1. 서론
실리콘은 오늘날 수많은 산업에서 이용되고 있으며, 그 제품의 수만 해도 수천종에 이르고 있다. 실리콘이 왜 이처럼 다양한 분야에서 폭넓게 사용되고 있는지에 대한 이유는 다음과 같은 몇 가지 이유로 요약해 볼 수 있을 것 같다. 그것은 내열성, 내한성, 내후성, 내UV성, 낮은 계면장력, 전기절연성, 낮은 독성, 우수한 가스 투과성, 점도 및 온도 변화가 낮은 것 등과 같은 실리콘의 독특한 특징에 따른 것이다. 그럼 먼저 실리콘의 역사와 그 구조로부터 고찰해 보고자 한다.
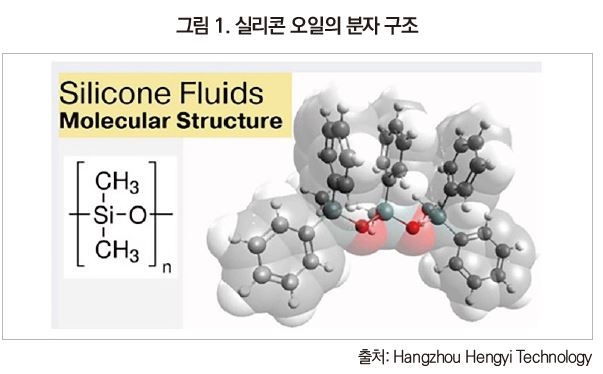
2. 실리콘의 역사
규소(Si)는 지구의 구성성분 중 약 28%에 해당하는 2번째로 많은 원소이다. 자연에서 무기고분자인 규소산염, 이산화규소 등의 형태로 있으며, 규소 단량체로는 거의 존재하지 않는다. 또한 규소 원자에 탄소가 직접 결합된 유기규소화합물도 자연에는 존재하지 않는다. 세계 최초의 유기규소화합물은 tetraethyl silane으로 1863년 C.Fridel과 J.M.Crafts에 의해 합성되었다.
Silicone(R2Si=O)은 Silico + Ketone(R2C=O)의 합성어로, 1908년 F.S.Kipping가 Chloro silane(H3SiCl)을 가수분해하고 최초로 합성하여 붙여진 이름이다. 실리콘은 무기화합물인 실록산 결합(-Si-O-Si-)을 주골격으로 하고 곁사슬에 유기기를 가지고 있는 Organopoly siloxane의 총칭이다.
실리콘의 공업적 생산은 1940년 GE가 alkyl chlorosilane 합성의 ‘직접법’을 발견하였는데, 규소산염을 환원하여 얻어진 금속 규소와 할로겐화 탄화수소에 copper 촉매를 사용하여 고온에서 반응시킨 chlorosilane류였다. 이와 같이 제조된 실리콘은 오늘날 전기·전자, 화장품, 건축·토목, 수송기기, 그 밖의 화학 분야에 널리 사용되고 있다.
3. 실리콘의 기본적 성질
규소(Si) 원자와 탄소(C) 원자는 주기율표의 같은 14족에 속하며, 정사면체 구조로 되어 있지만, 다음과 같은 차이가 있다.
① Si 공유결합 반경(1.17Å)이 C의 반경(0.77Å)보다 1.5배 크다.
② Si 전기음성도(1.8)는 C(2.5)에 비해 전기적 양성이다.
③ Si는 C에서 보여지는 이중 및 삼중결합이 거의 없다. 그러나 Si는 C에는 없는 3d 전자궤도가 있기 때문에 조건에 따라 sp3d 혼성궤도에 의해 5배위 화합물 존재도 가능하다,
이와 같은 특성 차이에 의해 규소 화합물은 탄소화합물에서 볼 수 없는 반응이 일어난다. 특히 Si-O, Si-Cl과 같이 전기음성도가 높은 hetero원자(X)와의 결합에너지는 대응하는 탄소화합물에 비해 크다. 하지만 Si+-X-의 분극에 의해 구핵 공격을 받기 쉬우므로 X의 탈리가 쉽게 일어나기도 한다. 예로서 규소 화합물의 Cl기나 alkoxy기는 치환되기 쉽고, hydrosilyl기(Si-H)는 염기성 조건 하에서 탈수소반응에 의해 silanol기(Si-OH)를 생성한다.
