 수 있다. 이 경우 온도를 안정화할 방법이 없었기 때문에 불안정한 온도에서도 품질을 일정하게 유지해야 할 필요가 있으며, 이를 위하여 말단의 캐비티 압력을 기준으로 공정을 제어할 수 있는 성형법을 적용하여 플래쉬(Flash)를 방지할 수 있도록 하였다.
5.2 치수 불균일 (Dimensional Inconsistency)
각각의 사이클마다 치수가 일정하지 않은 것은 성형공정 중에 캐비티 내의 온도와 압력이 일정하지 않아 발생하며, 이는 캐비티에 설치된 압력센서를 이용하여 모니터링하고 불량 판별을 수행할 수 있다.
우측 그림의 왼쪽 그래프와 같이 품질 규격을 통과한 사이클 제품의 그래프를 기준(Template)으로 선정하고, 각각의 사이클 그래프를 이와 비교하여 치수 불량의 유무를 결정한다.
오른쪽은 제품의 크기가 전체적으로 작은 경우에 나타나는 전형적인 그래프이다. 반대로 파란색과 초록색의 실선이 점선보다 높게 나타나는 경우는 제품의 치수가 전체적으로 크게 나타나는 경우일 것이다.
우측 그림은 제품의 치수가 게이트 근처에서 작게 나타나는 경우의 그래프를 보여주며, 이러한 경우는 게이트의 고화 불량에서 원인을 찾을 수 있다. 게이트 고화 불량은 압력이 게이트를 통하여 외부로 손실되는 것을 의미하여, 이러한 현상의 원인으로 불안정한 사출기의 동작, 금형과 용융 수지의 온도 변화 등을 원인으로 예측할 수 있다.
상단 우측의 오른쪽 그림과 같이 반대로 초록색의 실선이 점선보다 높게 나타나는 경우는 게이트 부근의 제품 치수가 전체적으로 크게 나타나는 경우일 것이며, 이에 대한 원인은 V/P절환 후에 100% 충전(Pack)되는 속도와 압력의 크기에 변동이 발생하기 때문이다.
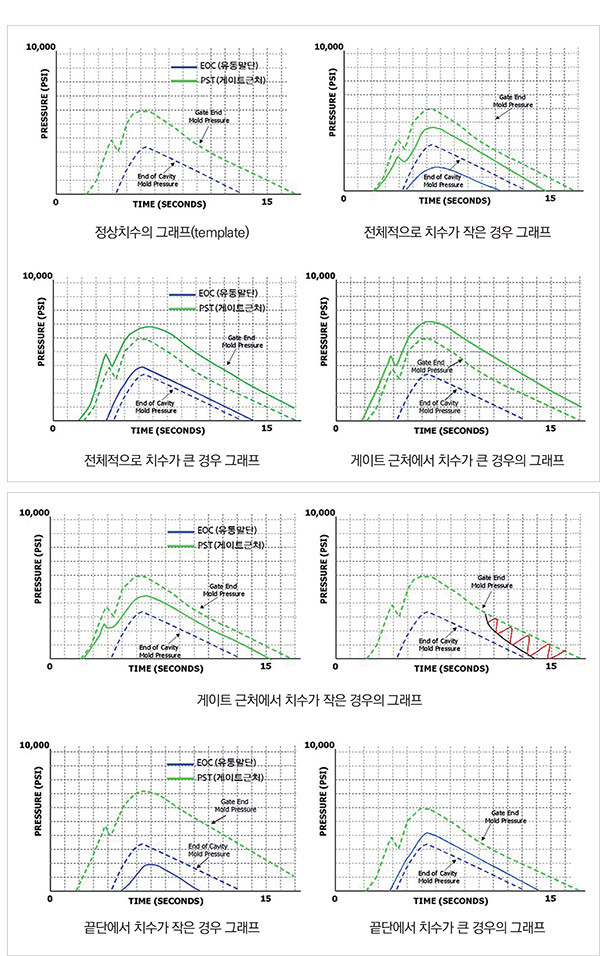
다수의 캐비티에서 얻어지는 곡선을 이용한 불량 판별에 대한 Tip
다수의 캐비티를 가지는 금형에 압력센서 또는 온도 센서를 설치하는 경우에 많은 곡선으로 인하여 각각의 캐비티의 변화를 그래프에서 인지하기가 어려울 경우가 종종 발생한다. 예를 들어 16-캐비티 금형에 각 캐비티에 2개의 압력센서를 설치하는 경우에 기본적으로 32개의 곡선이 한 개의 그래프 안에 표시되며, 이러한 경우, 사용자가 변화를 인지하는 것이 어려울 수 있다. 이러한 경우에는 각 곡선의 데이터를 2차 가공한 새로운 곡선 하나로 단순화하여 모니터링하는 것이 매우 효과적이다. (이를 유령 곡선(Phantom Curve)이라 부르기도 한다.)
우측 상단의 그림은 8개 EOC 압력센서에서 얻어지는 곡선과 1차 가공된 최대/최소 곡선을 동시에 표기한 것이며, 사용자가 문제 발생 여부를 판별하기 쉽지 않다. 그러나 우측 하단의 그림과 같이 최대/최소 곡선으로 단순화하고 2차 가공 곡선인 범위 곡선(#RNG)을 이용하면 더욱 손쉽게 판별할 수 있다.
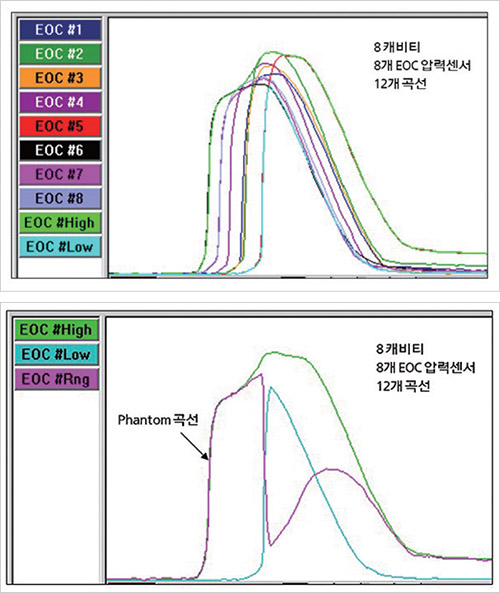
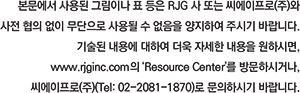