실리콘은 주사슬이 무기실록산결합(Si-O-Si)으로 되어 있고 곁사슬에 유기기를 가지는 유기-무기 hybrid 구조의 고분자 재료이다.
이들의 특징에 대하여 대표적인 실리콘인 dimethyl silicone과 paraffin 분자의 입체구조를 비교하였다.
dimethyl silicone의 주사슬 Si-O의 결합에너지는 444kJ/mol로서, 유기 폴리머의 주사슬 C-C 결합에너지 356kJ/mol이나 C-O 결합에너지 339kJ/mol에 비해 매우 크고 안정하다. 또한 Si 원자의 전기음성도(1.8)는 산소(3.5)에 비해 작기 때문에 Si+-O- 결합은 Si가 양으로 산소가 음으로 분극한 구조로 되어 있으며, 약 50%가 이온 결합성을 가지고 에너지적으로 안정화되어 있다.
이와 같은 siloxane 결합의 특징이 실리콘의 내열성, 내후성 성질을 만들어 낸다. 그러나 siloxane 결합의 이온 결합성은 siloxane 결합이 산, 염기 등의 이온 공격에 대해 약하다는 것을 의미하고 있다.
siloxane 결합의 거리는 1.64 Å로 C-C 결합거리 1.54 Å보다 길고, 더욱이 siloxane 결합각은 140°로 ethylene의 109°에 비해 크다. 또한 회전에너지도 C-C 결합의 15.1kJ/mol, C-O 결합의 11.3kJ/mol에 비해 S-O 결합은 0.8kJ/mol 이하로 상당히 작아 siloxane 결합은 움직이기 쉽다. 이 때문에 실리콘 폴리머 사이의 간격은 커서 점유 공간은 상당히 크게 되어 있다.
dimethyl silicone 사슬의 분자구조는 Si-O 결합 6개가 1회전하는 나선구조이다.
이 때문에 실리콘 폴리머의 표면은 대부분 소수성인 methyl기로 덮여 있고 표면에너지가 낮다. 실리콘 폴리머는 분자간력이 작기 때문에 소포성, 이형성, 발수성, 큰 압축률, 높은 기체 투과성, 낮은 온도의존성을 가지며 내한성이 우수하다. 이러한 실리콘의 독특한 성질은 그 구조로부터 유래한 것이라 할 수 있다.
4. 실리콘의 구조와 물성
폴리실록산과 유기 폴리머의 가장 일반적인 분자구조를 가진 polydimethylsiloxane과 polyethylene을 [그림 6]에 비교하였다. polyethylene은 탄소 원자가 일렬로 정렬되어 있는 주사슬에 수소 원자가 곁사슬로 결합하는 구조이다. 이에 비하여 polydimethylsiloxane의 주사슬은 규소(Si) 원자와 산소(O) 원자가 교대로 결합한 구조이며 곁사슬에 유기기인 methyl기가 결합하고 있다.
먼저 한 개 polysiloxane 분자의 성질을 확인하고, 그다음으로 polysiloxane 분자의 집합체로서 성질을 고찰하고자 한다.
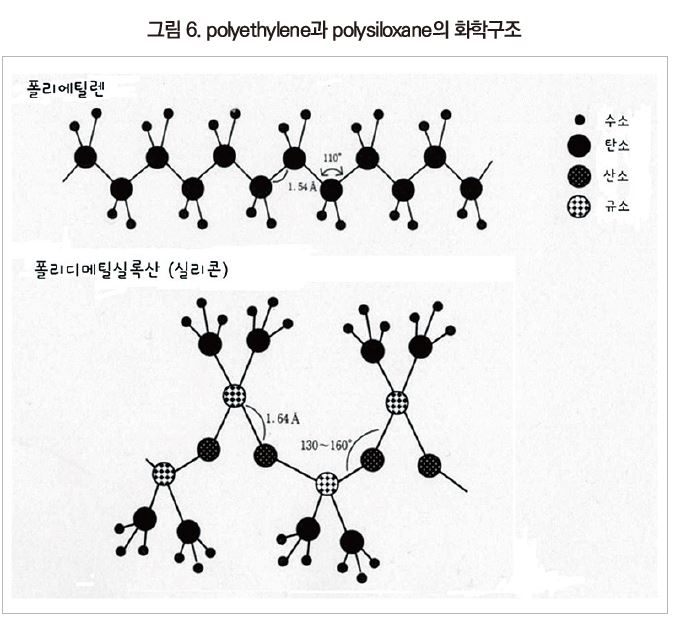
4.1 높은 유연성
Polysiloxane 주사슬 제1의 특징으로 유기 폴리머에 비하여 움직이기 쉬운, 즉 유연성이 높은 것이다. [그림 6]에 polyethylene과 polydimethylsiloxane 주사슬을 구성하는 원자간 거리와 결합각이 나와 있다. polyethylene의 C-C 결합거리 1.54Å에 비하여 polysiloxane의 Si-O 결합은 1.64Å으로 좀 더 길다. 더욱이 결합각이 polyethylene의 110°에 비해 polysiloxane의 Si-O-Si 결합각은 130~160°로 크다. 이것은 polysiloxane의 주사슬이 회전하기 쉬운 것을 나타내고 있다.
한 개 폴리머 분자의 움직임은 [그림 7]과 같이 ‘원자간 결합의 회전’에 의해 생긴다.
그중에서 주사슬의 결합(silicone의 경우 Si-O 결합)의 회전이 곁사슬(Si-C 결합이나 C-H 결합)보다도 폴리머 전체의 움직임에 크게 기여한다. 분자 전체의 회전이나 이동도 있을 수 있지만, 이것은 분자 집합체의 성질로서 고찰해야 할 것이다. 이와 같이 polysiloxane 주사슬은 C-C 결합으로 구성된 유기 폴리머보다 훨씬 회전하기 쉽기 때문에 폴리머 분자 전체가 움직이기 용이하게 된다.
siloxane 주사슬의 유연성에 관한 위의 설명은 P.J.Flory가 RIS(Rotational someric State Analysis)에 의해 주사슬 결합의 회전이 폴리머의 변형에 최대로 기여한다고 가정하여 이론계산으로 얻은 결론 ‘polysiloxane 사슬은 굴곡성이 크다’를 바탕으로 하고 있다. 최근 들어 결합의 회전에 결합각의 변형 이론이 더해져, 폴리실록산에서의 Si-O-Si 결합각 변형에너지는 1kcal/mol 정도로 매우 낮기 때문에 기존의 이론이나 실험을 뒷받침하고 있다.
Polysiloxane 주사슬의 제2의 특징은 열적 안정성이다. 유기 폴리머의 주사슬은 C-C나 C-O 결합으로 구성되어 있는 것이 많으며, 이들 결합에너지는 각각 85kcal/mol, 81kcal/mol이다. 이에 비해 실리콘 주사슬의 Si-O 결합에너지는 106kcal/mol로 유기 폴리머의 주사슬 보다 약 20kcal/mol 높다. 주사슬의 절단이 폴리머의 재료 특성에게 주는 영향이 곁사슬보다 크며, 이 차이에 의해 polysiloxane은 매우 높은 열안정성을 발휘하고 있다.
한편, 폴리머 실용상의 내열성에는 이 열적 안정성 외에 산화 등에 대한 화학적 안정성도 고려할 필요가 있다. polydimethylsiloxane의 경우에는 곁사슬의 산화나 주사슬의 재배열 반응이 있기 때문에 siloxane 결합의 열적 안정성의 한계 이하 온도까지만 사용할 수 있다.
4.3 주사슬의 이온성
Polysiloxane 주사슬 제3의 특징은 이온성이 높은 것이다. Si 원자는 주기율표에서는 탄소와 같은 14족이며, 탄소보다 금속성이 크고 주위의 전자를 끌어당기는 세기가 작다(전기음성도가 작다). 그 때문에 주사슬 주위의 전자는 산소 원자의 주변에 편재하여 규소(+), 산소(-)로 분극한 구조를 가진다[그림 10].
주사슬의 이온성이 높은 것은 주사슬끼리 당기는 힘(응집력)이 높다는 것을 의미하며, 또한 이온성이 높은 재료(무기 재료 등)와의 친화성도 높아진다. 그리고 polysiloxane의 이온성이 높은 것은 주사슬이 이온적 공격(산, 염기에 의해 반응)에 대해서 반드시 강하지 않다는 것도 의미한다. 중성 분위기하에서 매우 높은 내열성을 나타내는 polysiloxane도 산이나 염기가 존재하면 저온에서도 쉽게 분해하게 된다.
4.4 주사슬과 곁사슬의 대비
Polydimethylsiloxane 곁사슬은 methyl기로 polyethylene 곁사슬인 수소보다 점유 체적이 크기 때문에 그만큼 곁사슬의 성질이 폴리머에게 주는 영향이 크다.
polysiloxane 주사슬이 무기 Si-O 결합으로 구성되어 있는 데 비해, 곁사슬 methyl기는 전형적인 유기 성질을 가지고 있다. 즉 전자편향이 적고 비이온성이다. 그 때문에 표면에너지가 낮고 응집력도 작다. 주사슬이 친수성(hydrophilic)인 데 반하여 곁사슬은 소수성(hydrophobic)을 나타낸다. 동일한 폴리머 내에 이와 같이 대조적인 주사슬과 곁사슬이 같이 포함되어 있기 때문에, polysiloxane은 독특한 특성을 나타낸다.
4.5. 분자 집합체로서의 거동(발수 효과)
Polydimethylsiloxane은 이온성이 높고 응집력이 큰 주사슬과 비이온성이며 응집력이 약한 곁사슬로 구성되어 있다. 극히 소량(단분자층 또는 그 이하)의 polydimethylsiloxane이 수면이나 금속 표면 등의 재료상에 있는 경우에는 polysiloxane끼리의 응집력보다 poly siloxane과 접촉하고 있는 재료와의 응집력이 커진다.
그러한 경우 이온성이 강한 주사슬에 의해 polysiloxane과 재료가 접촉하며, siloxane 결합과 재료표면 사이에 수소결합이 형성된다. 그 결과 2개의 methyl기는 윗쪽을 향하게 되며, 표면을 보면 siloxane 주사슬은 보이지 않고 methyl기만으로 덮여 있는 것과 같이 된다[그림 12]. 실리콘을 도포하여 발휘되는 발수 효과는 이러한 결과에 따른 것이다.
두껍게 덮인 실리콘이나 벌크 액상 실리콘 중의 polysiloxane은 폴리머 간의 상호작용밖에 없다. 여기서 가장 안정한 polysiloxane의 형상은 나선구조인 것으로 알려져 있다[그림 13]. 주사슬 실록산 결합(-Si-O-Si-)은 나선 내부를 향하고, 이온성이 높은 주사슬 끼리의 인력은 오직 나선구조 내부에서만 일어나고 있다. 나선 외부로 나와 있는 것은 상호작용이 적은 methyl기이다.
나선 형상은 주사슬의 이온성에 의한 분자 내 작용하는 인력에 의해 유지되고 있다. 분자간 인력은 나선의 외부에 나와 있는 것이 methyl기 때문에 작다. 그리고 polysiloxane 주사슬은 유연성이 높아 격렬하게 움직이고 있다. 다른 분자에 대한 구속력이 낮은 채로 움직이고 있기 때문에 실리콘 폴리머 간 틈새가 벌어지게 된다. 즉, 실리콘 폴리머가 한 개가 차지하는 공간이 커지는 것이다.
polysiloxane 집합체의 이러한 성질에 의해 다른 고분자와는 다른 여러 가지 특성이 나온다. 예를 들어 낮은 증발 잠열, 낮은 융해열, 낮은 비점(같은 분자량의 유기 화합물과의 비교), 낮은 Tg 등은 분자간력이 약한 것으로 설명할 수 있다. 실리콘의 내한성이 좋은 것은 저온에서도 응고하지 않는 오일, glass 상태가 되지 않는 고무를 의미하며 낮은 Tg와 응고점에 달려 있다. 실용화되어 있는 폴리머 중에서 가장 gas 투과성이 높은 것, 액체로서 압축률이 높은 것 등도 실리콘의 응집력이 작고 폴리머 간의 틈새가 큰 것으로 설명할 수 있다.
4.6 Polysiloxane의 화학반응성
Polysiloxane 주사슬은 이온성이 높고, 산이나 염기에 의해 절단되기 쉬운 것은 앞서 언급하였으며, 이 성질은 polysiloxane 제조에 적극적으로 사용되고 있다. 그러나 제품의 배합을 중성으로 유지하지 않으면 실리콘 최대의 특징인 내열성을 손상시키는 경우가 있기 때문에 실리콘 제품의 설계나 사용에 있어서 이 성질이 제약조건이 되는 경우가 있다.
Si 원자에 직접 결합한 관능기의 반응성을 보면, C-H, C-halogen, ether, ester 등은 유기 화합물에서 비교적 안정한 결합이지만, 이들 탄소 원자가 Si 원자로 교체되면 반응성이 급격히 높아진다. 쉽게 가수분해하는 결합으로 알려져 있으며, 이들은 가수분해하여 silanol기(Si-OH)가 된다.
이들 관능기는 silanol기와도 반응하여 siloxane 결합을 생성한다.
silanol기는 고온이나 산·염기 조건 하에서는 자기들끼리도 반응하여 siloxane 결합을 생성한다.
이들 결합의 반응성은 실리콘의 제조뿐만 아니라 가교에도 널리 이용되고 있다. Si-H 결합은 고온이나 알칼리성 조건 하에서 위와 마찬가지로 반응을 한다.
이 Si-H기에 특이하면서도 유용성이 높은 것은 빛, 방사선, radical, 천이금속 촉매 등의 존재 하에서 일어나는 불포화결합의 부가반응(hydroxylation 반응)이다.
Si-H 결합은 도입 수단으로 실리콘 제조에 사용되고 있을 뿐만 아니라, 가교반응에도 중요한 반응이 되고 있다. 탄소 원자를 삽입하여 Si 원자에 결합한 유기 관능기는, 가운데의 탄소 원자 수가 적은 경우에 Si 원자의 영향을 받는다. 염소화 유기기에 있어 화학적 반응성은 아래와 같은 순서로 낮아진다.
가운데 탄소 원자 수가 3 이상이 되면 유기 화합물의 특성에 가깝기 때문에 polysiloxane에 도입하는 유기 관능기는 대부분의 경우 3개 이상의 탄소 원자를 사이에 두고 있다.
5. 실리콘의 제조
5.1 실리콘 제조공정
실리콘의 주성분인 Si 원자는 지구상에 다량으로 존재하는 규석(SiO2)을 원료로 하고 있다. 규석에서 Si 원자는 4개의 산소 원자와 결합하고 있으며, [그림 15]와 같이 2개의 산소 원자를 제거하고 유기그룹을 결합시키면 실리콘 폴리머가 된다.
좀 더 자세한 제조 공정은 [그림 16]에 나타내었으며, 그 순서는 다음과 같다.
(1) 실리카(SiO2)로부터 모든 산소 원자를 제거하여 금속 규소(Si)를 제조한다
(2) 금속 규소(Si)에 2개의 유기그룹과 2개의 염소를 결합시켜 유기클로로실란 단량체를 제조한다.
(3) Cl을 O로 치환시키고, 동시에 주사슬에 (-Si-O-)를 형성시켜 저분자 dimethyl siloxane을 만든다
(4) 저분자 dimethyl siloxane을 중합하여 고분자 dimethyl siloxane을 제조한다.
그림에서 보듯이 원료인 규석(SiO2)에 함유되어 있던 산소 원자(O)를 전부 제거하고 나서, 다시 산소 원자를 도입하는 공정을 실시하고 있다. 즉 화학적으로 4가의 규석을 금속 규소인 0가로 환원하고 다시 산화하여 4가에 되돌리고 있다. 대부분의 원소를 산화하는 것은 간단하지만, 역반응인 환원에는 에너지가 필요하다. 실제 금속 규소로의 환원에는 다량의 전력이 필요하므로 금속 규소는 저가의 원료가 아니다.
금속 규소로의 환원을 거치는 것은 규소 원자에 유기기를 도입하기(Si-C 결합 생성) 위해서이다. Si-C 결합의 도입 방법에는 여러 가지가 있지만, 대량의 단량체를 경제성 있게 제조하려면 위의 직접법만큼 우수한 공정은 없다.
5.2 유기클로로실란의 제조
실리콘 제조를 위해 사용되고 있는 Si 원자에 결합하는 유기기로 methyl기가 압도적으로 많다. methyl기는 금속 규소와 chloromethyl로부터 Cu 촉매 하에서 가열하여 합성되고 있다. 이 방법은 1940년대 E.G.Rochow에 의해 개발된 ‘직접법’이다.
직접법의 개발에 의해 실리콘의 산업적인 응용을 위한 규모와 경제성에서의 실리콘 제조가 처음으로 가능해졌다. 그 후에 금속 규소를 거치지 않는 실리콘 합성이 검토되었지만 직접법만큼 우수한 방법을 찾아내지는 못했다.
직접법에서는 dimethyl chlorosilane만이 아니고 아래와 같은 수많은 규소화합물을 생성하며, 이들 대부분은 실리콘공업에 사용되고 있다.
직접법으로 생성한 dimethyl chlorosilane는 정류 공정에 의해 분리되어 여러 가지 용도로 사용되고 있다. 비점이 가까운 화합물이므로 이들을 분리하기 위해서는 몇 단계의 분류 과정이 필요하다. dimethyl chlorosilane은 고분자량의 사슬상 폴리머 원료이므로 특히 고순도로 분리하고 있다.
methyl기 다음으로 용도가 많은 것은 phenyl이다. phenyl chlorosilane류도 직접법으로 제조되지만, Fridel-Craft 반응으로 제조되는 것도 있다. 실리콘 고무에서 중요한 관능기로서 vinyl기가 있다. 이것은 Si-H기와 acetylene으로부터 하이드로시릴화반응에 의해 제조되고 있다.
클로로실란류의 Si-Cl 결합은 물이나 알코올 등 활성수소를 가진 화합물과 쉽게 반응한다. 물과 반응하여 실리콘 폴리머가 얻어지는 것이 많으며, 알코올과 반응에서 가수분해나 실라놀(silanol)기와 축합 반응성이 풍부한 관능기를 얻을 수 있다.
이것은 실란커플링제(silane coupling agent)의 무기질 반응용 관능기나 실리콘 고무의 가교제 성분으로 중요한 역할을 하고 있다.
5.3 실리콘 수지
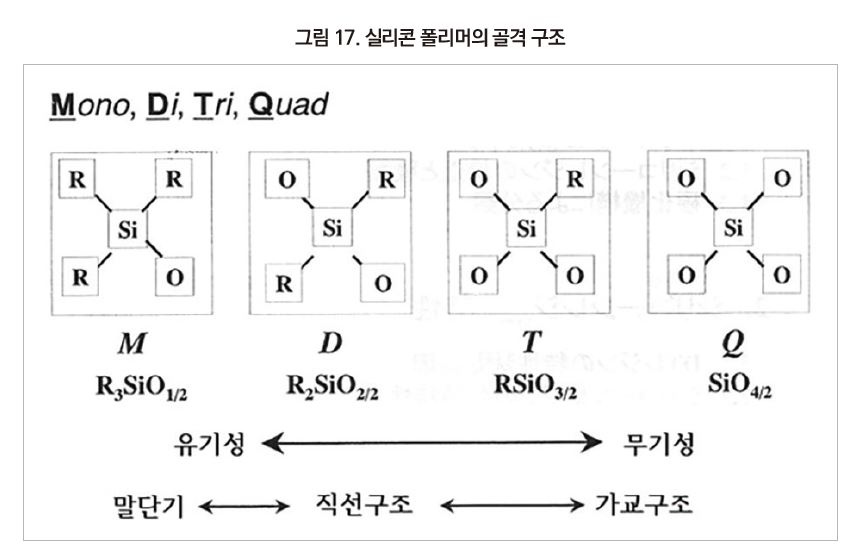
실리콘 수지의 구조는 아래와 같이 4개의 단위로 구성되어 있다.
Si 원자는 C원자와 같은 주기율표 14족의 원소이며, sp3 혼성궤도에 의해 정사면체의 구조로 4개의 연결고리를 가지고 있으며, Si 원자에 결합하고 있는 산소 수에 따라 M, D, T, Q가 붙여진다. 유기 치환기 R은 methyl, phenyl기가 일반적이며, R이 많을수록 유기성을 띠고 O가 많을수록 무기성을 나타낸다.
R3SiO1/2의 O가 1/2인 것은 2개의 Si가 공유하고 있다는 표현이며, R3SiO1/2은 연결기인 O가 1개이므로 주로 말단기이며, O가 2개인 R3SiO2/2는 사슬상의 구조를, 그리고 O가 3개 이상은 가교구조를 가진다. 실리콘 수지의 평균 구조식은 아래와 같다.
수지의 영역인 R3SiO3/2는 T단위 부근이며, DT수지의 합성법은 아래와 같다.
실리콘의 구조 중 D인 R3SiO2/2은 주로 Silicone Oil이나 Silicone flake이며, 수지 영역은 T인 R3SiO3/2가 주로 사용된다. 하지만 수지는 D와 T가 혼합한 DT형이 일반적이며, 2차원과 3차원이 섞여 있다.
그리고 DT 수지와 MQ 수지의 차이로, DT 수지는 단독으로 피막형성 능력을 가지고 있다. 각종 코팅제로 사용되며 표면보호, 발수, 발유, 내후성, 절연, 내약품성 등의 기능을 발휘한다. MQ 수지는 피막형성 능력이 없으며 경화되면 부스러진다. 실리콘 점착제(PSA), 실리콘 검(gum)의 용도로 사용되며, 부가 경화형과 과산화물 경화형이 있다. 그 이외에도 DQ, MT, MDT 등 필요에 따라 여러 가지 타입이 있다.
실리콘 수지는 methyl/phenyl 중 methyl이 많을수록 무기성이며, phenyl이 많을수록 유기성을 띤다. 가교 밀도는 사슬상의 D가 많을수록 유연하며, 수지상인 T가 많을수록 가교성이 높다. 또한 분자량이 낮을수록 취약하고 깨지기 쉬우며, 높을수록 가휘성이 높아 잘 구부러진다. silanol기(SiOH) 함유량이 적을수록 피막 응력이 낮고, 많을수록 경화 속도가 빠르다. 유기 치환기에 따른 특성을 비교하였다.
실리콘 수지의 특성으로 주사슬의 결합에너지가 높다.
주사슬 결합에너지: Si-O(108Kcal/mol), C-C(85Kcal/mol)
곁사슬이 phenyl계인 경우 내열 안정성이 높으므로 내열도료로 사용된다.
250℃에서 50wt.% 분해 시간: Me-Si(>10000 hr), Ph-Si(>100000 hr), Et-Si(6 hr), Pr-Si(2 hr)
5.4 실리콘 폴리머의 제조
실리콘 폴리머 중에서 널리 사용되고 있는 사슬상 폴리머의 대표인 폴리디메틸실록산의 제조에 대하여 서술하고자 한다.
사슬상 실리콘 폴리머의 주원료는 디메틸클로로실란(CH)3SiCl2이다. 이것을 가수분해한 후 중화, 탈수를 반복하면 사슬상 폴리머를 얻을 수 있으며, 공업적으로는 2단계로 나눌 수 있다. 즉 디메틸클로로실란을 가수분해하여 저분자량 실리콘을 제조하는 가수분해공정과 고분자량 실리콘 폴리머를 제조하는 중합공정이다.
디메틸클롤로실란을 다량의 물로 가수분해하고 부산물인 염화수소를 세척에 의해 제거한다. 생성물은 환상 디메틸실록산과 사슬상 디메틸실록산의 혼합물이다.
환상체은 3~6량체 정도의 저중합도 디메틸실록산이 많지만 실제로는 중합도 50 이상까지 분포하고 있다. 사슬체는 평균 중합도와 분포 모두 환상체보다 높다. 환상체와 사슬체의 비율이나 각각의 중합도는 가수분해 시의 pH 등으로 어느 정도 조정이 가능하다. 이 저분자량 실록산 혼합물로부터 증류에 의해 저중합도의 환상체(주성분 4~6량체)가 분리된다.
환상 실록산은 중합도 수천 이상의 고분자량 실리콘의 제조에 필요하다. 환상 실록산을 취한 후 나머지는 사슬상 실록산과 큰 환상 실록산의 혼합물이다. 이것들은 말단 silanol 관능성 실록산이나 비교적 저분자 실록산 제조에 사용된다.
다음, 실리콘 폴리머의 중합으로, 실리콘 폴리머의 주사슬은 이온성이 강하다. 그 때문에 산이나 염기의 존재 하의 고온에서 절단과 재결합이 쉽게 일어난다.
실리콘 폴리머에는 이 성질을 중합에 이용하고 있다. 수산화칼륨을 촉매로 환상 디메틸실록산의 중합을 예로 보면, 개시반응은 환상체의 개환에 의한 칼륨실라노레이트의 생성이다.
생성된 칼륨실라노레이트는 환상체를 개환하면서 분자량을 증대한다(생장반응).
칼륨실라노레이트는 환상체의 개환과 동시에 생장한 폴리디메틸실록산으로부터 환상체 생성(해중합/분자내 전이)이나 실록산끼리의 전이도 일으킨다.
이와 같이 중합 중에는 분자량 증대 반응뿐만 아니라 해중합도 동시에 일어나고 있다. 실록산 결합(-Si-O-Si-)이 random하게 절단·재결합을 일으키고 있다. 산 염기 중에서 이 반응을 계속하면 실록산의 분자량 분포는 열역학적 평형상태에 도달한다. 이러한 중합을 재배열 반응 또는 재평형화 반응이라 한다.
평형상태에서 환상체와 사슬체의 비율 및 분자량은 온도, 촉매 농도, 실록산 농도, 수분량, 곁사슬 종류, 단관능성 실록산의 단위 농도 등에 의존한다. 일반적인 폴리디메틸실록산에는 평형 시 다량의 환상체를 포함하고 있다. 분자량은 단관능성 실록산 단위의 첨가량으로 조정할 수 있다. 관능성이 없는 폴리디메틸실록산에서는 헥사메틸디실록산의 첨가량으로 분자량을 조정한다.
촉매로서 수산화칼륨을 예로 들었지만 다른 염기성 촉매에서도 마찬가지로 반응이 일어난다. 디메틸 포름아미드(DMF)나 디메틸술폭사이드(DMSO)와 같은 극성용매를 소량 첨가하면 촉매활성점을 용매화하여 중합 활성을 부여할 수 있다. 또한 염산 및 황산이나 활성백토 등은 산촉매로서 작용하는 촉매이다.
폴리디메틸실록산의 경우 산 염기 모두에서 중합할 수 있지만 곁사슬의 종류에 따라 사용할 수 있는 촉매는 한정되어 있다. 예를 들어, phenyl기를 함유한 경우에 산 촉매, Si-H기를 포함한 경우에는 염기성 촉매를 사용하면 중합 중에 이들 그룹이 분해하여 gel화 되기 쉽다. 중합은 촉매를 중화시킴으로써 정지되며, 부산물인 환상체는 스트립핑으로 제거하여 폴리디메틸실록산의 제조를 완료한다.